Tempo di lettura: 9 min
Indice
TPS Toyota Production System - Taiichi Ohno
Il Toyota Production System (T.P.S.) è un sistema di organizzazione della produzione che venne a formarsi nell’azienda giapponese fondata dalla famiglia Toyoda, la Toyota Motor Company. Il nome della società era stato trasformato da Toyoda in Toyota per motivi scaramantici, potendosi quest'ultimo scrivere, in giapponese, con otto colpi di pennello (l'8 è considerato un numero fortunato in Giappone)
Le origini della famosa multinazionale giapponese, oggi Toyota Motor Corporation, iniziarono nel 1933, quando la Toyota Utomatic Loom, società produttrice di telai tessili fondata da Sakichi Toyoda (detto il "re degli inventori giapponesi") nel 1890, aprì una divisione destinata alla produzione delle automobili diretta poi dal figlio Kiichiro Toyoda .
La divisione venne tramutata in una società indipendente nel 1937, la Toyota Motor Company. Ciò fu anche il risultato della pressione del governo giapponese, che spinse affinché la società si specializzasse nella produzione di autocarri per l’Esercito imperiale giapponese durante la Seconda Guerra Mondiale.
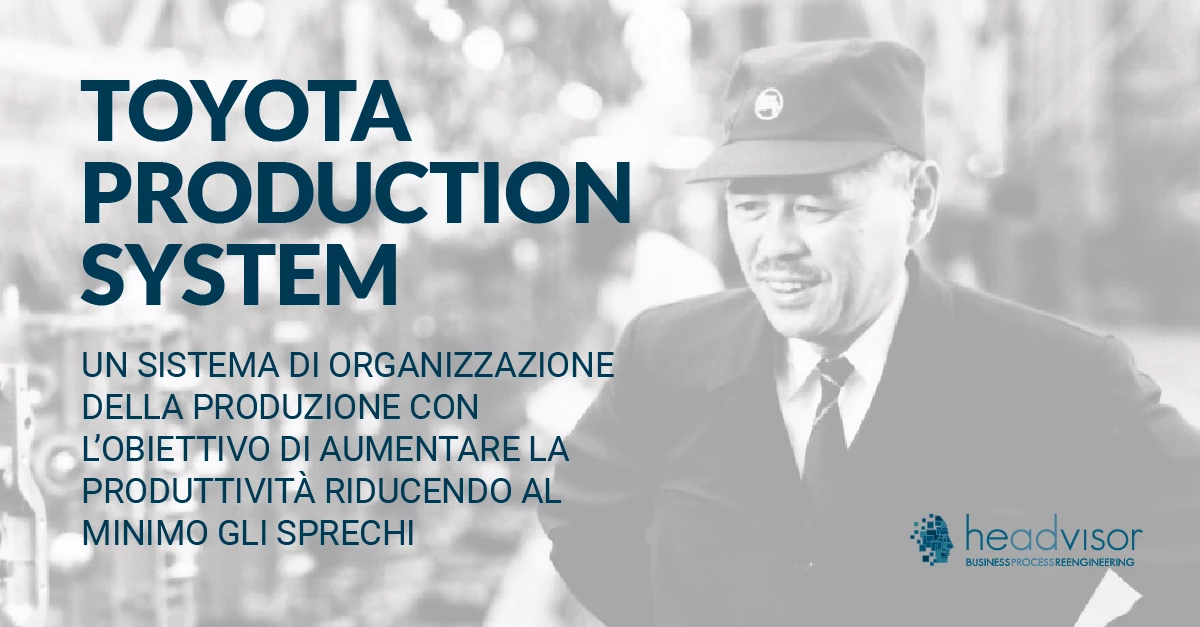
Toyota nel dopoguerra
Il contesto socio economico post-guerra rese inapplicabile il modello produttivo fordista occidentale in Toyota. La mancanza di capitali che caratterizzava l’economia giapponese e gli elevati costi di produzione, in particolare delle materie prime, non consentivano infatti di creare, come accadeva in occidente, economie di scala che portassero ad un abbattimento dei costi unitari.
