Tempo di lettura: 6 min
Indice
I 7 sprechi MUDA: Movimento
Roma aveva i suoi 7 Re e Toyota i suoi 7 MUDA o 7 sprechi.
Questa traduzione non rende l’idea di come veniva vissuta l’inefficienza negli anni in cui Taiichi Ono creò la “filosofia” produttiva TPS e poi chiamata "Lean Thinking".
La vera traduzione di MUDA è “che reca disonore”, infatti il termine spreco deriva dalla Occidentalizzazione di questo concetto.
Nel resto del mondo (fuori dal Giappone) l’errore non viene vissuto come un peccato capitale da punire aspramente ma semplicemente come una conseguenza dello stesso lavoro svolto, men che meno nel bel paese…infatti un vecchio proverbio recita così:
“Fare e disfare è tutto un lavorare”
I 7 MUDA rappresentano quindi quello che nel Giappone del dopo guerra veniva visto come una inefficienza obbligatoriamente da risolvere.
Nelle prossime righe parleremo di MUDA Movimento, uno spreco che accomuna, con una linea sottile, tutte le tipologie di realtà produttive e non, dalle ETO (Engineer to Order) alle DTS (Delivery to Order) e cioè lo spreco dei movimenti (Muda-Motion).
Movimento, Movimentazioni e spostamenti inutili (MUDA-Motion)
Dal dizionario Treccani “Organizzazione del movimento delle merci in un magazzino, regolato in base al flusso dei rifornimenti e degli ordini di consegna”.
Fanno parte di questa categoria tutti quegli spostamenti che avvengono all’interno dello stabilimento aziendale o nell’area produttiva.
Il MUDA movimento sono uno dei 7 sprechi della Lean Production perché quasi nella loro totalità rientrano in quelle azioni che non portano valore, dette anche NVA (Not Value Added), cioè tutte quelle operazioni per cui il “cliente” non è disposto a pagare e quindi sono semplicemente un costo per l’azienda.
Per antonomasia gli sprechi andrebbero eliminati per portare beneficio al sistema ma come è ovvio questo non è totalmente fattibile. È possibile invece minimizzare i MUDA o sprechi fino allo stretto necessario seguendo i diktat della Lean Production.
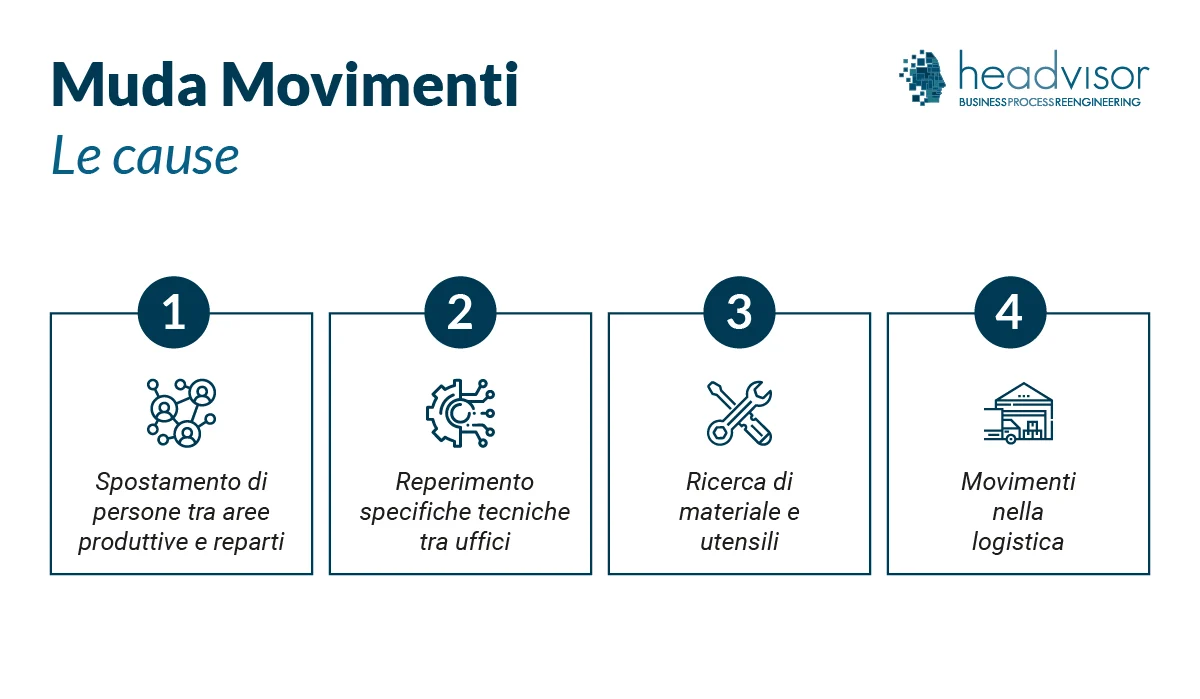
Analisi del problema inefficienza di logistica
Current State MAP (CSM) è l’analisi in cui si definisce in modo oggettivo lo stato As-Is della situazione di partenza.
