Poka Yoke cosa è e come eseguirlo
Uno dei più importanti successi ottenuti dalla Lean Management è Poka Yoke.
L'espressione giapponese Poka Yoke descrive un principio costituito da diversi elementi, che include precauzioni tecniche e dispositivi per la prevenzione degli errori e per il rilevamento immediato degli errori.
È particolarmente orientato verso gli errori involontari che le persone possono commettere quando sono coinvolti nei processi di produzione ed è inteso a impedire che un errore si trasformi in un errore di prodotto.
Poka Yoke è stato sviluppato dal giapponese Shigeo Shingo nel Toyota Production System (TPS).
Shingo ha anche sviluppato e descritto Zero Quality Control, una combinazione di tecniche Poka Yoke per correggere possibili difetti e un'ispezione alla fonte per prevenirli.
Poka Yoke significato
"Poka" significa "errore involontario" in giapponese, "Yoke" significa "evitare" o "ridurre", in modo che l'espressione Poka Yoke possa essere tradotta come evitare errori involontari.
In questo senso, è altrettanto possibile utilizzare la designazione "sicuro" per agire in relazione a un processo di fabbricazione.
Poka Yoke è uno strumento eccezionale per raggiungere lo stato produttivo di "zero difetti".
L'idea di evitare errori e difetti fin dall'inizio del processo produttivo può essere utilizzata universalmente e si è rivelata un reale aumento dell'efficienza.
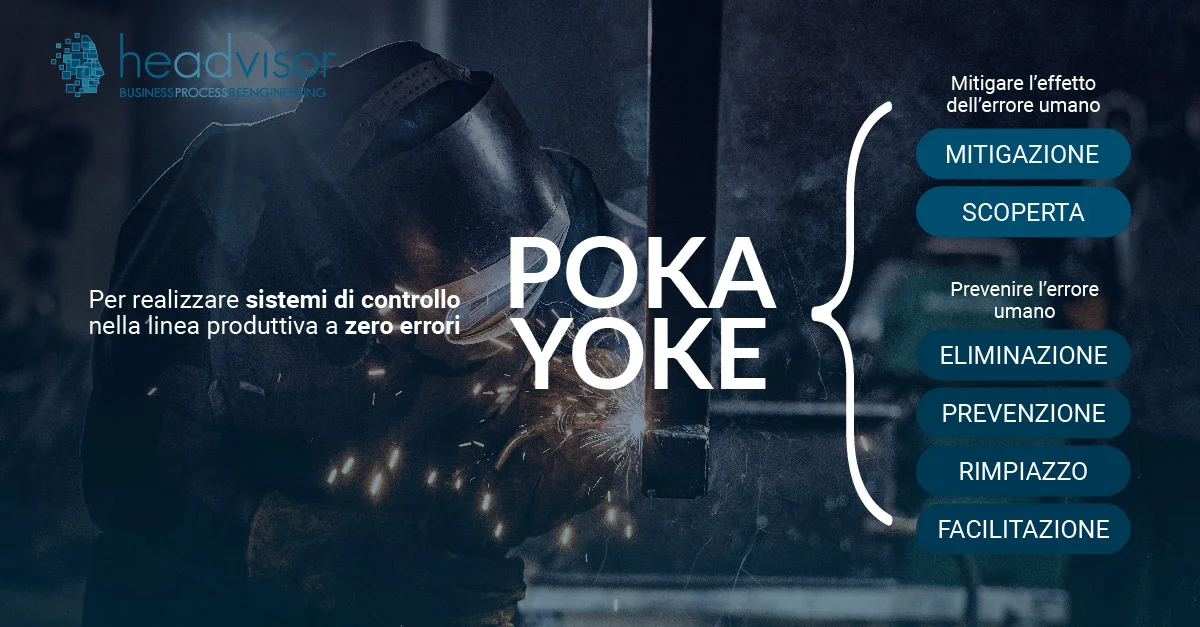
Il termine originale era in realtà baka-yoke, che significa qualcosa come "infallibile" ma fu ritenuto eccessivamente pretenzioso, e venne quindi successivamente cambiato in Poka Yoke.
Poka Yoke significa protezione dagli errori o letteralmente - evitare errori accidentali (poka yokeru).
Poka Yoke garantisce che esistano le giuste condizioni prima che venga eseguita una fase del processo, evitando così che si verifichino errori sin dall'inizio del processo produttivo.
Dove ciò non è possibile, Poka Yoke agisce come controllore per eliminare gli errori nel processo il più rapidamente ed economicamente possibile.