Taiichi Ohno
Solo grazie all’intuzione di Taiichi Ohno, allora diretore generale, che Toyota fece il salto di qualità. Tahiichi Ohno, nato nel 1912, dedicò quasi tutta parte della sua vita lavorativa al servizio della famiglia Toyoda, inizialmente come impiegato nella società produttrice di telai.
Spostato nel 1939 al ramo automobilistico in cui fece carriera fino a diventare membro del consiglio esecutivo della Compagnia, Taiichi Ohno si rese conto presto che era necessario cambiare il metodo produttivo slegandosi dal principio fordista basato sulla produzione di massa.
Taiichi Ohno fece diversi viaggi in Usa, con l’obiettivo di studiare il modello fordista e rimase negativamente stupito in particolare da come la Ford Motor Company aveva organizzato la catena di montaggio, a suo avviso pieno di "MUDA" (sprechi).
Rimase invece particolarmente colpito dal modello di una catena di negozi, i Piggly Wiggy, caratterizzati da un particolare modo di allestire un percorso obbligato lungo il quale dei prodotti posti sulle mensole potevano essere prelevati e poi pagati all’uscita.
Tahiichi Ohno pensò di trasporre tale principio in Toyota, regolando quindi il tasso di produzione in base all’andamento della domanda, un principio contrapposto al fordismo, caratterizzato da una produzione di massa concentrata sullo stimolo dell’offerta. Come nacque quindi il Toyotismo (TPS Toyota Production System)?
Per ironia della sorte, studiando... un supermercato americano. Gli stessi produttori statunitensi subiranno le conseguenze dell’intuizione di Taiichi Ohno.
I Principi del Toyota Production System TPS
Il principio base di Taiichi Ohno è che la sovrapproduzione è la madre di tutti i MUDA (gli sprechi).
L’obiettivo è quello quindi di aumentare la produttività riducendo al minimo i MUDA (gli sprechi).
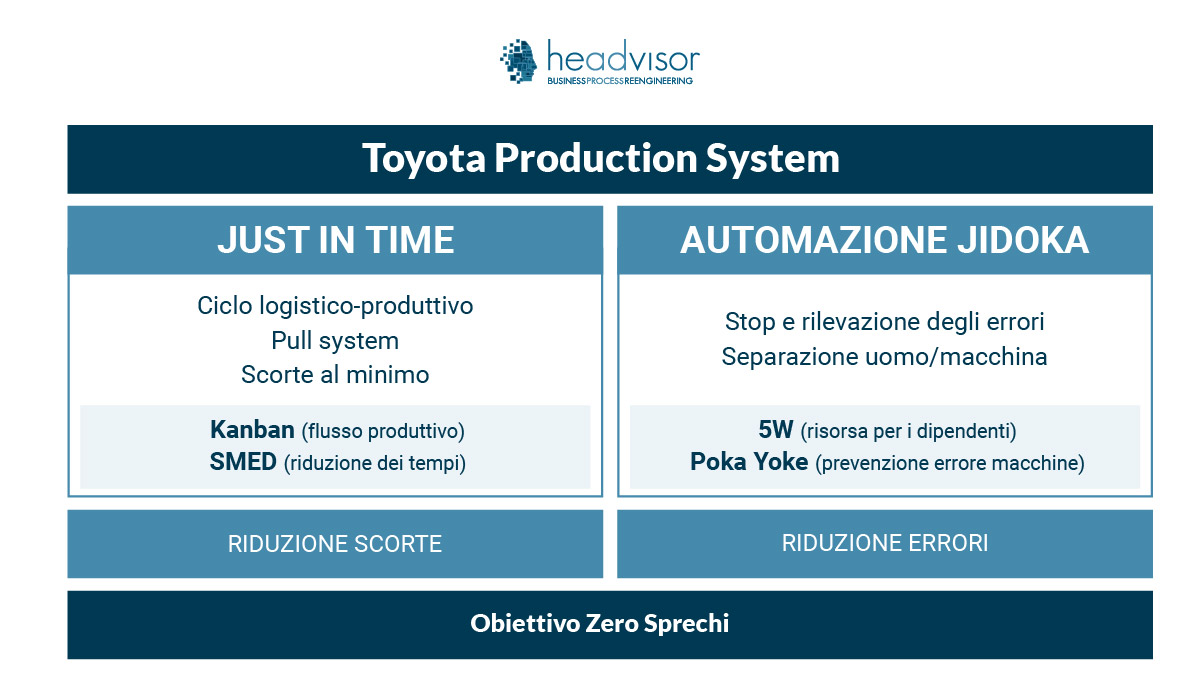
I due pilastri del Toyota Production System TPS sono il Just in time e l’autonomazione.