Per comprendere appieno il problema quindi si parte facendosi delle semplici domande, ebbene anche per il MUDA Movimento serve partire dall’analisi della situazione e quindi chiedersi ad esempio:
Nel Magazzino:
- Dove si trova l’ingresso della merce?
- Come è posizionato il magazzino rispetto alle unità produttive?
- Che dimensioni ha il magazzino?
- Come è organizzato? Scansie, pallet, scaffali e le automazioni?
- Che compiti deve svolgere il magazziniere?
- Come viene svolta l’accettazione merce?
- Quante volte viene percorso il magazzino dagli operatori?
- Quanti carichi e scarichi vengono fatti?
- L'allestimento delle scansie è ottimizzato?
- La merce ad alta rotazione è più vicina alle linee di produzione?
- Quanto materiale di “ristagno” potrebbe essere smaltito per dar spazio alla logistica migliorandone i percorsi?
- le scansie sono facilmente accessibili o serve qualche scaletto o transpallet scomodo e di cui gli operatori devono rubarsene l'utilizzo?
- Il layout della logistica, è ottimizzato per ridurre gli spostamenti?
- Ecc ecc
Nella produzione:
- Gli operatori si allontanano frequentemente dalle loro postazioni? perché?
- I centri di produzione sono studiati ergonomicamente per ridurre i movimenti degli operatori?
- La produzione si ferma spesso per mancanza di materiale?
- il bordo-macchina o WIP (Work in progress) ha capienza sufficiente per il supermarket di stock?
- i lotti di approntamento sono adeguatamente calibrati?
- i materiali accessori o di utilizzo comune sono sempre ben presenti alle postazioni
- il versamento del semilavorato viene posto in prossimità? C'è un addetto allo stock o serve cercare spazio ogni volta?
- il controllo qualità è lontano dalla produzione?
- Il controllo qualità è ben allineato con i reparti produttivi?
- Il Layout delle linee di produzione è disegnato in modo efficiente?
- Ecc ecc
Definire l’inefficienza
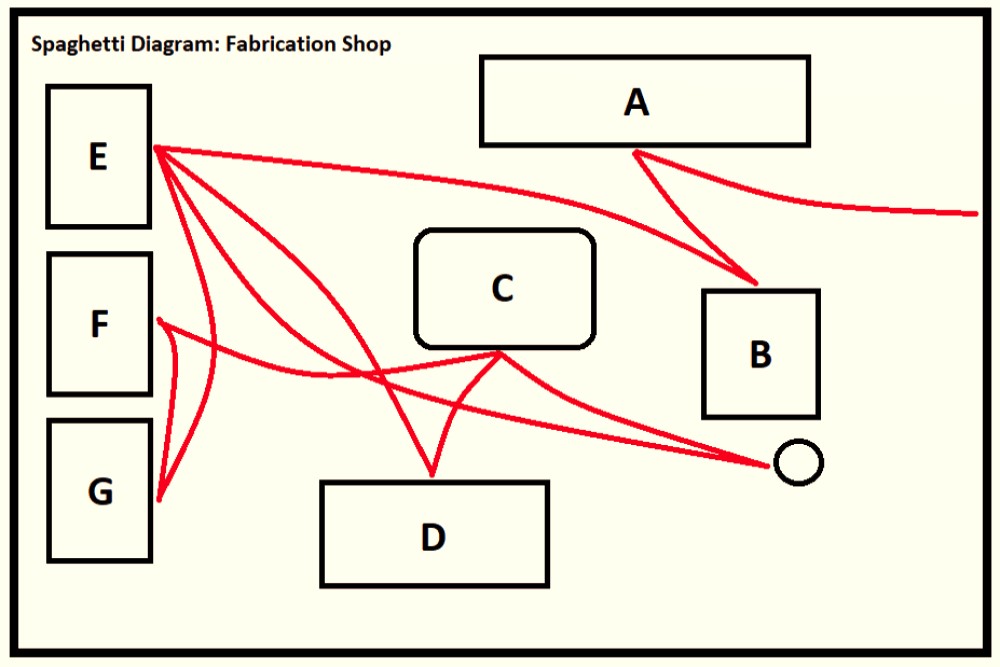
Uno metodo schematico che possa aiutare in modo semplice ed immediato a raccogliere tutto il flusso di spostamenti all’interno di uno stabilimento è lo Spaghetti Diagram o Spaghetti chart.
