One Piece Flow
One Piece Flow, o Single Piece Flow, è un concetto legato alla Lean Production e al sistema TPS (Toyota Production System). Si riferisce ad un approccio che ha l'obiettivo di ridurre gli sprechi di produzione (MUDA) e migliorare l'efficienza attraverso la produzione di un singolo pezzo per volta, senza lavorare su grandi lotti produttivi.
Il termine One Piece Flow indica perciò un flusso produttivo in cui viene prodotto “un pezzo alla volta”.
Per comprendere questo concetto, prendiamo come esempio un prodotto sul quale vanno effettuate tre lavorazioni (1, 2 e 3) e un lotto da 50 pezzi. Invece di lavorare 50 pezzi durante la prima lavorazione, poi 50 durante la seconda lavorazione e infine 50 pezzi durante la lavorazione 3, utilizzando il metodo One Piece Flow ogni pezzo viene lavorato di seguito, eseguendo in successione le lavorazioni 1, la 2 e la 3, contrapponendosi al metodo di produzione per lotti.
Nelle aziende che adottami la filosofia Lean Thinking, l'obiettivo ideale è quello di passare da una produzione per lotti push, in cui si ha una frammentazione di semilavorati, ad una produzione pull, i cui il flusso produttivo è “tirato” dalla domanda puntuale del cliente (es metodo Kanban).
L'applicazione di questa metodologia ha come conseguenza principale la riduzione dei tempi di ciclo, o Lead Time, poiché vengono ridotte al minimo le attività di tipo "NON a valore aggiunto", spesso riguardanti la movimentazione dei prodotti. Utilizzando il One Piece Flow diventa inoltre possibile ottimizzare l'inventario e migliorare la flessibilità del processo produttivo.
Realizzando i prodotti uno alla volta, è possibile poi individuare e risolvere eventuali problemi ed inefficienza in modo rapido, riducendo i tempi d'attesa e migliorando la qualità complessiva del prodotto.
In sintesi, il One Piece Flow riguarda la produzione continua di un singolo pezzo o prodotto per volta, permettendo di evitare la presenza di grandi quantità di materiale in stock o inventario di tipo inattivo e ottimizzando il flusso di lavoro.
Esempio di produzione One Piece Flow
Per comprendere cos'è il One Piece Flow, e capire quali vantaggi porta in termini di efficienza produttiva, spiegheremo il ciclo produttivo descritto in figura.
La parte sinistra dell'immagine mostra una normale produzione a lotti, mentre quella a destra una produzione che sfrutta il metodo One Piece Flow. Si tratta di un esempio semplice e intuitivo che non tiene conto di alcune variabili ma che ci permette comunque di comprendere come, implementando questo approccio a produzioni con volumi maggiori, si possono ottenere enormi vantaggi.
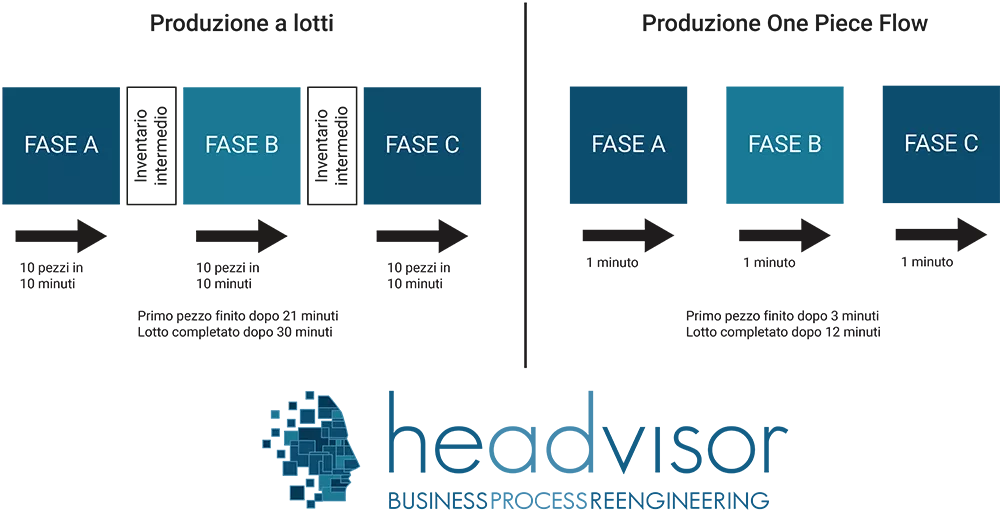
I vantaggi del One Piece Flow
Ecco alcuni vantaggi ottenibili sfruttando il metodo One Piece Flow:
- Più qualità e meno difetti: One Piece Flow permette di ridurre diversi sprechi di produzione (MUDA). In particolare, grazie al miglioramento della qualità di prodotto, si hanno meno difetti sui prodotti finali.