Poka Yoke in sintesi potrebbe essere definito come un qualsiasi meccanismo in un processo di produzione Lean Production che aiuti ad evitare errori.
Il suo scopo è eliminare i difetti del prodotto prevenendo, correggendo o segnalando gli errori umani non appena si verifichino.
Metodologia Poka Yoke
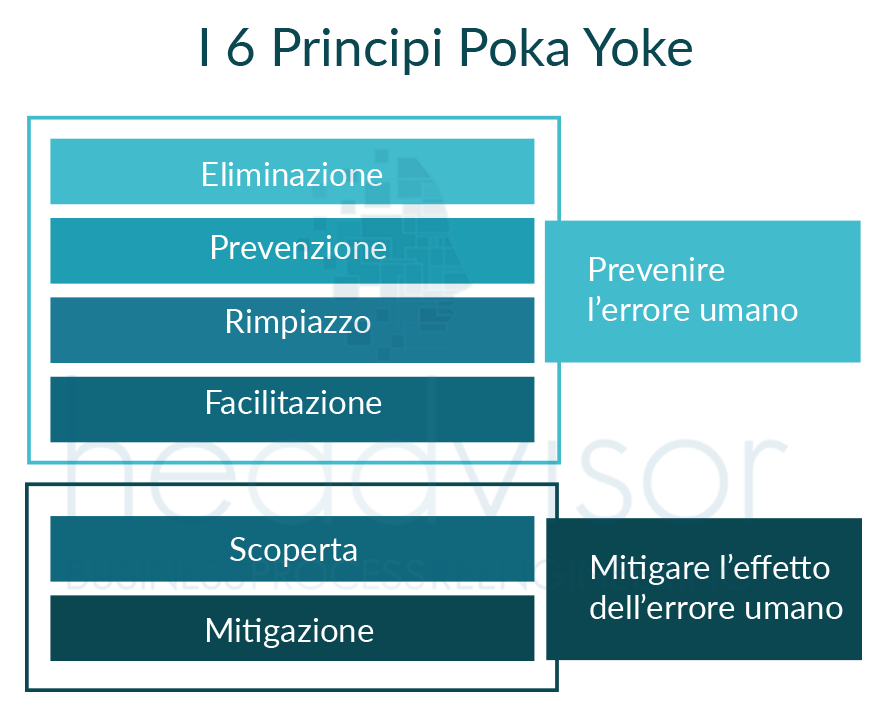
Il punto di partenza per Poka Yoke è la consapevolezza che nessuna persona o sistema sia in grado di evitare completamente errori involontari.
Nel caso di sistemi industriali, ovvero macchine e impianti, le informazioni sugli errori possono essere normalmente fornite utilizzando il parametro Mean Time Between Failure (MTBF) o l'intervallo medio di guasto.
Azioni sbagliate come disattenzione, omettere, confondere, dimenticare, leggere in modo errato, interpretare male, possono a loro volta essere aggravate da stress, elementi ambientali dannosi, cattive condizioni di lavoro. Tutti questi aspetti sono nella natura umana e, nonostante tutti gli sforzi, non possono essere escluse con certezza.
Con l'aiuto di Poka Yoke, vengono utilizzati per lo più sistemi semplici ma efficaci per garantire che tali errori nel processo di produzione non portino a errori nel prodotto finale o passino inosservati.Viene utilizzato in combinazione anche con un rispettivo metodo di ispezione per poter escludere a priori il verificarsi di difetti ormai già avvenuti in passato e corretti.
La Source Inspection, anch'essa sviluppata da Shigeo Shingo, si è dimostrata particolarmente efficace.
Poiché viene considerata l'intera catena causale tra la manipolazione errata nel processo e l'errore nel prodotto, le cause di errore saranno quindi messe in risalto ed eliminate.
In questo modo, l'eventuale ripetersi di un errore sarà efficacemente prevenuto andando a convergere nel concetto di azzeramento dell'errore.
Nell'uso pratico, un sistema Poka Yoke consiste fondamentalmente nei due elementi di base: un meccanismo di rilevamento e un meccanismo di regolazione.
Inoltre, ci sono precauzioni speciali sotto forma di misure progettuali che escludono fin dall'inizio possibili irregolarità.
Meccanismi di rilevamento
I meccanismi di rilevamento sono sensori e sistemi di rilevazione che possono essere utilizzati in una varietà di forme: come sensori di posizione, interruttori di fine corsa o di prossimità, dimensioni, forma, pressione, temperatura, vibrazione, colore o corrente e tutti quei sistemi di sensoristica atti a rilevare uno stato o una azione.