Serve disegnare il layout dello stabilimento o dell’area interessata e qualche ora di tempo per vedere e disegnare i collegamenti tra un’isola e l’altra o tra un reparto e l’altro.
L’immagine è molto stilizzata ma rende l'idea della moltitudine di movimenti che vengono effettuati ogni giorno. Questo diagramma fa leva soprattutto sull'evidenziare i movimenti a colpo d’occhio.
L’operazione sopra descritta andrebbe eseguita in più momenti della giornata al fine di conoscere esattamente l’entità degli spostamenti e l'inefficienza operativa del MUDA Movimento (MUDA Motion).
Oltre che disegnare il flusso degli spostamenti, Spaghetti Chart risulterà molto importante, per quantificare lo spreco, (MUDA Movimento) il problema, e trasformare queste semplici righe in numeri e percentuali (CTQ Critical To Quality).
Definendo le criticità di logistica e magazzino verranno evidenziati gli eventuali atteggiamenti sbagliati come potrebbero essere la disorganizzazione delle posizioni dei materiali, delle consegne, dei ritiri oppure semplicemente la cattiva gestione degli spazi di accettazione, controllo qualità e stoccaggio merci.
Misurare l’inefficienza
Una volta iniziato a focalizzare lo spreco è necessario misurare numericamente il costo in termini di tempo dell’inefficienza.
Per avere il polso degli sprechi infatti non ci si può affidare alle sole sensazioni visive o percezioni, bisogna parlare di numeri. Serve quindi raccogliere dati che poi dovranno essere misurati, pesati, con l’utilizzo di metodi anche molto semplici.
Ma se si volesse solo migliorare un po’? Senza dover raccogliere dati allo sfinimento per analizzarli?
Tutto si può fare, tuttavia gli eventuali miglioramenti non sarebbero quantificabili in termini numerici il che vorrebbe dire non avere il pieno controllo della situazione evolutiva.
L’attività di efficientamento deve poter rispondere in modo numerico alle aspettative, servono quindi dati che diano risposte concrete:
- Gli spostamenti sono diminuiti? di quanto?
- Quanto è costato questo nuovo layout prototipale?
- Quanto costerà mantenere questi nuovi standard?
- La nuova soluzione è estendibile ad altri operatori e aree?
- Il controllo è aumentato di quanto?
- Ecc. ecc
La raccolta dati e la misurazione degli sprechi non deve essere considerata un optional, va fatta sempre ed i dati vanno statisticati per avere un rendiconto di quello che era e di quello che è la nuova situazione nella fase di controllo e check.
Troppe volte si cade nell’errore di non avere la reale percezione della situazione esistente, i numeri sono univoci perché non danno possibilità di fraintendimenti.
Grazie ai dati poi sarà possibile attuare tutti i correttivi necessari, magari comprendendo ad esempio che il reparto è sottodimensionato anche a livello di risorse o sovra-strutturato a livello di mezzi.
Analizzare e misurare serve ad andare a fondo del problema non fermandosi ai sintomi ma proseguendo fino alla radice del problema (root-cause).
Tuttavia, durante il processo, non bisogna perdere di vista il vero obbiettivo di queste misurazioni, voler minimizzare gli sprechi di movimento.
Ricapitoliamo i passaggi fatti fino ad ora:
- Definito il problema.
