Core Tools Automotive, L’importanza degli strumenti “Core”
Continuiamo il nostro percorso nel mondo Automotive, mercato che è riferimento per gli elevati standard Qualitativi che le case automobilistiche richiedono a tutta la catena di fornitura.
Introduciamo il concetto di Core Tools Automotive, ovvero gli strumenti principali da conoscere, implementare ed applicare continuamente per chi è certificato IATF e per chi lavora nel settore di riferimento.
Riportiamo di seguito in formato elenco i Core Tools Automotive:
- APQP: Advanced Product Quality Planning and the Control Plan
- PPAP: Production Part Approval Process
- FMEA: Failure Mode & Effect Analysis
- MSA: Measurement System Analysis
- SPC: Statistical Process Control
All’interno della Specifica Tecnica IATF si trovano riferimenti frequenti ai Core Tools Automotive e come anticipato la specifica IATF ne impone la conoscenza, l’applicazione ed anche la capacità di verificare la corretta applicazione dei Tools.
Ma Quale è l’utilità dei Core Tools Automotive IATF?
Lo scopo principale è promuovere il miglioramento delle performance delle organizzazioni, tenendo sotto controllo i processi di sviluppo prodotto e processo ed i processi produttivi che concorrono alla realizzazione del prodotto ed erogazione del servizio.
L’utilizzo dei Core Tools Automotive è necessario quindi per monitorare i processi definiti Core delle Aziende ed identificati come gli step critici per prevenire l’insorgere di problematiche tecniche in esercizio.
Queste fasi di processo sono rappresentate da:
- Progettazione e Sviluppo
- Rilascio del Progetto in Produzione
- Industrializzazione
- Produzione
- Controllo e Misurazione
Inoltre, la conoscenza dei Core Tools Automotive permette alle organizzazioni di creare competenza e Know How utili per comprendere le aspettative, le esigenze e le richieste dei Car Makers offrendo anche un benchmark interno rispetto alle guide ed ai manuali di riferimento.
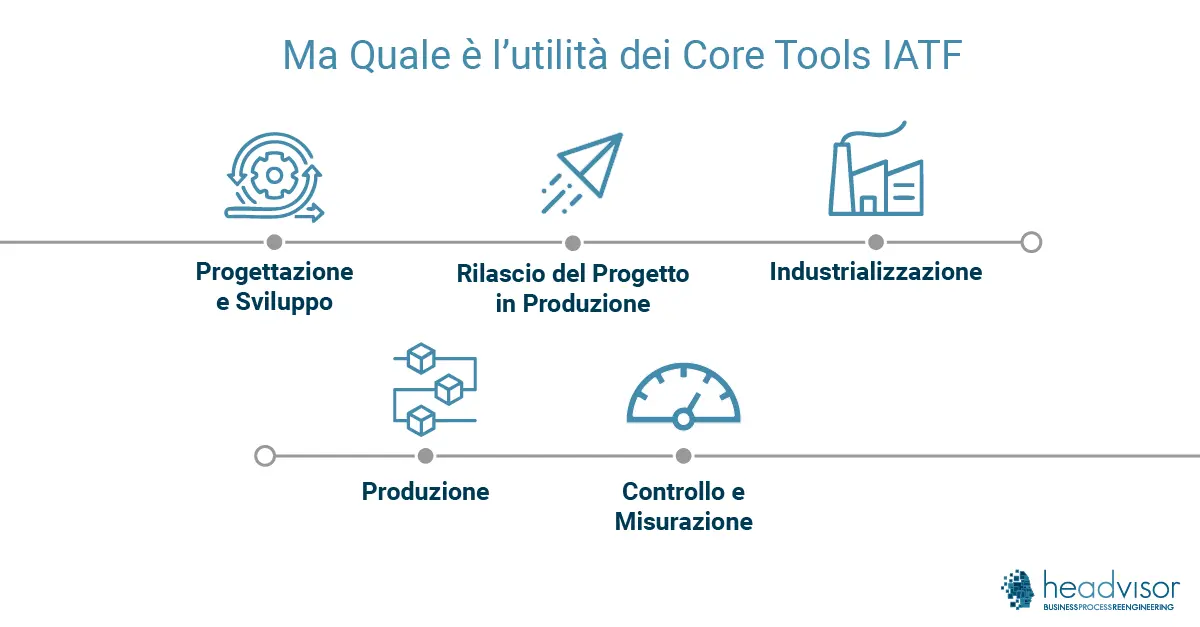
Dove si possono trovare i manuali dei Core Tools Automotive?
L’ente AIAG ha creato dei manuali di riferimento per l’applicazione dei Tools. Questi manuali poi possono essere richiamati dai Capitolati di Fornitura dei Clienti e dei Car Makers aggiungendo dei requisiti o delle specificità.