Just in time
Il Just in time, inteso come logica di coordinamento tra due fasi del ciclo logistico-produttivo, in particolare tra cliente e fornitore, consiste nel far arrivare all’attività lavorativa solo i componenti richiesti, nel tempo richiesto e nella quantità richiesta. In questo modo si riducono al minimo le scorte inventariali, si sincronizzano le attività tra fornitore cliente e si riduce il rischio di produrre componenti che non verranno rapidamente utilizzati.
Questa logica, di tipo “Pull”, si contrappone al sistema di tipo “Push”, caratterizzato dalla realizzazione di prodotti finiti allo scopo di stoccarli in magazzino. Secondo Taiichi Ohno infatti “Più materiale c'è a magazzino, meno probabilità c'è che si trovi ciò di cui si ha bisogno.”
Kanban per Zero scorte
L’obiettivo “zero scorte” può essere raggiunto attraverso il combinato disposto dell’utilizzo di Kanban e della metodologia SMED.
I Kanban sono cartellini di segnalazione (cartacei o ellettronici) indicanti un articolo e poche altre informazioni, che esprimono una richiesta tra una postazione di lavoro e la sua precedente. Il cartellino kanban, spostandosi lungo il processo, determina il flusso produttivo “ordinando” le lavorazioni tramite una logica Pull, chiamando cioè da valle le lavorazioni necessarie in base ai bisogni del momento.
La metodologia SMED (Single Minute Excchange of Die), si propone di ridurre i tempi di set-up portando ad una riduzione dei tempi riattrezzaggio dei macchinari. Tale metodologia consente di avere una maggiore reattività alle richieste dei clienti, i set-up sono infatti attività a non valore aggiunto (NVA) i cui costi determinano un ricarico sul costo finale per il cliente oppure una riduzione del profitto.
Il combinato disposto di Kanban e SMED consente di ridurre i “tempi morti” e il risultato è un sistema operativo flessibile capace di adattarsi alle esigenze del mercato.
Automazione Jidoka - Autonomazione
Il secondo pilastro del TPS è l’autonomazione (Jidoka in giapponese), crasi di “autonomia” e “automazione”. L’obiettivo è quello di dotare la macchina di sistemi di prevenzione dei difetti e a prova di errore (Poka Yoke).
Tale sistema si fonda su due espedienti: uno che si basa sulla rilevazione degli errori, l’altro che consenta di fermare la produzione quando questi si verificano, in modo tale da risolvere il problema con urgenza, limitando la ripetizione delle anomalie. L’obiettivo è quindi quello di slegare l’addetto dalla macchina.
I macchinari non necessitano più di una continua supervisione, in questo modo i dipendenti possono generare un surplus di valore limitando gli sprechi. Secondo Taiichi Ohno infatti “Tutte le ispezioni condotte allo scopo di individuare difetti sono uno spreco e una perdita di tempo. Le ispezioni vanno fatte per prevenire i difetti”.