- Riduzione degli sprechi di inventario: il One Piece Flow è collegato alla produzione di tipo pull e al JIT Just In Time. Vengono perciò ridotti gli sprechi di gestione a stock (muda inventory) e, in particolare, si ottiene una gestione efficiente dell'inventario intermedio.
- Maggiore efficienza: con questo approccio vengono ottimizzati i tempi di ciclo complessivi, riducendo i tempi di attesa e migliorando la produttività globale.
- Flessibilità operativa: il sistema è progettato per adattarsi in modo agile a diverse condizioni, consentendo una risposta rapida a cambiamenti della domanda e variazioni nelle specifiche di prodotto.
- Miglior controllo qualità: vengono ridotte le probabilità di errori e difetti nei prodotti, poiché ogni pezzo è soggetto ad una maggiore attenzione durante le lavorazioni.
- Riduzione dei tempi di avvio e arresto: il metodo One Piece Flow consnete di ridurre i tempi di avvio e arresto dei macchinari, poiché il flusso produttivo è continuo.
- Risparmio di spazio: i pezzi vengono trasferiti direttamente da una fase a quella successiva, senza la necessità di creare aree di stoccaggio (supermarket) intermedie le quali, inoltre, possono mettere a rischio la sicurezza degli operatori.
- Risoluzione di problemi: un flusso continuo rende chiara e ben visibile la catena di valore (Value Stream)e il flusso di lavoro, permettendo di individuare problemi ed inefficienze lungo il ciclo produttivo.
- Magazzino WIP basso: il One Piece Flow mantiene basso il magazzino della lavorazione WIP (Work In Progres), favorendo il livellamento dei carichi di lavoro.
Come implementare il One Piece Flow
Implementare il metodo One Piece Flow nella propria azienda richiede tempo, impegno e la cooperazione di tutti gli operatori. Inoltre, essendo una produzione di tipo Pull, sarà necessario prendere accordi vantaggiosi con i fornitori, in modo da avere sempre a disposizione un costante approvvigionamento di materiali per mantenere attivi i processi produttivi.
Potrebbe essere vantaggioso introdurre dei cambiamenti graduali, in modo da migliorare l'intera operatività di reparto alla nuova metodologia.
Ecco una possibile serie di operazioni da mettere in atto per implementare il sistema One Piece Flow, ricordando che queste possono variare in base alla tipologia di produzione e azienda.
- Analisi dei processi: il primo passo riguarda l'analisi dei processi attuali, individuando sprechi operativi, punti critici e le aree in cui si accumulano maggiori stock di produzione. È possibile fare ciò attraverso analisi As-Is o analisi Current State Map - CSM .
- Mappatura del flusso di valore: la Value Stream Mapping permette di visualizzare chiaramente il passaggio di ogni pezzo attraverso le diverse fasi del processo. Questo ci permette di identificare opportunità di miglioramento e riduzione degli sprechi operativi.
- Definizione degli standard di lavoro: serve definire degli standard chiari per ciascuna fase del processo, come tempi di ciclo, procedure operative standard (SOP – Standard Operative Procedures) e obiettivi di Qualità.
- Riorganizzare il layout e la produzione: questa è chiaramente la fase più delicata e che richiede particolare
attenzione.
Per riorganizzare la produzione, si può partire dalla riduzione degli stock intermedi presenti tra le varie
fasi di lavoro, incoraggiando un flusso continuo lungo la catena produttiva.
Per raggiungere il modello One Piece Flow saranno necessarie diverse attività, tra cui una revisione delle politiche di riordino e gestione dell'inventario e una nuova organizzazione del layout di produzione che faciliti il flusso continuo. Ad esempio con l'introduzione anche di rulliere o corridoi di scorrimento per i semilavorati in produzione. - KPI e miglioramento continuo: dopo aver completato la fase precedente, la produzione dovrebbe essere in grado di creare un flusso continuo tra le varie fasi produttive. A questo punto è importante implementare il One Piece Flow gradualmente, monitorando le performance attraverso il monitoraggio di KPI Key Performance Indicator e identificando nuove aree che possono essere migliorate, in ottica di miglioramento continuo (secondo il tipico modello Kaizen per il miglioramento continuo).