Di fatto quindi i Manuali AIAG, così come i Manuali VDA per alcune tematiche specifiche, costituiscono dei riferimenti richiamati nella documentazione contrattuale dei Car Makers.
Riepiloghiamo quindi:
Nel settore automotive, i Core Tools Automotive sono quindi strumenti utilissimi per assicurare la qualità e l'efficienza dei processi produttivi. Questi strumenti sono stati sviluppati per supportare le aziende nella gestione della qualità, nella prevenzione dei difetti e nel miglioramento continuo.
I principali Core Tools Automotive sono cinque:
1. APQP Advanced Product Quality Planning and the CP Control Plan
L'APQP è un processo strutturato che aiuta le aziende a sviluppare prodotti di alta qualità in modo efficiente. Questo strumento prevede la pianificazione anticipata della qualità del prodotto, dalla fase di progettazione fino alla produzione. L'obiettivo è identificare e risolvere potenziali problemi prima che si verifichino.
Il Control Plan CP è poi lo strumento che viene utilizzato per fissare e definire i Controlli necessari al fine di evitare il presentarsi dei potenziali problemi.
Un processo di APQP è articolato in 17 task differenti, che possono essere svolti non in sequenza temporale:
- Key Stakeholders Meeting: incontro di tutti i portatori di interesse per il processo, prodotto o progetto;
- Technical Review: meeting con i fornitori per valutare le offerte tecniche e le richieste del cliente;
- Risk Assessment: valutazione del rischio associato alla scelta di ogni fornitore;
- Supplier Program Reviews: quattro meeting di verifica del SAL di progetto;
- Timing Charts e Open Issues: per valutare la coerenza tra planning ed evidenziare le criticità di ogni componente;
- Feasibilty Assessment Letter: documenti associati ad ogni Supplier Program Review;
- Flow Chart: per visualizzare la sequenza e la correlazione tra le attività del processo;
- DFMEA: analisi FMEA del Design
- Design Review: analisi del design definito
- Gage/Tooling Equipment Review: attività per garantire che il processo produttivo del fornitore sia allineato;
- GP11 – Pre-Prototype & Prototype Process: produzione della documentazione che accompagna ogni componente;
- PFMEA Development: analsi FMEA di processo per l'intero processo;
- Control Plan: documento che definisce i controlli dimensionali, funzionali ed estetici per garantire pezzi conformi;
- GP12 – Early Production Containment: piano di controllo richiesto al fornitore;
- PPAP: Production Part Approval Process: attività di controllo per determinare che ogni requisito richiesto sia stato rispettato;
- Run@Rate: attività di one day production e verifica della capacità produttiva del fornitore;
- Lesson Learned: documento contenente tutte le problematiche precedenti su prodotti per evitare la stessa esperienza sul prodotto in sviluppo;
2. PPAP (Production Part Approval Process)
Il PPAP è un processo utilizzato per dimostrare che un fornitore ha compreso e soddisfatto tutti i requisiti del cliente per i componenti prodotti. Questo strumento include la presentazione di documenti e campioni che attestano la conformità del prodotto ai requisiti specificati.
Utilizzato per la prima volta da Ford e General Motors è adesso adottato da tutte le maggiori industrie operanti nel settore Automotive mondiale, per garantire che i fornitori di componenti abbiano processi produttivi omologati.
Un processo PPAP produce una serie di documenti utili a garantire e provare che un fornitore ha la capacità di soddisfare i requisiti di riproducibilità e qualità.
3. FMEA (Failure Mode and Effects Analysis)
La FMEA è una metodologia sistematica per identificare e analizzare i potenziali guasti di un prodotto o processo.
Questo strumento aiuta a valutare l'impatto dei guasti e a implementare azioni correttive per ridurre il rischio di difetti.
4. MSA (Measurement System Analysis)
L'MSA è l’insieme di strumenti di analisi utilizzati per valutare l'affidabilità e la precisione dei sistemi di misurazione. Questo strumento è fondamentale per garantire che i dati raccolti siano accurati e ripetibili, riducendo così le variazioni nei processi produttivi.
5. SPC (Statistical Process Control)
L'SPC è una metodologia che utilizza tecniche statistiche per monitorare e controllare i processi produttivi. Questo strumento aiuta a identificare le variazioni nei processi e a implementare azioni correttive per mantenere la qualità del prodotto.