Meccanismi di regolazione
A seconda del tipo di misura che viene rilevata dalla sensoristica, i meccanismi di regolazione possono intervenire nei seguenti metodi:
Metodo di intervento
Se si verificano deviazioni o irregolarità di processo che possono causare errori, la macchina viene immediatamente fermata (CUT-OFF). Anche le operazioni antecedenti associate al processo vengono immediatamente interrotte.
Ciò consente di attuare misure correttive per evitare errori in cascata o l'accumulo di costi di produzione su un semilavorato non conforme che potrebbe proseguire nelle fasi di lavorazione seguenti.
Ridurre gli errori
Grazie all'introduzione di sistemi di allarme vengono sviluppati tutti i tipi di segnalazioni per avvisare il corretto o NON corretto funzionamento del processo. Questi possono essere ottici e/o acustici che allertano di una situazione errata che si è appena verificata.
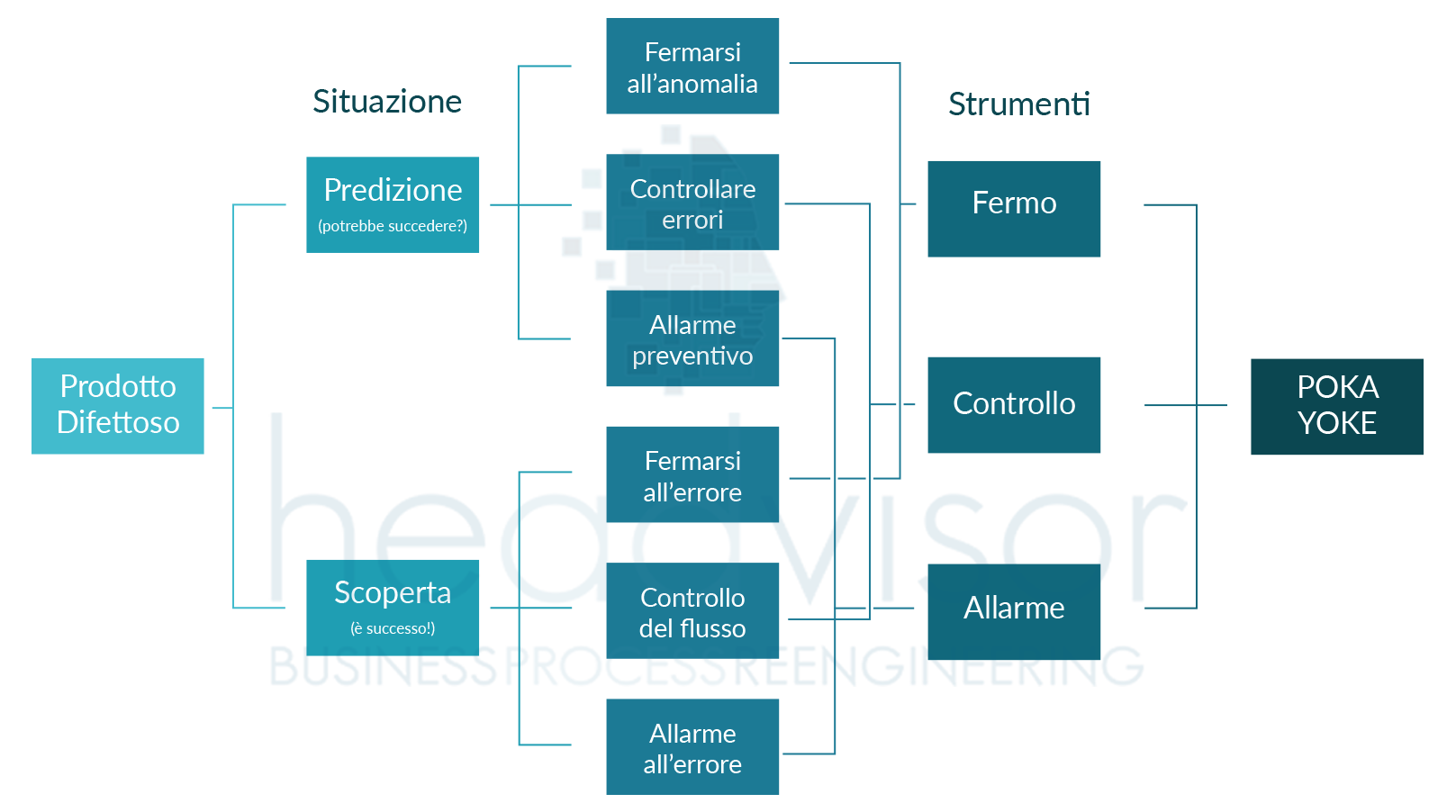
Attraverso l'uso mirato di Poka Yoke in relazione all'ispezione delle fonti di errore, è possibile utilizzare ausili tecnici (spesso anche relativamente semplici) per prevenire errori nel prodotto durante il processo produttivo.