- Analizzato lo stato attuale
- Raccolto dati oggettivi
- Ricercato le cause radice
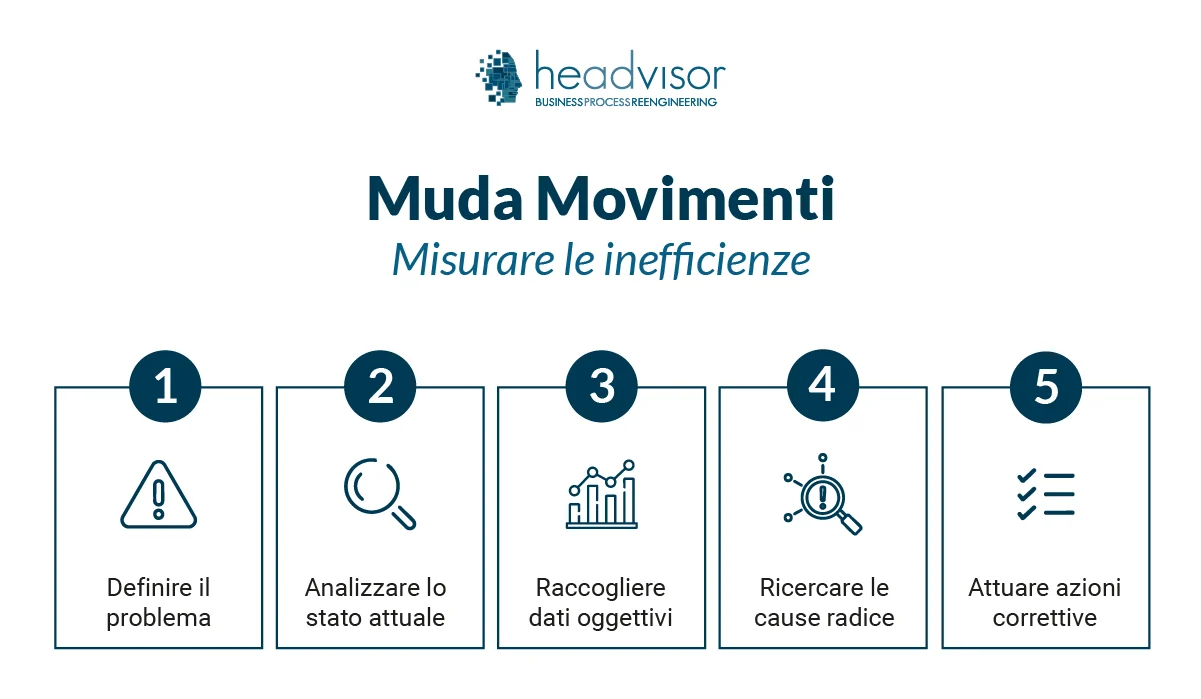
Analisi attuativa - Comprendere come migliorare:
Ora è arrivato il momento di mettere in atto delle operazioni correttive.
Queste correzioni dovranno essere direttamente collegate all’entità del problema rilevato.
Pareto affermava che il 20% delle cause provoca l’80% degli effetti, questo sta a significare che non bisogna esaminare e migliorare tutte le criticità ma che invece serve concentrarsi sui principali problemi che incidono maggiormente rispetto ad altri.
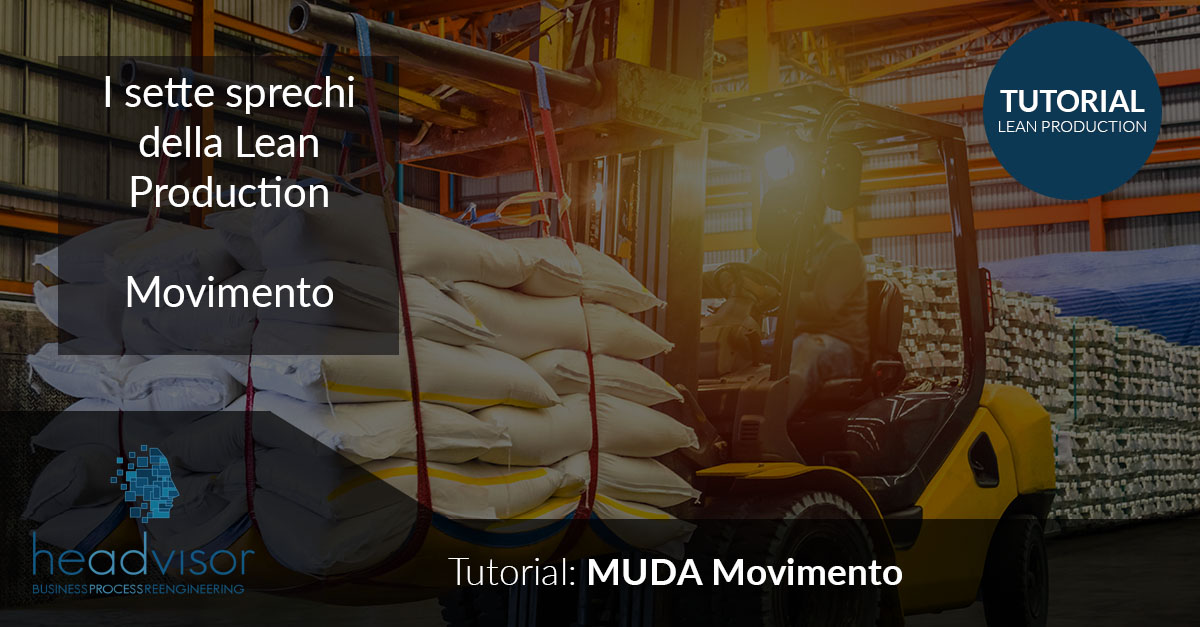
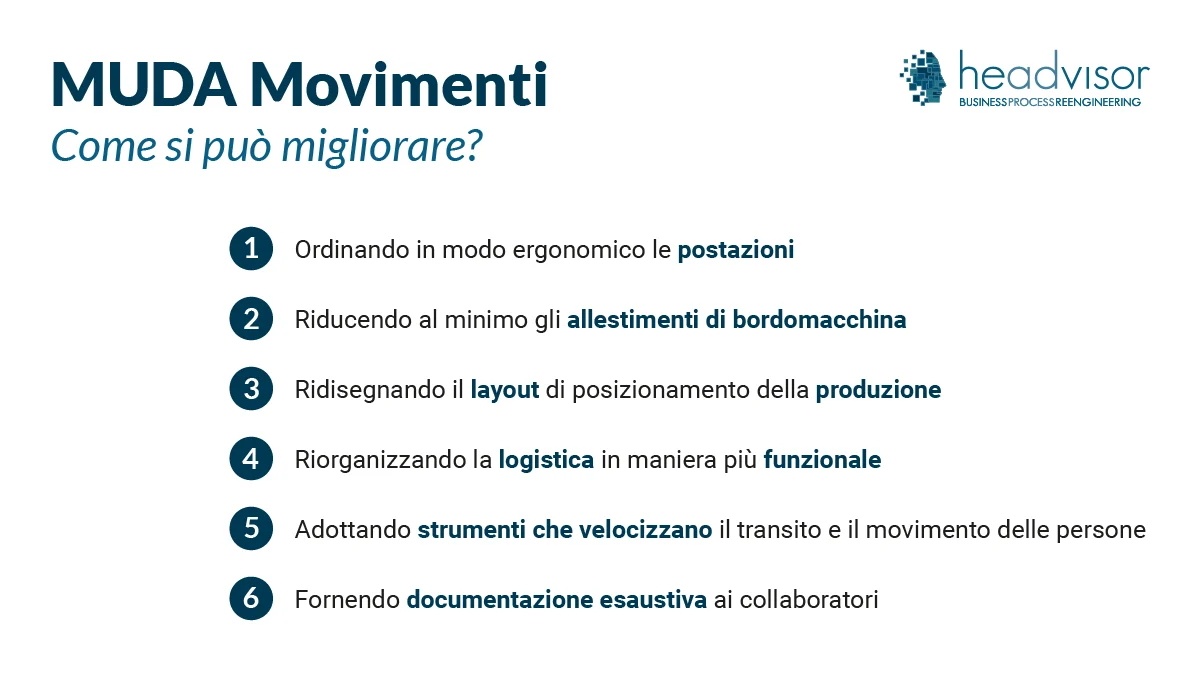
Un esempio di MUDA Movimento
Prendiamo ad esempio un problema costante in molte aziende, i corrieri attendono troppo tempo per essere caricati e scaricati. Tutti passano per un solo molo di carico, uno alla volta.
Il magazzino è organizzato su due turni da otto ore: 6/14 e 14/22.
Gli operatori hanno turni fissi quindi l’operatore A fa sempre il 1° turno e l’operatore B sempre il 2°.
Proviamo a quantificare il troppo tempo rendendo questo aggettivo un numero.
La durata minima di attesa è 2’ e quella massima 20’, con una media di 11’ e una moda di 6’
Questi dati non dicono nulla se non ci si pongono dei limiti di accettabilità massima.
Secondo la proprietà i corrieri devono aspettare al max 4’ il che vuol dire che siamo lontani dall’obiettivo.
Andiamo oltre i soli numeri e stratifichiamo l’analisi anche per fascia oraria.
La maggior parte dei carichi e scarichi avvengono dalle 8:00 alle 15:00.
Le attese più lunghe avvengono di mattina, si potrebbe saltare alle conclusioni accusando l’operatore A di scarsa produttività eppure andando a fondo si scopre che in quel lasso di tempo l’operatore A svolge anche attività non annesse al ricevimento merci, come l’allestimento della logistica per il reparto qualità (che lavora dalle 8 alle 14), oltre la distribuzione di materiale ad alto consumo nelle postazioni produttive, oltre a questo non possiede un telefono portatile per essere avvisato del arrivo di un corriere.
Si era partiti con l’idea che l’operatore del primo turno fosse poco produttivo e si è arrivati acapire invece che il carico di lavoro nella fascia iniziale della giornata è maggiore rispetto a quella che avviene dalle 12 alle 22.
Verifichiamo non solo la forza lavoro ma anche quella dei mezzi.