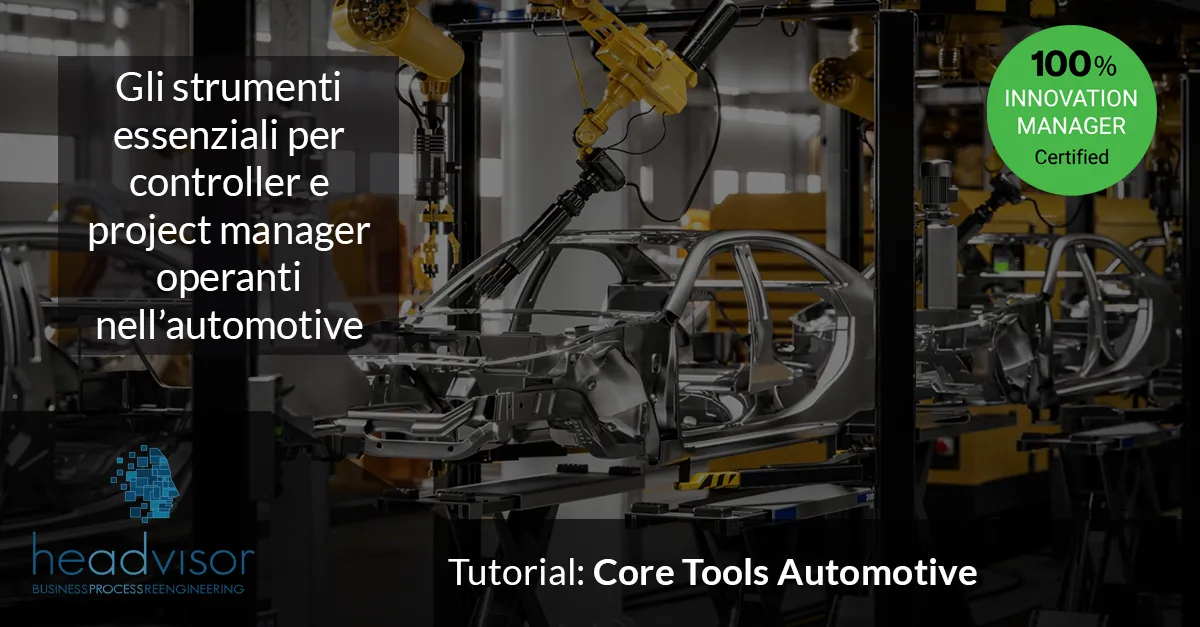
Conclusione
L'implementazione efficace dei Core Tools Automotive è essenziale per le aziende del settore Automotive che desiderano mantenere elevati standard di qualità e competitività. Questi strumenti non solo aiutano a prevenire i difetti, ma promuovono anche il miglioramento continuo e l'efficienza operativa.
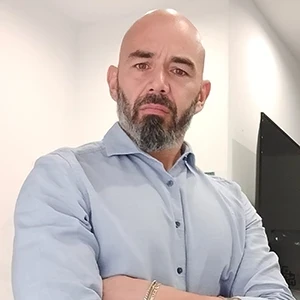
Bruno Bonera
Operations & Quality Manager
Quality Manager con circa 20 anni di esperienza in 4 organizzazioni, nell’ambito di:
- Certificazioni ISO (9001, 14001, IATF, EN9100)
- Quality Key Account per FCA , Iveco , CNH
- Metodologie 8d, SPC , FMEA, PPAP, APQP, MSA, WCM, Continuous improvement, Project Management
- Progetti Lean, audit di 1a e 2a parte, mappatura processi e implementazione ERP / Eccellenza Operativa
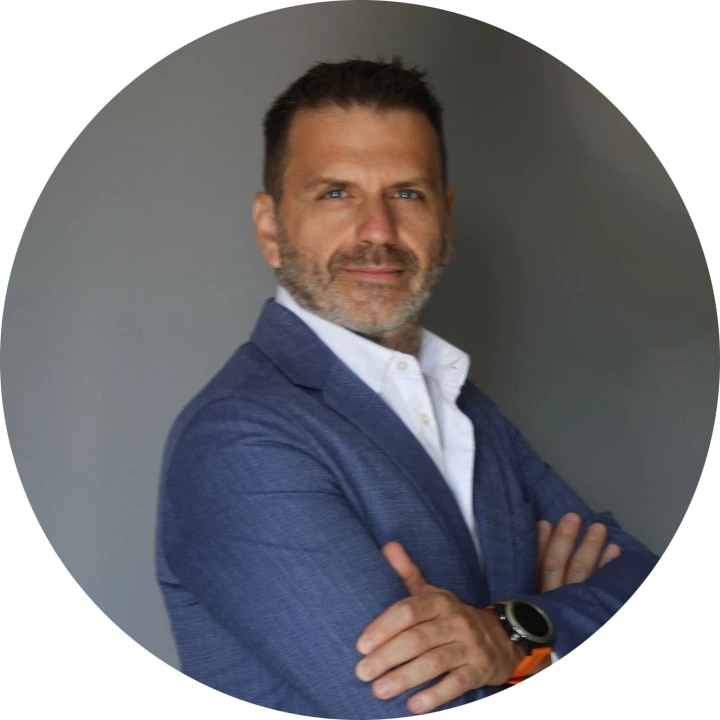
Stefano Patelli
Co-Founder e Direttore Operativo di Polo Innovativo srl
Innovation Manager, Consulente e aziendalista in materia di strategia industriale volti alla Digitalizzazione e innovazione dei processi industriali e aziendali. Progettazione e analisi di database complessi, analisi degli strumenti d'impresa BI e System integration gli strumenti di uso più frequente.