Va notato, tuttavia, che le cause degli errori spesso si trovano in una fase precedente del processo di sviluppo del prodotto. Serve domandarsi allora se non sia più efficace prevenire tale errore nel processo a monte e magari con uno sforzo inferiore.
Un buon metodo teorico per ridurre gli errori già in fase di progettazione è il sistema di valutazione a matrice denominato FMEA (Failure Mode and Effects Analysis).
Va sottolineato tuttavia che il confronto con Poka Yoke richiede un cambio di mentalità che accetti errori e tassi di errore e li assuma come inevitabili. Sullo sfondo dell'inevitabilità dell'errore umano, tuttavia, il verificarsi di errori non deve assolutamente essere considerato normale.
Come implementare Poka Yoke
Poka Yoke è semplice e razionale e quindi facile da implementare. È possibile eseguire il seguente processo passo dopo passo per applicare la tecnica:
- Identifica l'operazione o il processo.
- Analizzare i 5 perché (5 Whys) e le possibilità di fallimento del processo.
- Prova il metodo e vedi se funziona.
- Formare l'utente, esaminare le prestazioni e misurare il successo.
- Organizza e gestisci i progetti in modo efficiente
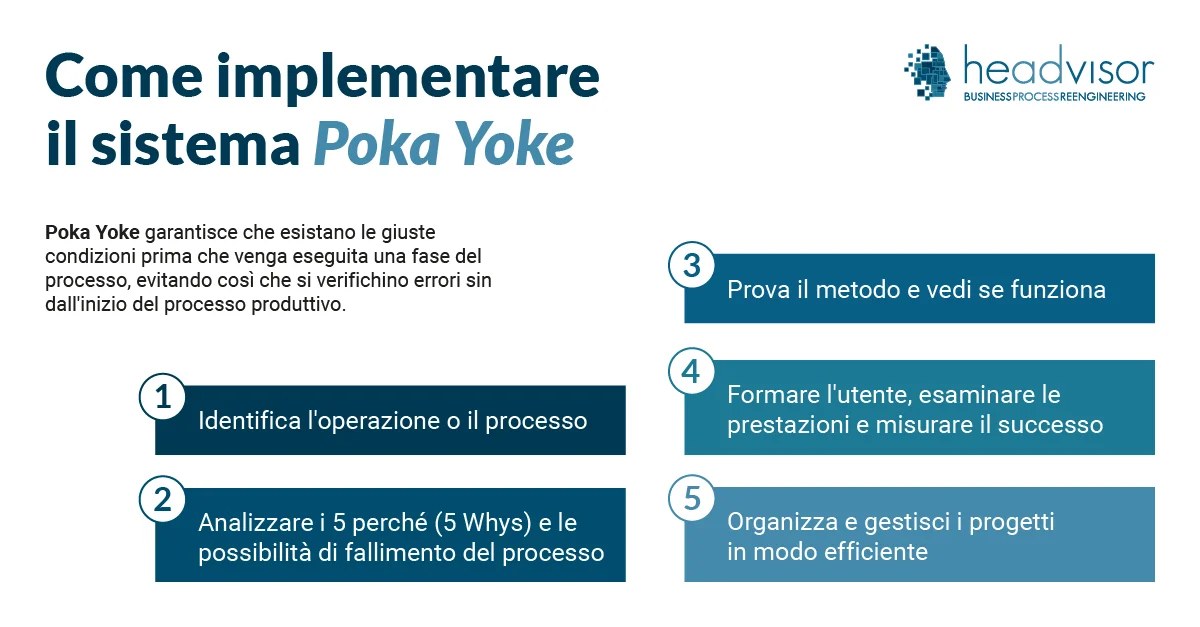
Esempi di utilizzo tecnica Poka Yoke
Un esempio di Poka Yoke si possono trovare nelle prese elettriche a prova di bambino o nella lavatrice che si avvia solo quando l'oblò è chiuso oppure si lascia aprire solamente quando il cestello è completamente fermo per evitare pericoli o allagamenti.