5 perchè
Un metodo utile per far fruttare l’intelligenza dei dipendenti è quello dei “cinque perchè” (5whys).
La tecnica dei “cinque perchè” (5whys) consente di trovare le effettive cause di un problema senza fermarsi alla prima domanda sottostante ad un problema. Ponendosi almeno 5 domande, un problema può essere risolto alla radice senza accontentarsi di una soluzione superficiale.
A questo proposito vale la pena ricordare due riflessioni di Taiichi Ohno per il quale ”Lo stile Toyota Production System (TPS) non consiste nel creare risultati col duro lavoro. Il nostro è un sistema che afferma che non ci sono limiti alla creatività delle persone. Le persone non vanno in Toyota per lavorare, vanno in Toyota per pensare” e “Le risorse umane sono qualcosa al di sopra di ogni misurazione. Le capacità di queste risorse possono estendersi illimitatamente quando ogni persona comincia a pensare.”
I due pilastri hanno quindi “obiettivi tendenti allo zero”, la produzione di scorte tendenti allo zero per il Just in time e una riduzione tendente allo zero di difetti per l’autonomazione (Jidoka).
Grazie all’introduzione di questi principi produttivi, nell’arco di circa 25 anni, dagli anni ’60 alla metà degli anni ’80, Toyota riuscì a diventare un ledaer globale nel settore automotive.
Un successo non determinato da una manifesta superiorità tecnologica rispetto ai competitor, in molto casi la multinazionale giapponese ha agito infatti da folower tecnologico, abile a incorporare innovazioni tecnologiche di altri produttori. Le automobili costruite dalla Toyota si sono rivelate più affidabili e meno costose rispetto ai competitor occidentali.
In particolare, a partire dagli anni ’60 aumentò la domanda globale di autoveicoli, il mercato iniziò a frammentarsi e ciò a beneficio di Toyota che era in grado di offrire prodotti eterogenei aumentando in modo limitato i costi di produzione: la flessibilità e la produzione snella, appunto “lean” iniziavano a fare la differenza nel mercato globale.
La mission del modello Toyota Production System è ben espresso in un celebre aforisma di Taiichi Ohno “Tutto quello che dobbiamo fare è concentrarci sulle tempistiche, dal momento in cui riceviamo un ordine fino a quando incassiamo il pagamento, e fare di tutto per ridurle, eliminando le attività prive di valore aggiunto.”
Alla base del successo del Toyota Production System vi è un modello organizzativo originale che si fonda su:
- Strutture snelle con una riduzione dei livelli gerarchici;
- Introduzione sistematica dei gruppi di lavoro;
- Investimenti in formazione;
- Parziale sovrapposizione tra ruoli operativi e manageriali, in quanto agli operatori vengono attribuite autonomie decisionali e responsabilità collegate ai risultati.
Il termine "Lean Production" è stato coniato da John Krafick in un articolo del 1988 “Triumph of the lean production system", basato sulla sua tesi di laurea al MIT. Il termine è stato ripreso da Womack, Daniel T. Jones e Daniel Roos nel libro "La macchina che ha cambiato il mondo", in cui i tre studiosi hanno per primi analizzato il modello Toyota Production System (TPS), rivelando le ragioni della netta superiorità di quest'ultima rispetto ai competitor.
La "Lean Production" non è altro quindi che una divulgazione in Occidente del modello Toyota Production System (TPS). I tre autori riuscirono in particolare ad estrapolare i cinque principi applicativi del Lean Thinking:
- Value: Definizione del valore del prodotto in base al cliente finale;
- Value Stream Map: Mappatura delle attività che generano valore per il cliente;
- FLOW: tecnica che consiste nel rendere fluido e costante il processo delle attività che generano valore;
- PULL: Il cliente tira il valore della produzione;
- Perfection: Tendere alla perfezione del processo produttivo
I 5 principi portano a generare un valore per il cliente finale eliminando i MUDA (sprechi).
