Cosa è l'indice OEE
Le aziende possono scoprire sistematicamente il potenziale di ottimizzazione attraverso gli indici di performance KPI, tra questi, l'OEE aiuta a dare una misura complessa e generale di tutto lo stato di salute dell'impianto o della linea produttiva.
Infatti grazie all'indice OEE come strumento di misura, l'efficacia del sistema è misurabile, paragonabile e quindi sia anche migliorabile in termini numerici.
Il valore OEE è costituito dai seguenti tre fattori:
- Disponibilità operativa
- Tempi di singola lavorazione
- Qualità del prodotto
L' OEE, Overall Equipment Effectiveness ("Efficienza complessiva della risorsa produttiva") è un indice di performance (KPI) per misurare la capacità produttiva di una azienda di produzione.
È un importante indicatore nella Lean Production per il mantenimento del controllo. L'indice OEE mette in risalto il livello di spreco delle risorse che devono essere corrette.
L'indice OEE tiene conto delle più comuni e importanti fonti di perdita di produttività nella produzione secondo la filosofia Kaizen, il che significa che la produzione può essere continuamente migliorata.
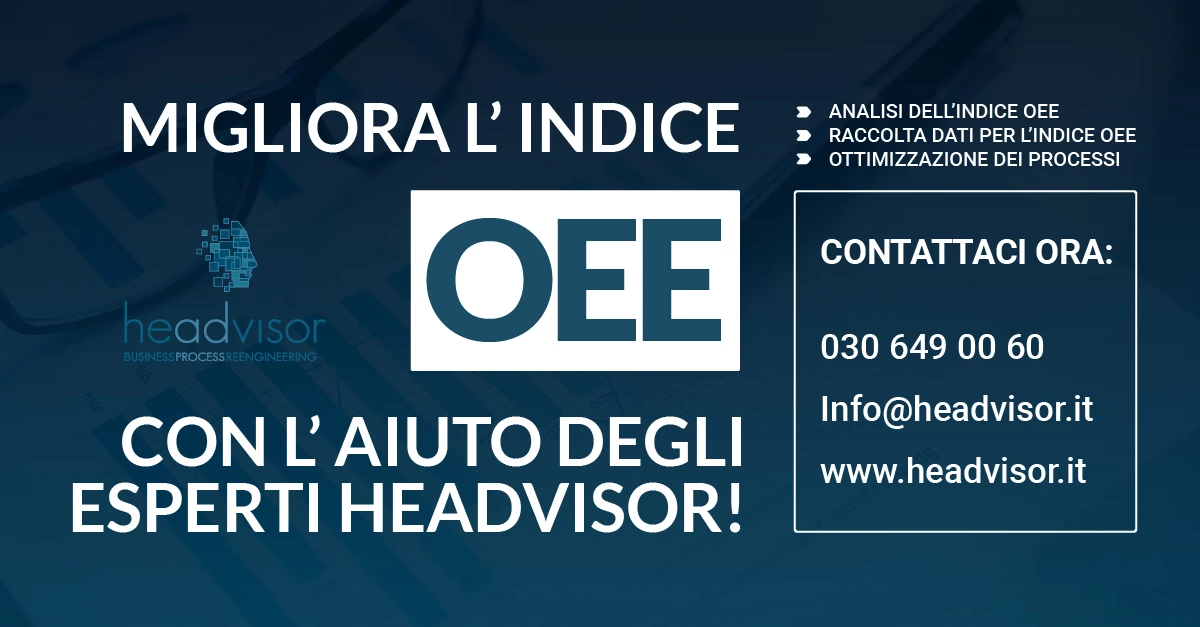
OEE calcolo
OEE formula: è il prodotto delle tre componenti fondamentali della performance
produttiva
Availability x Performance x Quality
-
Availability (Disponibilità):
Percentuale del tempo lavorato rispetto al tempo disponibile. Si utilizza il rapporto tra il tempo disponibile di lavoro dell'impianto (es il turno o la giornata o la settimana) rispetto al reale tempo in cui l'impianto ha prodotto valore eseguendo parti o semilavorati
-
Performance (Prestazione):
Percentuale di parti realmente lavorate rispetto alle parti teoricamente lavorabili. Nella pianificazione vengono calcolati i pezzi lavorabili a regime ottimale, eventuali riduzioni di tali performance indicano un calo produttivo
-
Quality (Qualità prodotta):
È il rapporto percentuale tra le parti conformi rispetto al totale delle parti prodotte. Si evidenziano in tal modo cali produttivi relativi a scarti o rilavorazioni che incidono sull'inefficienza generale
Esempio di calcolo indice OEE
Nell'impianto 1 è stata pianificata la produzione di un lotto di lavoro per 5.300 pezzi. Il tempo teorico di lavorazione per ogni pezzo è di 87 secondi.