Per movimentare c’è la necessità primaria di carrelli, carriponte, transpallet, muletti, questi mezzi sono adeguati?
Ad esempio per lo scarico di mezzi pesanti, di quanti carrelli elevatori ha a disposizione il magazzino?
La risposta magari è uno solo, che potrebbe anche bastare ovviamente, tuttavia è condiviso con tutto il resto dell’azienda, magari altri 12 operatori che mediamente impegnano giornalmente il mezzo per soli 135’ e non consecutivi.
Aggiungiamo che il magazzino non sia ottimizzato per il carico e scarico con carrello ma dopo aver scaricato i pallet, gli stessi dovranno essere spostati con mezzi manuali perché le scansie sono troppo strette o sono presenti soppalchi.
Potremmo concludere, senza andare ad approfondire oltre l’analisi, che il problema sembra chiaro e si potrebbe intervenire in svariati modi. Pensiamo quindi alcune proposte da attuare e di cui poterne trarre misurazioni.
E' ipotizzabile aumentare i moli di ingresso? Possono i corrieri essere già dotati di un codice di accettazione via app o via portale Web?
Qualora si voglia comunque procedere per passi più piccoli:
- Attrezzare l’operatore A di un telefono DEC con controllo remoto del citofono e dell’ingresso di carico scarico
- Sgravare il turno della mattina di certe operazioni che potrebbero essere suddivise su altri operatori (magari anticipare al giorno prima facendole fare all’operatore B).
Volendo agire per piccoli passi queste potrebbero essere comunque delle attività migliorative quantificabili quindi misurabili nell’immediato.
- Riduzione delle attese e un abbassamento della media dei tempi.
- Migliore distribuzione del carico lavoro tra operatore A ed operatore B.
Nel caso che i dati rientrino già nel limite di accettabilità imposto dalla proprietà ci si potrebbe fermare a questi interventi.
Un’altra soluzione economica potrebbe essere invece quella di aumentare la programmazione dei carichi e scarichi, in accordo con fornitori e clienti, dalle 15 alle 17:30 sgravando così l’operatore A di una percentuale di essi.
Se il livello di efficienza atteso giustifica un intervento più importante si potrebbe ragionare su una riorganizzazione della logistica:
- Modificare il layout del magazzino, disporre gli articoli in maniera più funzionale
- Gli articoli a maggior rotazione nei pressi dei centri di lavoro
- Le scorte nella parte più alta delle scansie
- Spostare la ricambistica al di fuori delle linee di passaggio o addirittura fuori dalla superficie logistica
- Segnalare e delimitare le aree di molo allestimento, di WIP, Controllo Qualità Molo di spedizione, Accettazione merce ecc
- Automatizzando una parte del lavoro attualmente svolto manualmente.
- Dotarsi di infrastruttura elettronica e di controllo visivo e auditivo che diano lo stato di salute della logistica
- Testare l’inserimento di una nuova figura per il solo allestimento a bordo macchina
- Testare l’utilizzo di logiche Kanban per l’allestimento di contenitori per la produzione
- Investendo in attrezzature, come ad esempio l’acquisto di scaffalature più consone al tipo di prodotto o aumentando il parco mezzi per le movimentazioni che creano un vincolo non indifferente.
Kaizen, migliorare per piccoli passi e MUDA Movimento
Per nulla secondaria alla fase pratica è la parte psicologica, procedere a piccoli passi rendendo il cambiamento più gestibile e contenuto è alla base della filosofia Kaizen - Miglioramento continuo.
Questo atteggiamento aumenterebbe di molto le possibilità di collaborazione e consenso degli operatori interessati e quindi della riuscita del progetto di miglioramento.
POC Proof of concept e MUDA Movimento
Ripetutamente si è fatto riferimento ai vantaggi di eseguire Test, fasi di prototipazione, simulazioni ecc..
Nulla può essere più efficace e ben visto dagli operatori come quello di eseguire una prova di fattibilità.
Ma che vantaggi porta un POC Proof of Concept?
- Possibilità di gestire una problematica più contenuta
- Contenere i costi
- Contenere l’impegno di risorse
- Ridurre i tempi di attesa per verificare i miglioramenti
Nel caso il POC - Proof of Concept andasse a buon fine si potrebbe “allargare” questo approccio a tutto il resto delle criticità di reparto e non solo.
La vera filosofia di Taiichi sta proprio in questa fase di implementazione detta Lean Thinking, “miglioramento continuo”.
Mantenere il controllo e cercare il miglioramento continuo
Arrivati a questo punto il lavoro consisterà nel tener monitorati i risultati dei “miglioramenti” messi in atto, che sia una semplice prova su un solo campione oppure una rivoluzione ingegneristica della produzione.