Questi tipi di automazione funzionano bene poiché non ammettono errori involontari
Può essere applicato con successo in tutti i tipi di processi in produzione o nel settore dei servizi e previene tutti i tipi di errori:
- Evitare parti mancante durante l'assemblaggio.
- Prevedere errori di configurazione o impostazione utensile errata o impostazione della macchina.
- Evitare l'uso di parti errate.
- Impedire di saltare una fase o non completarla secondo le istruzioni
- Impedire errori di misurazione o di controllo qualità
Perché Poka Yoke è importante?
Il vantaggio di Poka Yoke è che la tecnologia garantisca che persone e processi funzionino correttamente eliminando gli errori.
Queste tecniche possono migliorare in modo significativo la qualità e l'affidabilità dei prodotti e dei processi eliminando i difetti.
Questo approccio alla produzione si inserisce perfettamente nella cultura del Kaizen - Miglioramento continuo o filosofia Kaizen ben argomentata nella filosofia della Lean Management.
La flessibilità di Poka Yoke inoltre gli consente di essere distribuito a basso costo.
La tecnica Poka Yoke può sempre essere utilizzata quando potrebbe verificarsi un errore o qualcosa potrebbe essere fatto male, quindi potenzialmente sempre e ovunque.
Poka Yoke in sintesi
La tecnologia Poka Yoke è uno dei più grandi tesori nella gestione Lean Production. Ciò consente di garantire la qualità senza utilizzare un processo di garanzia della qualità. Semplicemente prevengono i difetti fin dall'inizio.
Poka Yoke può essere implementato in qualsiasi settore produttivo e di processo offrendo molti vantaggi a basso costo.
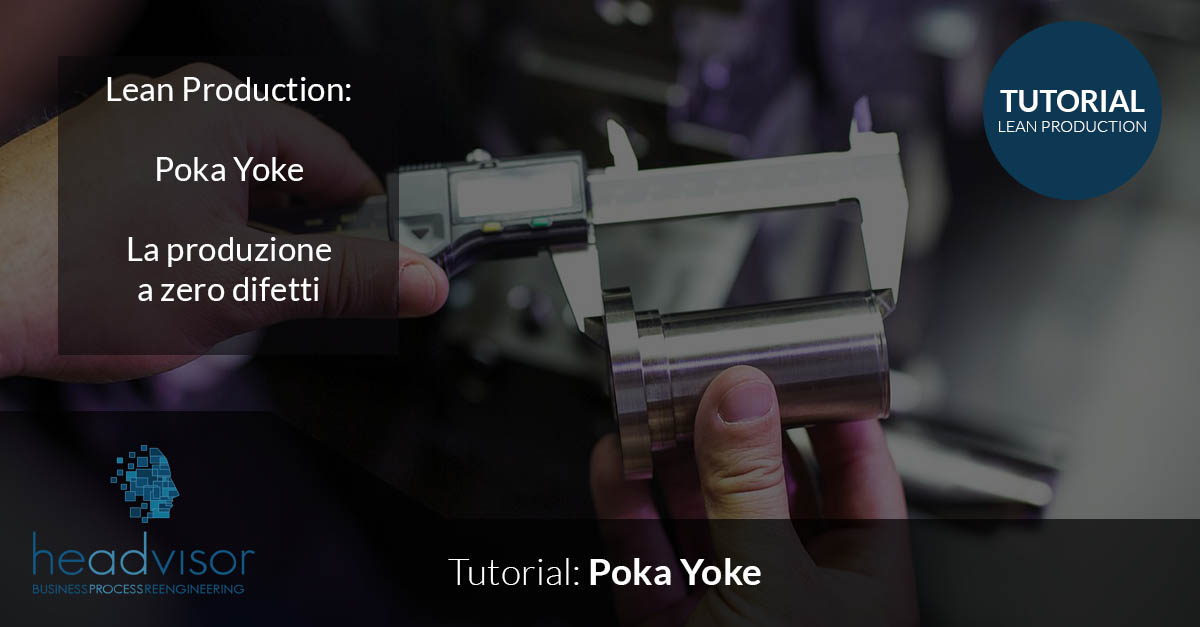
Argomenti correlati:
- Analisi FMEA per la valutazione degli effetti negativi generati da problemi produttivi.