Chiedici una consulenza gratuita
I nostri esperti sono a tua disposizione!
Gli operatori circolano nei reparti della tua azienda con fogli di carta? La pianificazione della produzione è manuale o effettuata con Excel?
Sai esattamente quanto è il tuo livello di produzione? Quanto scarto produci? Quante rilavorazioni per inefficienze? Quante materie prime impieghi?
Tramite un processo di efficientamento è possibile implementare soluzioni tengibili, per ottimizzare al meglio ogni processo e migliorare il livello di efficienza.
Tutto il nostro team è a tua disposizione, per qualunque esigenza.
Leggi i Tutorials più recenti
Strumenti per efficientare le imprese
Core Tools Automotive: l’importanza degli strumenti “Core”
Core tools automotive: gli strumenti chiave da conoscere per lavorare come controller, project manager e dirigenti nel settore automotive.... [Continua a Leggere]
Metodo Hoshin Kanri per la pianificazione strategica
Hoshin Kanri è un metodo di gestione strategica della lean production che permette di allineare gli obiettivi strategici di un'azienda con le sue operazioni quotidiane... [Continua a Leggere]
ESRS: gli standard europei per il reporting sulla sostenibilità
ESRS: gli standard che definiscono le linee guida per la rendicontazione sostenibile delle aziende in Europa. Scopri cosa sono in questo articolo... [Continua a Leggere]
CSDDD o CS3D: cosa è e cosa prevede la nuova direttiva europea
CSDDD o CS3D perché è nata questa normativa europea? a chi è rivolta? entro quando entrerà in vigore?... [Continua a Leggere]
Sostenibilità aziendale: come migliorare le performance sostenibili
La sostenibilità aziendale è un concetto fondamentale per le aziende moderne. Come implementare soluzioni sostenibili per il prossimo futuro?... [Continua a Leggere]
Balanced scorecard: la guida completa
Balanced Scorecard BSC è la scheda di valutazione bilanciata per la gestione strategica e la misurazione dei risultati aziendali nelle diverse aree.... [Continua a Leggere]
Analisi PEST e analisi PESTEL
Analisi PESTEL (anche conosciuta come PEST o PESTLE) permette di evidenziare tutti i fattori esterni che possano condizionare lo sviluppo di una azienda o business... [Continua a Leggere]
La Carbon Footprint aziendale: 9 tecniche e metodi per la stima degli impatti di emissioni in atmosfera
Carbon Footprint aziendale: tecniche e metodi per la stima degli impatti di emissioni in atmosfera e rendicontazione nel bilancio di sostenibilità... [Continua a Leggere]
Margine di Contribuzione: Cos’è, Calcolo ed Esempi
Il margine di contribuzione è un indice fondamentale per valutare la redditività dei prodotti creati dall'azienda. Leggi questo articolo per saperne di più... [Continua a Leggere]
Just in Time: efficienza in produzione e logistica
Il just in time è una strategia di gestione che permette di ridurre gli sprechi e rendere più efficiente e coordinato il reparto produzione.... [Continua a Leggere]
WBS (Work Breakdown Structure): cos'è e come utilizzarla
La WBS è lo strumento di ripartizione del lavoro per suddividerlo in compiti più piccoli e renderlo più gestibile, controllabile e accessibile.... [Continua a Leggere]
Break Even Point (BEP) - come calcolare il punto di pareggio
Il Break Even Point è una formula per calcolare il punto di pareggio. Il valore in cui i profitti e i costi di un’attività aziendale sono in equilibrio.... [Continua a Leggere]
Sistemi di Efficientamento organizzativo
Gli strumenti per efficientare la tua impresa
L'analisi e la mappatura dei processi di un'organizzazione, consentono di riorganizzare le attività, razionalizzare l'uso delle risorse, incrementare l’efficacia, l’efficienza ela produttività della struttura stessa.
I nostri servizi a supporto di imprese:
- Mappatura dei processi interni, gestionali e organizzativi
- Analisi e ottimizzazione delle prestazioni dei processi individuati
- Analisi e riduzione dei costi di gestione
- Ridefinizione dei processi con l'obiettivo di migliorare l'efficienza dell'organizzazione e delle sue prestazioni
- Progettazione di Innovazione tecnologica e digitalizzazione dei processi
- Progettazione di economia circolare