Quantificare i miglioramenti vuol dire tener viva l’attenzione sull’evoluzione in atto.
Come insegna la TPS l’errore più grande è interrompere la continuità nel voler migliorare.
“Quello che oggi è qualcosa di fenomenale, domani potrebbe essere pura normalità.”
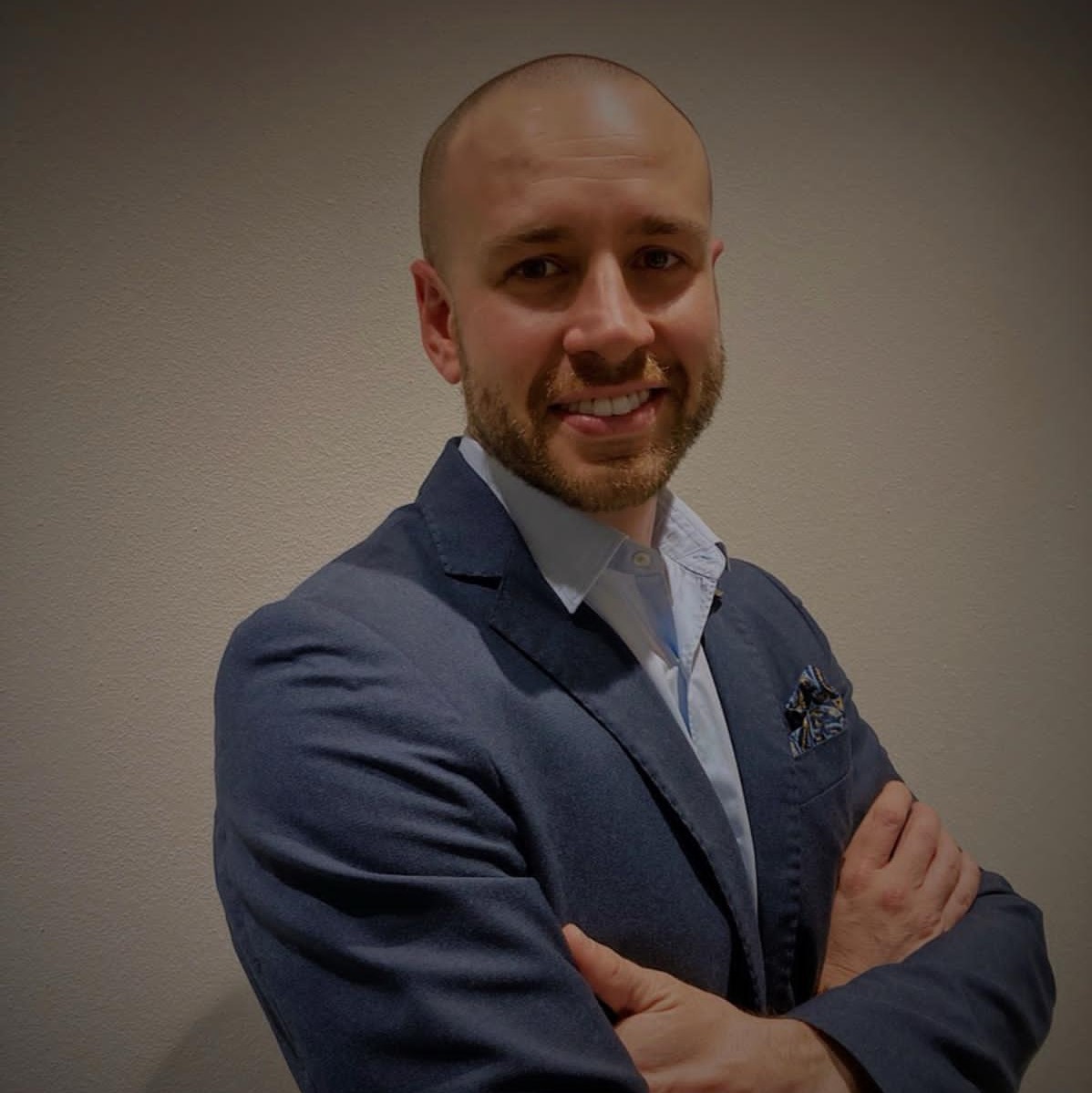
Andrea Micheli
Classe 1986 Planning Manager, Lean Production.
Sviluppo pianificazione e project manager in ambiente Engine to Order
Mental Coach certificato University Coaching in collaborazione con Sport Team Bocconi di Milano.