L'impianto lavoro per 3 turni e per 5 giorni alla settimana. Teoricamente sarebbero necessari poco più di 16 turni lavorativi ipotizzando una efficienza teorica del 100%.
Infatti moltiplicando 5.300 pezzi per 87 secondi si ottengono 461.000 secondi che diviso un normale turno di 8 ore (8*60*60 = 28.800 secondi per turno) da come risultato 16,01.
Availability OEE
Nel primo turno viene fatto l'attrezzaggio completo per tutta la produzione del lotto e vieneconsumato un tempo di 90 minuti.
Inoltre tra accensione e avvio di macchina per inizio settimana sono necessari altri 35 minuti.
Durante tutto il turno vengono eseguite altre 3 verifiche in manuale sullo stato attrezzaggio e stato macchina costringono alla sospensione di lavoro per un totale di 24 minuti.
Per 12 volte scattano allarmi di vario genere (sicurezza, anomalia, check di pressione, ecc) per un totale di 28 minuti complessivi di sospensione lavoro.
Non vi sono fermi di manutenzione programmata e nemmeno di sostituzione parti e utensili.
Availability è quindi formato dal tempo teorico (480 minuti) sottratti tutti i fermi (90 + 35 + 24 + 28 = 177) per un tempo netto lavorato di 303 che corrisponde ad una efficienza percentuale della voce Availability del 63%
Performance OEE
Sempre mantenendo l'esempio appena descritto, nel tempo di Availability appena calcolato saranno posti in relazione il tempo teorico produttivo con i reali pezzi prodotti.
Quindi nei 303 minuti di disponibilità dell'impianto suddivisi per gli 87 secondi teorici, ne scaturisce una produzione teorica di 209 pezzi (esattamente calcolati in 303 minuti x 60 secondi a minuto / 87 secondi pezzo).
Poiché la reale produzione invece è stata di 181 pezzi, ne deriva che il rapporto tra teorico ed effettivo sarà 181/209 cioè un indice di Performance del 87%.
Quality OEE
Per finire durante il medesimo turno, dei 181 pezzi prodotti 4 sono stati scartati ed uno invece ha subito una rilavorazione a causa di un allarme che ha costretto ad un piccolo intervento manuale (di cui al punto Availability)
Ancora eseguiremo il medesimo rapporto tra i 181 pezzi lavorati rispetto ai pezzi conformi, 181 - 5 pezzi scartati (4 scarti e un rilavorato). Il valore che otterremo sarà 176/181 per un indice di Quality del 97%
OEE del turno
Finalmente per ottenere l'indice OEE del turno 1 sulla base del nostro esempio appena illustrato ne deriverà che: 63% (Availability) x 87% (Performance) x 97% (Quality) = 53%
È chiaro che in questo turno ha inciso pesantemente l'attrezzaggio di 90 minuti. Senza questo importante fermo il valore Availability sarebbe stato di 82%.
Volendo fare della semplice teoria, ipotizzando che le percentuali di Performance e Quality mantengano gli stessi valori, si potrebbe ipotizzare che l'intero indice OEE del turno ma senza l'attrezzaggio, avrebbe potuto essere 82% (Availability) x 87% (Performance) x 97% (Quality) = 69%.