- Diagramma Ishikawa e i 5 Perchè (5whys) per la risoluzione di problemi procedurali
- Spreco di Skills e Formazione l'importanta del personale ben formato
- KRI (Key Risk Indicator) e la misurazione di indici di rischio
- Risk Management per la gestione dei fattori di rischio aziendali
Chiedici una consulenza gratuita
I nostri esperti sono a tua disposizione!
Gli operatori circolano nei reparti della tua azienda con fogli di carta? La pianificazione della produzione è manuale o effettuata con Excel?
Sai esattamente quanto è il tuo livello di produzione? Quanto scarto produci? Quante rilavorazioni per inefficienze? Quante materie prime impieghi?
Tramite un processo di efficientamento è possibile implementare soluzioni tengibili, per ottimizzare al meglio ogni processo e migliorare il livello di efficienza.
Tutto il nostro team è a tua disposizione, per qualunque esigenza.
Leggi i Tutorials più recenti
Strumenti per efficientare le imprese
Core Tools Automotive: l’importanza degli strumenti “Core”
Core tools automotive: gli strumenti chiave da conoscere per lavorare come controller, project manager e dirigenti nel settore automotive.... [Continua a Leggere]
Metodo Hoshin Kanri per la pianificazione strategica
Hoshin Kanri è un metodo di gestione strategica della lean production che permette di allineare gli obiettivi strategici di un'azienda con le sue operazioni quotidiane... [Continua a Leggere]
ESRS: gli standard europei per il reporting sulla sostenibilità
ESRS: gli standard che definiscono le linee guida per la rendicontazione sostenibile delle aziende in Europa. Scopri cosa sono in questo articolo... [Continua a Leggere]
CSDDD o CS3D: cosa è e cosa prevede la nuova direttiva europea
CSDDD o CS3D perché è nata questa normativa europea? a chi è rivolta? entro quando entrerà in vigore?... [Continua a Leggere]
Sostenibilità aziendale: come migliorare le performance sostenibili
La sostenibilità aziendale è un concetto fondamentale per le aziende moderne. Come implementare soluzioni sostenibili per il prossimo futuro?... [Continua a Leggere]
Balanced scorecard: la guida completa
Balanced Scorecard BSC è la scheda di valutazione bilanciata per la gestione strategica e la misurazione dei risultati aziendali nelle diverse aree.... [Continua a Leggere]
Analisi PEST e analisi PESTEL
Analisi PESTEL (anche conosciuta come PEST o PESTLE) permette di evidenziare tutti i fattori esterni che possano condizionare lo sviluppo di una azienda o business... [Continua a Leggere]
La Carbon Footprint aziendale: 9 tecniche e metodi per la stima degli impatti di emissioni in atmosfera
Carbon Footprint aziendale: tecniche e metodi per la stima degli impatti di emissioni in atmosfera e rendicontazione nel bilancio di sostenibilità... [Continua a Leggere]
Margine di Contribuzione: Cos’è, Calcolo ed Esempi
Il margine di contribuzione è un indice fondamentale per valutare la redditività dei prodotti creati dall'azienda. Leggi questo articolo per saperne di più... [Continua a Leggere]
Just in Time: efficienza in produzione e logistica
Il just in time è una strategia di gestione che permette di ridurre gli sprechi e rendere più efficiente e coordinato il reparto produzione.... [Continua a Leggere]
WBS (Work Breakdown Structure): cos'è e come utilizzarla
La WBS è lo strumento di ripartizione del lavoro per suddividerlo in compiti più piccoli e renderlo più gestibile, controllabile e accessibile.... [Continua a Leggere]
Break Even Point (BEP) - come calcolare il punto di pareggio
Il Break Even Point è una formula per calcolare il punto di pareggio. Il valore in cui i profitti e i costi di un’attività aziendale sono in equilibrio.... [Continua a Leggere]
Sistemi di Efficientamento organizzativo
Gli strumenti per efficientare la tua impresa
L'analisi e la mappatura dei processi di un'organizzazione, consentono di riorganizzare le attività, razionalizzare l'uso delle risorse, incrementare l’efficacia, l’efficienza ela produttività della struttura stessa.
I nostri servizi a supporto di imprese:
- Mappatura dei processi interni, gestionali e organizzativi
- Analisi e ottimizzazione delle prestazioni dei processi individuati
- Analisi e riduzione dei costi di gestione
- Ridefinizione dei processi con l'obiettivo di migliorare l'efficienza dell'organizzazione e delle sue prestazioni
- Progettazione di Innovazione tecnologica e digitalizzazione dei processi
- Progettazione di economia circolare