I MUDA, gli sprechi produttivi del sistema Lean
Approfondisci anche tutti gli altri 7 MUDA o sprechi della Lean Production
Sei interessato a maggiori informazioni sull'efficientamento industriale e aziendale? Leggi anche:
- Che cos'è la Lean Production e come funziona
- BPR Business Process Management
- Innovation Manager: chi è e come opera in azienda
- Supply Chain Management e la digitalizzazione
- POC Proof Of Concept: che cos'è e come può aiutarti
Chiedici una consulenza gratuita
I nostri esperti sono a tua disposizione!
Gli operatori circolano nei reparti della tua azienda con fogli di carta? La pianificazione della produzione è manuale o effettuata con Excel?
Sai esattamente quanto è il tuo livello di produzione? Quanto scarto produci? Quante rilavorazioni per inefficienze? Quante materie prime impieghi?
Tramite un processo di efficientamento è possibile implementare soluzioni tengibili, per ottimizzare al meglio ogni processo e migliorare il livello di efficienza.
Tutto il nostro team è a tua disposizione, per qualunque esigenza.
Leggi i Tutorials più recenti
Strumenti per efficientare le imprese
Core Tools Automotive: l’importanza degli strumenti “Core”
Core tools automotive: gli strumenti chiave da conoscere per lavorare come controller, project manager e dirigenti nel settore automotive.... [Continua a Leggere]
Metodo Hoshin Kanri per la pianificazione strategica
Hoshin Kanri è un metodo di gestione strategica della lean production che permette di allineare gli obiettivi strategici di un'azienda con le sue operazioni quotidiane... [Continua a Leggere]
ESRS: gli standard europei per il reporting sulla sostenibilità
ESRS: gli standard che definiscono le linee guida per la rendicontazione sostenibile delle aziende in Europa. Scopri cosa sono in questo articolo... [Continua a Leggere]
CSDDD o CS3D: cosa è e cosa prevede la nuova direttiva europea
CSDDD o CS3D perché è nata questa normativa europea? a chi è rivolta? entro quando entrerà in vigore?... [Continua a Leggere]
Sostenibilità aziendale: come migliorare le performance sostenibili
La sostenibilità aziendale è un concetto fondamentale per le aziende moderne. Come implementare soluzioni sostenibili per il prossimo futuro?... [Continua a Leggere]
Balanced scorecard: la guida completa
Balanced Scorecard BSC è la scheda di valutazione bilanciata per la gestione strategica e la misurazione dei risultati aziendali nelle diverse aree.... [Continua a Leggere]
Analisi PEST e analisi PESTEL
Analisi PESTEL (anche conosciuta come PEST o PESTLE) permette di evidenziare tutti i fattori esterni che possano condizionare lo sviluppo di una azienda o business... [Continua a Leggere]
La Carbon Footprint aziendale: 9 tecniche e metodi per la stima degli impatti di emissioni in atmosfera
Carbon Footprint aziendale: tecniche e metodi per la stima degli impatti di emissioni in atmosfera e rendicontazione nel bilancio di sostenibilità... [Continua a Leggere]
Margine di Contribuzione: Cos’è, Calcolo ed Esempi
Il margine di contribuzione è un indice fondamentale per valutare la redditività dei prodotti creati dall'azienda. Leggi questo articolo per saperne di più... [Continua a Leggere]
Just in Time: efficienza in produzione e logistica
Il just in time è una strategia di gestione che permette di ridurre gli sprechi e rendere più efficiente e coordinato il reparto produzione.... [Continua a Leggere]
WBS (Work Breakdown Structure): cos'è e come utilizzarla
La WBS è lo strumento di ripartizione del lavoro per suddividerlo in compiti più piccoli e renderlo più gestibile, controllabile e accessibile.... [Continua a Leggere]
Break Even Point (BEP) - come calcolare il punto di pareggio
Il Break Even Point è una formula per calcolare il punto di pareggio. Il valore in cui i profitti e i costi di un’attività aziendale sono in equilibrio.... [Continua a Leggere]
Sistemi di Efficientamento organizzativo
Gli strumenti per efficientare la tua impresa
L'analisi e la mappatura dei processi di un'organizzazione, consentono di riorganizzare le attività, razionalizzare l'uso delle risorse, incrementare l’efficacia, l’efficienza ela produttività della struttura stessa.
I nostri servizi a supporto di imprese:
- Mappatura dei processi interni, gestionali e organizzativi
- Analisi e ottimizzazione delle prestazioni dei processi individuati
- Analisi e riduzione dei costi di gestione
- Ridefinizione dei processi con l'obiettivo di migliorare l'efficienza dell'organizzazione e delle sue prestazioni
- Progettazione di Innovazione tecnologica e digitalizzazione dei processi
- Progettazione di economia circolare