Esempio di calcolo OEE su un giorno di 3 turni:
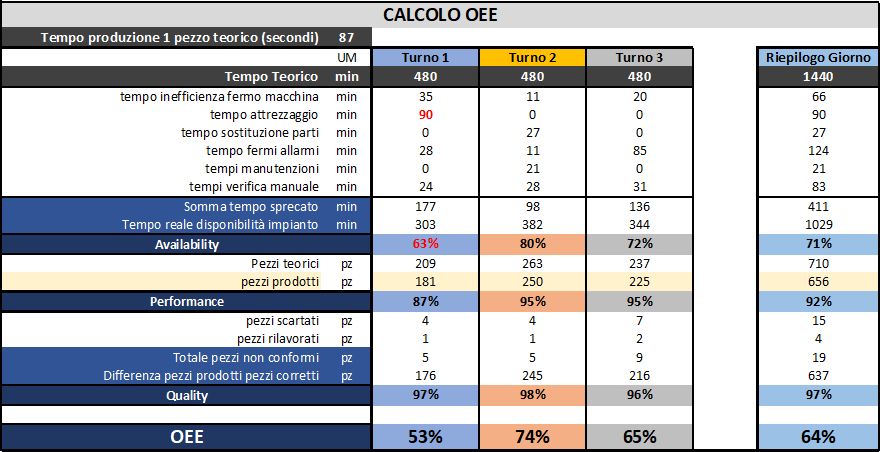
Efficientamento tramite OEE
L'OEE, essendo un'analisi rapida del potenziale di ottimizzazione, esamina e misura l'intera gamma di perdite di efficacia nei sistemi di produzione, evidenziando le conseguenze dello spreco.
L'OEE aiuta l'azienda a prendere le giuste decisioni per implementare i suggerimenti di miglioramento. L'indice OEE infatti evidenzia subito quali perdite dipendano dalla macchina o dal processo per essere ridotte al minimo.
Nell'esempio proposto prima infatti un valore che dovrebbe balzare subito all'occhio è che il livello di performance abbia dei valori particolarmente diversi tra teorico ed effettivo. Immaginare che una macchina produca solamente l'87% dei pezzi teorici deve insospettirci.
Le cause possono essere molteplici, i tempi teorici non sono corretti, l'impianto ha una velocità volontariamente ridotta per motivi industriali (nuovo utensile, nuovo materiale, nuova riprogrammazionepart-program, ecc.), l'impianto ha un degrado funzionale o usura nelle parti meccaniche o nella forza motrice che lo rallentano.
Queste ed altre considerazioni emergono facilmente quando si hanno a disposizione dati precisi e puntuali da poter valutare in maniera efficace.
Perdite in azienda
Allo stesso modo in cui i KPI mostrano gli indici di Performance per l'azienda, l'OEE può rientrare anche negli indici KRI (Key Risk Indicator) poiché misura il grado di inefficienza e di esposizione alla perdita finanziaria.
Possibili perdite in un'azienda possono essere perdite di prestazioni, ad esempio, a causa di guasti IT e guasti del sistema, diventa chiaro quanto l'azienda dipenda dalla tecnologia.
È tanto più importante prevenire i fallimenti in modo che le aziende non debbano affrontare ingenti perdite.
Interruzioni e guasti possono verificarsi anche nella produzione. Tali tempi di inattività possono derivare da errori e guasti dei sistemi, nonché da parti mancanti o problemi organizzativi.
Anche ulteriori modifiche tecniche e riparazioni possono causare un arresto.
L'indice OEE nella produzione può aiutare a monitorare le seguenti aree di miglioramento:
- Pianificazione
- Logistica
- Qualità del prodotto
- Manutenzione
- Ciclo produttivo
Un miglioramento tramite OEE può avvenire solo attraverso la raccolta puntuale dei dati produttivi e la rispettiva elaborazione.
Raccolta dati:
Al fine di operare il calcolo OEE serve raccogliere in campo e durante la produzione tutti i dati di lavorazione: tempi di sosta o interruzione dell'impianto, tempi medi di produzione per pezzo, numero di pezzi buoni rispetto ai pezzi scartati o rilavorati.
Questi valori quindi possono essere confrontati a consuntivo con i valori attesi teorici della pianificazione.
Queste informazioni sono chiaramente disponibili al manager di linea o al team leader.
Il supervisore, il team leader e il team di produzione possono così controllare e ottimizzare l'ulteriore produzione aziendale.
Perché adottare un controllo tramite OEE
OEE è il modo più rapido per confrontare tra loro le aree di produzione e implementare così un'eliminazione graduale dei tempi di fermo.
Le cause del deterioramento della produzione vengono riconosciute prontamente e vengono sviluppate opportunità di miglioramento per aumentare la produttività.
Al termine dell'acquisizione dei dati, le variazioni di produttività possono essere valutate in confronti giornalieri, settimanali, mensili e annuali.
L'obiettivo di OEE è raggiungere una produzione a zero difetti e impegnarsi nella manutenzione in un'azienda. Il conseguente aumento della produzione aiuta un'azienda a rimanere competitiva. Inoltre, è possibile verificare l'efficacia delle misure di miglioramento.
Ma quanto deve essere il valore giusto del mio OEE?