Chiedici una consulenza gratuita
I nostri esperti sono a tua disposizione!
Gli operatori circolano nei reparti della tua azienda con fogli di carta? La pianificazione della produzione è manuale o effettuata con Excel?
Sai esattamente quanto è il tuo livello di produzione? Quanto scarto produci? Quante rilavorazioni per inefficienze? Quante materie prime impieghi?
Tramite un processo di efficientamento è possibile implementare soluzioni tengibili, per ottimizzare al meglio ogni processo e migliorare il livello di efficienza.
Tutto il nostro team è a tua disposizione, per qualunque esigenza.
Leggi i Tutorials più recenti
Strumenti per efficientare le imprese
Core Tools Automotive: l’importanza degli strumenti “Core”
Core tools automotive: gli strumenti chiave da conoscere per lavorare come controller, project manager e dirigenti nel settore automotive.... [Continua a Leggere]
Metodo Hoshin Kanri per la pianificazione strategica
Hoshin Kanri è un metodo di gestione strategica della lean production che permette di allineare gli obiettivi strategici di un'azienda con le sue operazioni quotidiane... [Continua a Leggere]
ESRS: gli standard europei per il reporting sulla sostenibilità
ESRS: gli standard che definiscono le linee guida per la rendicontazione sostenibile delle aziende in Europa. Scopri cosa sono in questo articolo... [Continua a Leggere]
CSDDD o CS3D: cosa è e cosa prevede la nuova direttiva europea
CSDDD o CS3D perché è nata questa normativa europea? a chi è rivolta? entro quando entrerà in vigore?... [Continua a Leggere]
Sostenibilità aziendale: come migliorare le performance sostenibili
La sostenibilità aziendale è un concetto fondamentale per le aziende moderne. Come implementare soluzioni sostenibili per il prossimo futuro?... [Continua a Leggere]
Balanced scorecard: la guida completa
Balanced Scorecard BSC è la scheda di valutazione bilanciata per la gestione strategica e la misurazione dei risultati aziendali nelle diverse aree.... [Continua a Leggere]
Analisi PEST e analisi PESTEL
Analisi PESTEL (anche conosciuta come PEST o PESTLE) permette di evidenziare tutti i fattori esterni che possano condizionare lo sviluppo di una azienda o business... [Continua a Leggere]
La Carbon Footprint aziendale: 9 tecniche e metodi per la stima degli impatti di emissioni in atmosfera
Carbon Footprint aziendale: tecniche e metodi per la stima degli impatti di emissioni in atmosfera e rendicontazione nel bilancio di sostenibilità... [Continua a Leggere]
Margine di Contribuzione: Cos’è, Calcolo ed Esempi
Il margine di contribuzione è un indice fondamentale per valutare la redditività dei prodotti creati dall'azienda. Leggi questo articolo per saperne di più... [Continua a Leggere]
Just in Time: efficienza in produzione e logistica
Il just in time è una strategia di gestione che permette di ridurre gli sprechi e rendere più efficiente e coordinato il reparto produzione.... [Continua a Leggere]
WBS (Work Breakdown Structure): cos'è e come utilizzarla
La WBS è lo strumento di ripartizione del lavoro per suddividerlo in compiti più piccoli e renderlo più gestibile, controllabile e accessibile.... [Continua a Leggere]
Break Even Point (BEP) - come calcolare il punto di pareggio
Il Break Even Point è una formula per calcolare il punto di pareggio. Il valore in cui i profitti e i costi di un’attività aziendale sono in equilibrio.... [Continua a Leggere]
Sistemi di Efficientamento organizzativo
Gli strumenti per efficientare la tua impresa
L'analisi e la mappatura dei processi di un'organizzazione, consentono di riorganizzare le attività, razionalizzare l'uso delle risorse, incrementare l’efficacia, l’efficienza ela produttività della struttura stessa.
I nostri servizi a supporto di imprese:
- Mappatura dei processi interni, gestionali e organizzativi
- Analisi e ottimizzazione delle prestazioni dei processi individuati
- Analisi e riduzione dei costi di gestione
- Ridefinizione dei processi con l'obiettivo di migliorare l'efficienza dell'organizzazione e delle sue prestazioni
- Progettazione di Innovazione tecnologica e digitalizzazione dei processi
- Progettazione di economia circolare