Taiichi Ohno aveva indivduato 7 MUDA:
- Difetti della produzione.
- Sovrapproduzione. Eccessiva produzione non necessaria.
- Scorte, cioè la presenza di magazzini con all’interno prodotti in attesa di lavorazione. A tal proposito Taiichi Ohno riteneva che: “Più materiale c'è a magazzino, meno probabilità c'è che si trovi ciò di cui si ha bisogno.”
- Extra lavorazione, processi inutili, la presenza di lavorazioni non necessarie.
- Movimentazioni non necessarie di persone.
- Trasporti eccessivi o non necessario di materiali.
- Attesa. Il verificarsi di code, come conseguenza dell’attesa del termine delle attività a monte o l’attesa del completamento dei processi svolti dai macchinari.
È possibile individuare un nono MUDA, legato alla qualità della Formazione professionale dei dipendenti.
I 3 autori americani hanno individuato un ulteriore MUDA, consistente nella progettazione di beni e servizi che non soddisfano i bisogni dei clienti.
L'applicazione dei principi Lean Production
L’introduzione dei principi Lean Production in un’impresa tradizionale è una sfida ambiziosa e complessa. In media l’introduzione della Lean Production ha una durata superiore ai 5 anni e il tasso di fallimento è superiore al 50%. La fase più delicata è l’introduzione della cultura Lean Production in tutti i livelli dell’organizzazione aziendale. In particolare i maggiori ostacoli sono stati riscontrati nei livelli intermedi, in quanto i più impattati dall’introduzione della filosofia organizzativa/produttiva.
Per questa ragione, come evidenziato dagli studi di Ikujiro Nonaka, i manager intermedi, in quanto anello di congiunzione tra il top management e i livelli operativi, sono fondamentali per rendere concreta la scelta dei vertici di introdurre la Lean Production in azienda. A tal fine è necessario rassicurarli, dando loro un chiaro percorso di crescita professionale e di carriera.
Negli anni novanta i maggiori competitor statunitensi ed europei hanno provato ad imitare il modello giapponese, trovando diverse difficolta una volta calato il modello nel conteso socioeconomico occidentale: in particolare il forte ruolo del sindacato in occidente, il livello di scolarizzazione della forza lavoro e una diversa cultura aziendale. Gli stessi insediamenti del Toyota Production System in Occidente si sono rivelati meno efficienti degli stabilimenti giapponesi.
Nel settore automobilistico negli ultimi anni, attori indiani e cinesi stanno adottando modelli lontani dai principi "Lean Production". In contesti socioeconmici caratterizzati da una bassa sindacalizzazione, bassi livelli di delega, forte ricorso alla gerarchia oltre ad un’organizzazione del lavoro caratterizzata da una maggiore separazione tra ruolo manageriale e mansioni operative, il metodo lean può risultare inefficace.
In Paesi in cui il costo del lavoro è più basso che in Occidente o Giappone, è quindi possibile produrre a costi competitivi nonostante un basso livello di produttività. Il fordismo, superato dalla Lean Production, ritrova quindi nuova linfa in Oriente. Ciò a dimostrazione del fatto che sono soprattutto i fattori ambientali e socioeconomici a rendere efficace un modello organizzativo o inefficace un altro.