Normalmente in una azienda di produzione di massa, in cui i lotti di prodotti abbiano un tempo di attraversamento superiore alle 8 ore di un turno (poiché l'attrezzaggio è un elemento che abbatte questo indice), un buon valore di indice di performance medio settimanale potrebbe attestarsi attorno all'85%.
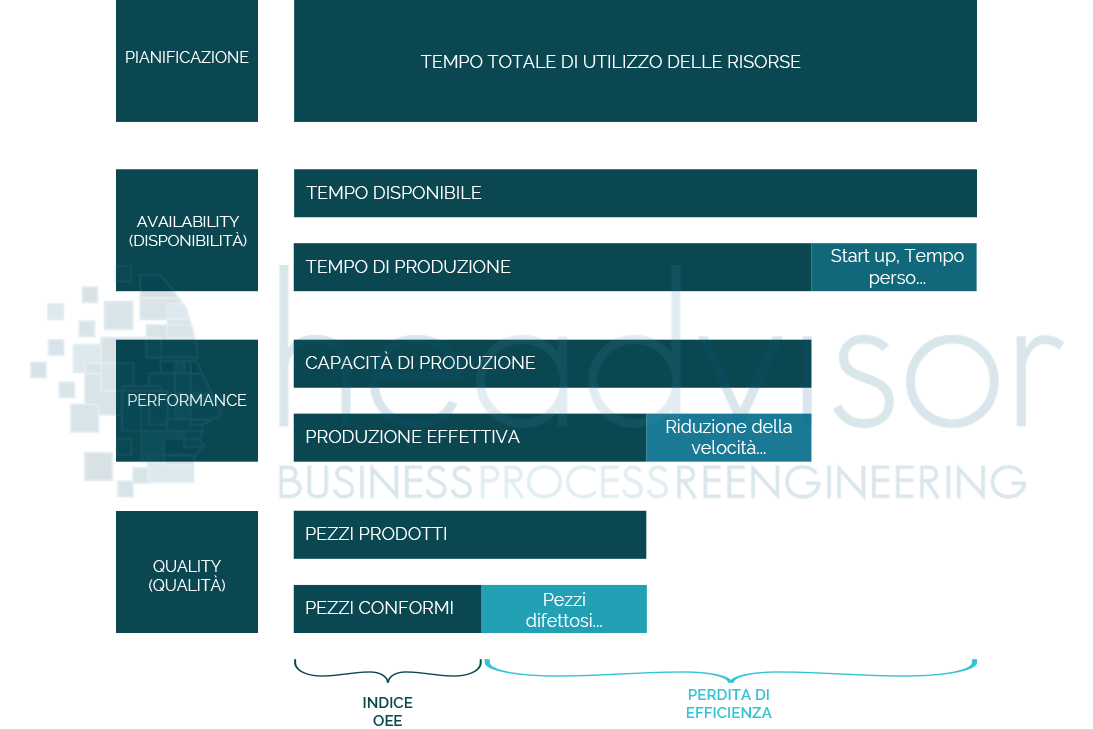
Un valore 85% è normalmente utilizzato dai fornitori di componenti automotive per giudicare la robustezza dell'impianto dei fornitori. Quando si eseguono audit nella Supply Chain management, i Clienti strategici come case automobilistiche o grosse multinazionali, eseguono controlli sull'efficienza produttiva dei loro fornitori.
È facile intuire come raggiungere un valore di rapportato superiore a 85%, raccontato nell'esempio precedente sia comunque ancora un lavoro molto oneroso in termini di efficientamento aziendale.
Le azioni e i correttivi necessari per migliorare l'efficienza degli impianti deve essere eseguito con cura e precisione, analizzando il flusso del valore (Value Stream Map - VSM) e correggendo tutti gli sprechi (MUDA) che castigano l'efficienza.
Tuttavia è evidente che nelle lavorazioni di piccoli lotti in cui vi sia un forte dispendio di tempo causato dai frequenti attrezzaggi, un valore di 85% sia difficilissimo se non impossibile da raggiungere.
Questo cosa significa? Non esiste un valore univoco per tutti i processi produttivi, esiste però la possibilità di misurare e quindi migliorare la propria efficienza produttiva.
Scoprire oggi che un impianto di un contoterzista ha un'efficienza del 60% non deve assolutamente stupire. Invece è interessante nei mesi riuscire ad adoperarsi al fine che lo stesso impianto passi via via al 65% e poi al 70%. Questo è l'atteggiamento giusto.
Immaginiamo che 10 impianti passino da un valore OEE da 70% a 80% di produttività in 6/12 mesi grazie all'adozione di tutti i buoni principi della Lean Production , in pratica è come aver introdotto un nuovo impianto, funzionante, ma senza averne dovuto sostenere i costi.
Come può avvenire tutto questo? Magari ci sono nuovi strumenti, maggiori sistemi di controllo, nuovo software interconnesso all'elettronica di macchinario, ma i costi di efficientamento e sviluppo saranno comunque inferiori rispetto ai benefici derivanti all'aumento della produttività e dei nuovi livelli di controllo (KPI) aziendali.
Metodo scientifico per l'OEE
Serve rigore e precisione per un buon calcolo OEE, pochi minuti di arrotondamento o qualche tolleranza in più sul pezzo lavorato possono incidere parecchio sulla bontà di questo dato.
Se i segnali arrivano dai PLC della macchina, le variabili sono decisamente più precise. La rilevazione dei tempi uomo e la qualità del prodotto devono essere immediatamente rilevati.
Molto spesso alcuni atteggiamenti involontari possono inquinare la precisione della raccolta dati, ricordo alcuni casi di inefficienza in cui il controllo qualità veniva fatto in modo "sommario" (o "furbo" se pensiamo in malafede) spalmando i rilavorati sul tempo medio dei pezzi buoni.
In questo modo mantenendo qualche secondo di "tolleranza" sul tempo medio produttivo per pezzo, risultava un buon livello di OEE ma che in realtà tanto buono non era.
Questi atteggiamenti servono a poco, se un processo produttivo può essere migliorato non è gestendo i dati a piacimento che si risolvono le inefficienze, servono solo per far contenta la proprietà e mantenere lo status quo.
La filosofia Kaizen incentiva il miglioramento continuo anche da parte degli stessi operatori, dalla direzione e dai manager deve arrivare cultura al miglioramento incentivando la mentalità collettiva all'efficienza.
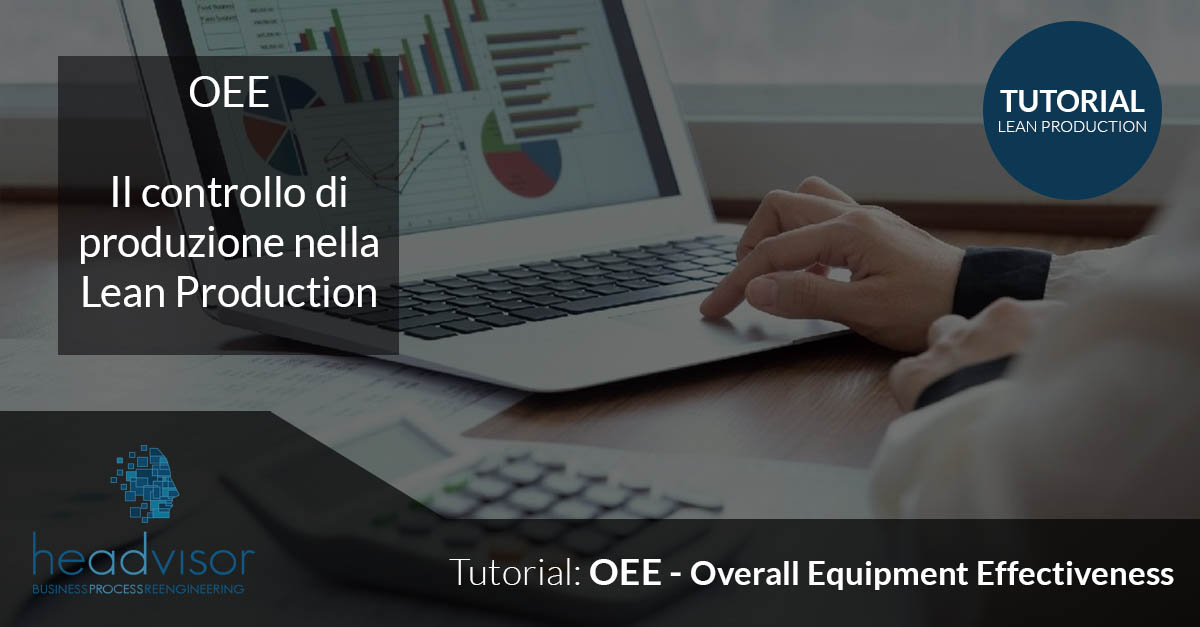
Chiedici una consulenza gratuita
I nostri esperti sono a tua disposizione!