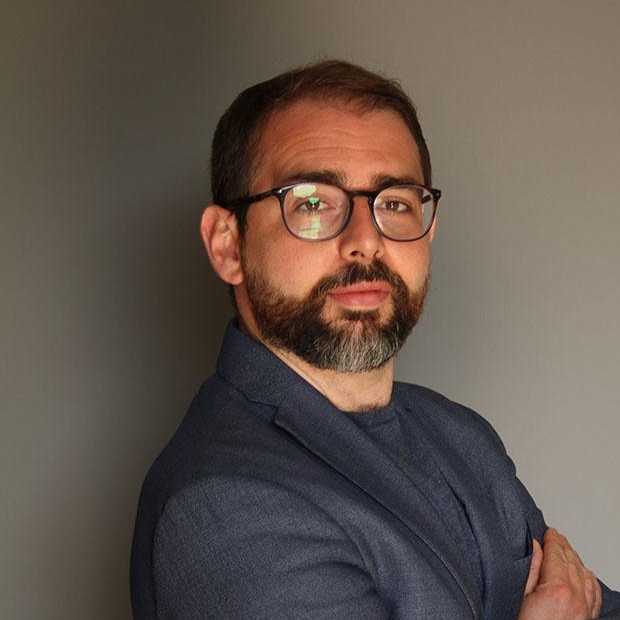
Pasquale Fierro
Consulente Strategico d'impresa
Consulente di esperienza nel settore aziendale industriale, l’obiettivo principale che muove la sua attività ogni giorno è la soddisfazione dell’imprenditore nella ricerca delle opportunità per aumentare l'efficienza delle PMI.
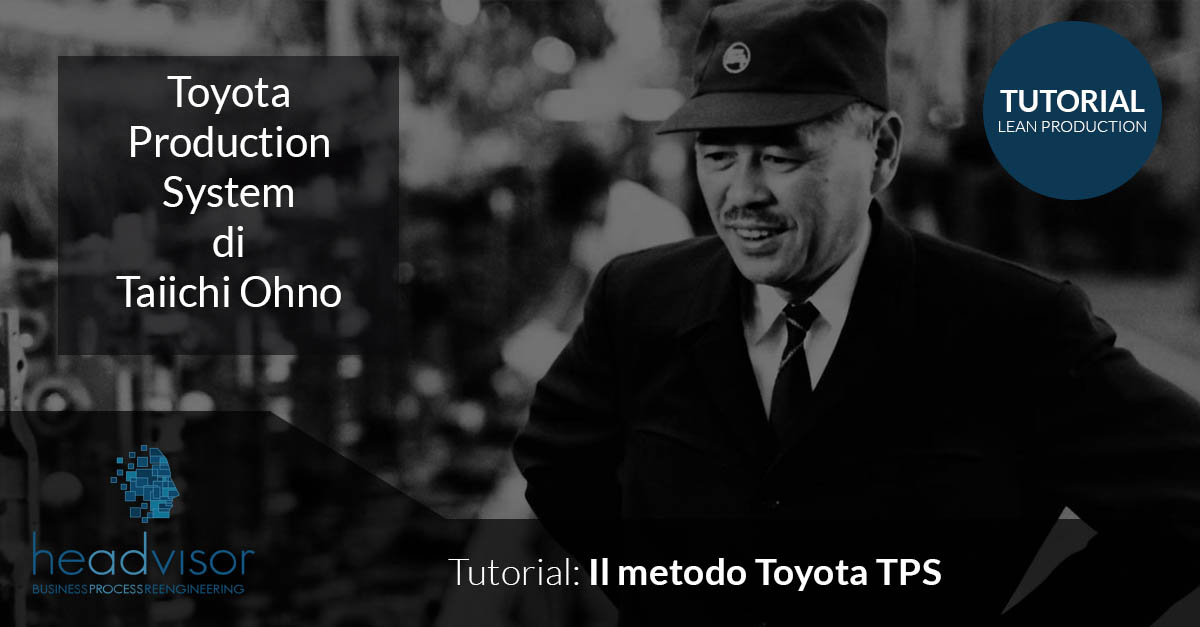
Chiedici una consulenza gratuita
I nostri esperti sono a tua disposizione!
Gli operatori circolano nei reparti della tua azienda con fogli di carta? La pianificazione della produzione è manuale o effettuata con Excel?
Sai esattamente quanto è il tuo livello di produzione? Quanto scarto produci? Quante rilavorazioni per inefficienze? Quante materie prime impieghi?
Tramite un processo di efficientamento è possibile implementare soluzioni tengibili, per ottimizzare al meglio ogni processo e migliorare il livello di efficienza.
Tutto il nostro team è a tua disposizione, per qualunque esigenza.
Leggi i Tutorials più recenti
Strumenti per efficientare le imprese
Core Tools Automotive: l’importanza degli strumenti “Core”
Core tools automotive: gli strumenti chiave da conoscere per lavorare come controller, project manager e dirigenti nel settore automotive.... [Continua a Leggere]
Metodo Hoshin Kanri per la pianificazione strategica
Hoshin Kanri è un metodo di gestione strategica della lean production che permette di allineare gli obiettivi strategici di un'azienda con le sue operazioni quotidiane... [Continua a Leggere]
ESRS: gli standard europei per il reporting sulla sostenibilità
ESRS: gli standard che definiscono le linee guida per la rendicontazione sostenibile delle aziende in Europa. Scopri cosa sono in questo articolo... [Continua a Leggere]
CSDDD o CS3D: cosa è e cosa prevede la nuova direttiva europea
CSDDD o CS3D perché è nata questa normativa europea? a chi è rivolta? entro quando entrerà in vigore?... [Continua a Leggere]
Sostenibilità aziendale: come migliorare le performance sostenibili
La sostenibilità aziendale è un concetto fondamentale per le aziende moderne. Come implementare soluzioni sostenibili per il prossimo futuro?... [Continua a Leggere]
Balanced scorecard: la guida completa
Balanced Scorecard BSC è la scheda di valutazione bilanciata per la gestione strategica e la misurazione dei risultati aziendali nelle diverse aree.... [Continua a Leggere]
Analisi PEST e analisi PESTEL
Analisi PESTEL (anche conosciuta come PEST o PESTLE) permette di evidenziare tutti i fattori esterni che possano condizionare lo sviluppo di una azienda o business... [Continua a Leggere]
La Carbon Footprint aziendale: 9 tecniche e metodi per la stima degli impatti di emissioni in atmosfera
Carbon Footprint aziendale: tecniche e metodi per la stima degli impatti di emissioni in atmosfera e rendicontazione nel bilancio di sostenibilità... [Continua a Leggere]
Margine di Contribuzione: Cos’è, Calcolo ed Esempi
Il margine di contribuzione è un indice fondamentale per valutare la redditività dei prodotti creati dall'azienda. Leggi questo articolo per saperne di più... [Continua a Leggere]
Just in Time: efficienza in produzione e logistica
Il just in time è una strategia di gestione che permette di ridurre gli sprechi e rendere più efficiente e coordinato il reparto produzione.... [Continua a Leggere]
WBS (Work Breakdown Structure): cos'è e come utilizzarla
La WBS è lo strumento di ripartizione del lavoro per suddividerlo in compiti più piccoli e renderlo più gestibile, controllabile e accessibile.... [Continua a Leggere]
Break Even Point (BEP) - come calcolare il punto di pareggio
Il Break Even Point è una formula per calcolare il punto di pareggio. Il valore in cui i profitti e i costi di un’attività aziendale sono in equilibrio.... [Continua a Leggere]
Sistemi di Efficientamento organizzativo
Gli strumenti per efficientare la tua impresa
L'analisi e la mappatura dei processi di un'organizzazione, consentono di riorganizzare le attività, razionalizzare l'uso delle risorse, incrementare l’efficacia, l’efficienza ela produttività della struttura stessa.
I nostri servizi a supporto di imprese:
- Mappatura dei processi interni, gestionali e organizzativi
- Analisi e ottimizzazione delle prestazioni dei processi individuati
- Analisi e riduzione dei costi di gestione
- Ridefinizione dei processi con l'obiettivo di migliorare l'efficienza dell'organizzazione e delle sue prestazioni
- Progettazione di Innovazione tecnologica e digitalizzazione dei processi
- Progettazione di economia circolare