Gli operatori circolano nei reparti della tua azienda con fogli di carta? La pianificazione della produzione è manuale o effettuata con Excel?
Sai esattamente quanto è il tuo livello di produzione? Quanto scarto produci? Quante rilavorazioni per inefficienze? Quante materie prime impieghi?
Tramite un processo di efficientamento è possibile implementare soluzioni tengibili, per ottimizzare al meglio ogni processo e migliorare il livello di efficienza.
Tutto il nostro team è a tua disposizione, per qualunque esigenza.
Leggi i Tutorials più recenti
Strumenti per efficientare le imprese
Core Tools Automotive: l’importanza degli strumenti “Core”
Core tools automotive: gli strumenti chiave da conoscere per lavorare come controller, project manager e dirigenti nel settore automotive.... [Continua a Leggere]
Metodo Hoshin Kanri per la pianificazione strategica
Hoshin Kanri è un metodo di gestione strategica della lean production che permette di allineare gli obiettivi strategici di un'azienda con le sue operazioni quotidiane... [Continua a Leggere]
ESRS: gli standard europei per il reporting sulla sostenibilità
ESRS: gli standard che definiscono le linee guida per la rendicontazione sostenibile delle aziende in Europa. Scopri cosa sono in questo articolo... [Continua a Leggere]
CSDDD o CS3D: cosa è e cosa prevede la nuova direttiva europea
CSDDD o CS3D perché è nata questa normativa europea? a chi è rivolta? entro quando entrerà in vigore?... [Continua a Leggere]
Sostenibilità aziendale: come migliorare le performance sostenibili
La sostenibilità aziendale è un concetto fondamentale per le aziende moderne. Come implementare soluzioni sostenibili per il prossimo futuro?... [Continua a Leggere]
Balanced scorecard: la guida completa
Balanced Scorecard BSC è la scheda di valutazione bilanciata per la gestione strategica e la misurazione dei risultati aziendali nelle diverse aree.... [Continua a Leggere]
Analisi PEST e analisi PESTEL
Analisi PESTEL (anche conosciuta come PEST o PESTLE) permette di evidenziare tutti i fattori esterni che possano condizionare lo sviluppo di una azienda o business... [Continua a Leggere]
La Carbon Footprint aziendale: 9 tecniche e metodi per la stima degli impatti di emissioni in atmosfera
Carbon Footprint aziendale: tecniche e metodi per la stima degli impatti di emissioni in atmosfera e rendicontazione nel bilancio di sostenibilità... [Continua a Leggere]
Margine di Contribuzione: Cos’è, Calcolo ed Esempi
Il margine di contribuzione è un indice fondamentale per valutare la redditività dei prodotti creati dall'azienda. Leggi questo articolo per saperne di più... [Continua a Leggere]
Just in Time: efficienza in produzione e logistica
Il just in time è una strategia di gestione che permette di ridurre gli sprechi e rendere più efficiente e coordinato il reparto produzione.... [Continua a Leggere]
WBS (Work Breakdown Structure): cos'è e come utilizzarla
La WBS è lo strumento di ripartizione del lavoro per suddividerlo in compiti più piccoli e renderlo più gestibile, controllabile e accessibile.... [Continua a Leggere]
Break Even Point (BEP) - come calcolare il punto di pareggio
Il Break Even Point è una formula per calcolare il punto di pareggio. Il valore in cui i profitti e i costi di un’attività aziendale sono in equilibrio.... [Continua a Leggere]
Sistemi di Efficientamento organizzativo
Gli strumenti per efficientare la tua impresa
L'analisi e la mappatura dei processi di un'organizzazione, consentono di riorganizzare le attività, razionalizzare l'uso delle risorse, incrementare l’efficacia, l’efficienza ela produttività della struttura stessa.
I nostri servizi a supporto di imprese:
- Mappatura dei processi interni, gestionali e organizzativi
- Analisi e ottimizzazione delle prestazioni dei processi individuati
- Analisi e riduzione dei costi di gestione
- Ridefinizione dei processi con l'obiettivo di migliorare l'efficienza dell'organizzazione e delle sue prestazioni
- Progettazione di Innovazione tecnologica e digitalizzazione dei processi
- Progettazione di economia circolare