Tempo di lettura: 15 min
Indice
3. DMAIC: Fase 1 - Define o Definizione
- Definire la VOC (Voice Of Customer)
- Definire i Processi aziendali
- Definire la Qualità (Total Quality Management - 6C)
- Che documenti devono essere prodotti alla fine della fase DEFINE?
L’origine del metodo DMAIC
Il metodo DMAIC è uno dei metodi attuativi della Lean Six Sigma.
Che cos’è la Lean Six Sigma?
È una metodologia attuativa che unisce la Lean Production al Metodo Six Sigma, permettendo di applicare i concetti teorici alle pratiche aziendali di tutti i giorni:
- Lean Production: è la metodologia creata da Taiichi Ohno negli anni '60 per gestire la linea di produzione Toyota (TPS Toyota Product System), massimizzando gli utili e minimizzando gli sprechi (costi);
- Metodo Six Sigma: il metodo Six Sigma è stato sviluppato nell’azienda Motorola negli anni '90 ed è una metodologia che si concentra sulla qualità del prodotto attraverso la riduzione dei difetti di processo.
L’unione di questi due metodi crea la metodologia Lean Six Sigma e il Metodo DMAIC.
Che cos’è il Metodo DMAIC?
La parola DMAIC è un acronimo, in cui ogni lettera rappresenta uno step della metodologia:
- Definizione (Define)
- Misurazione (Measure)
- Analisi (Analyze)
- Implementazione (Improve)
- Controllo (Control)
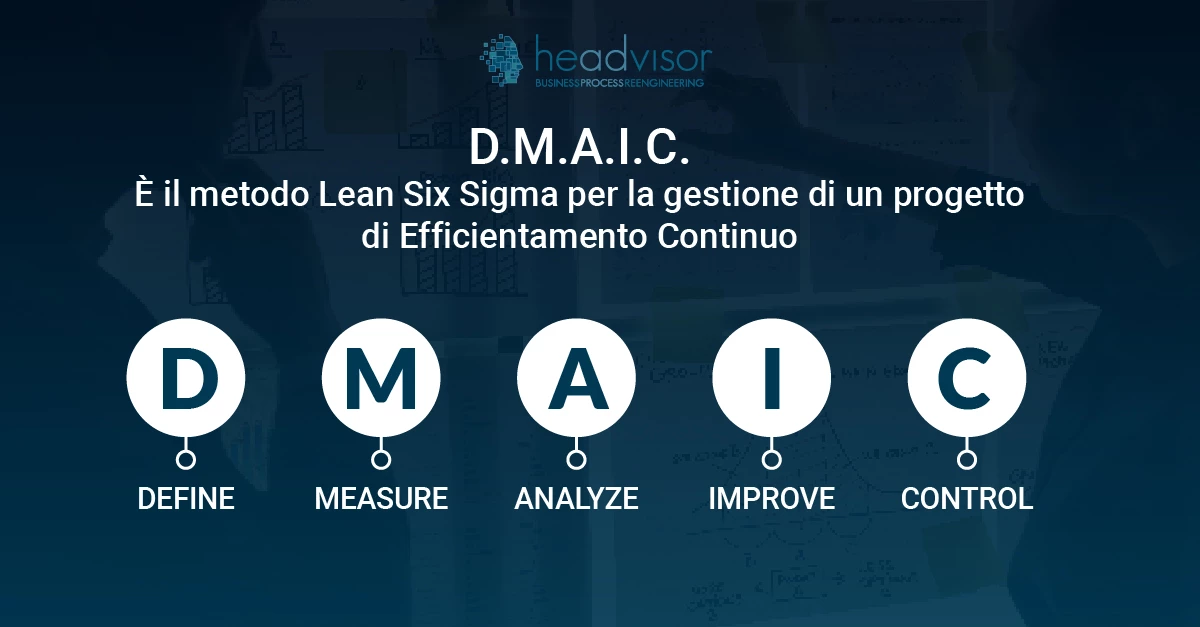
DMAIC: Fase 1 - Define o Definizione
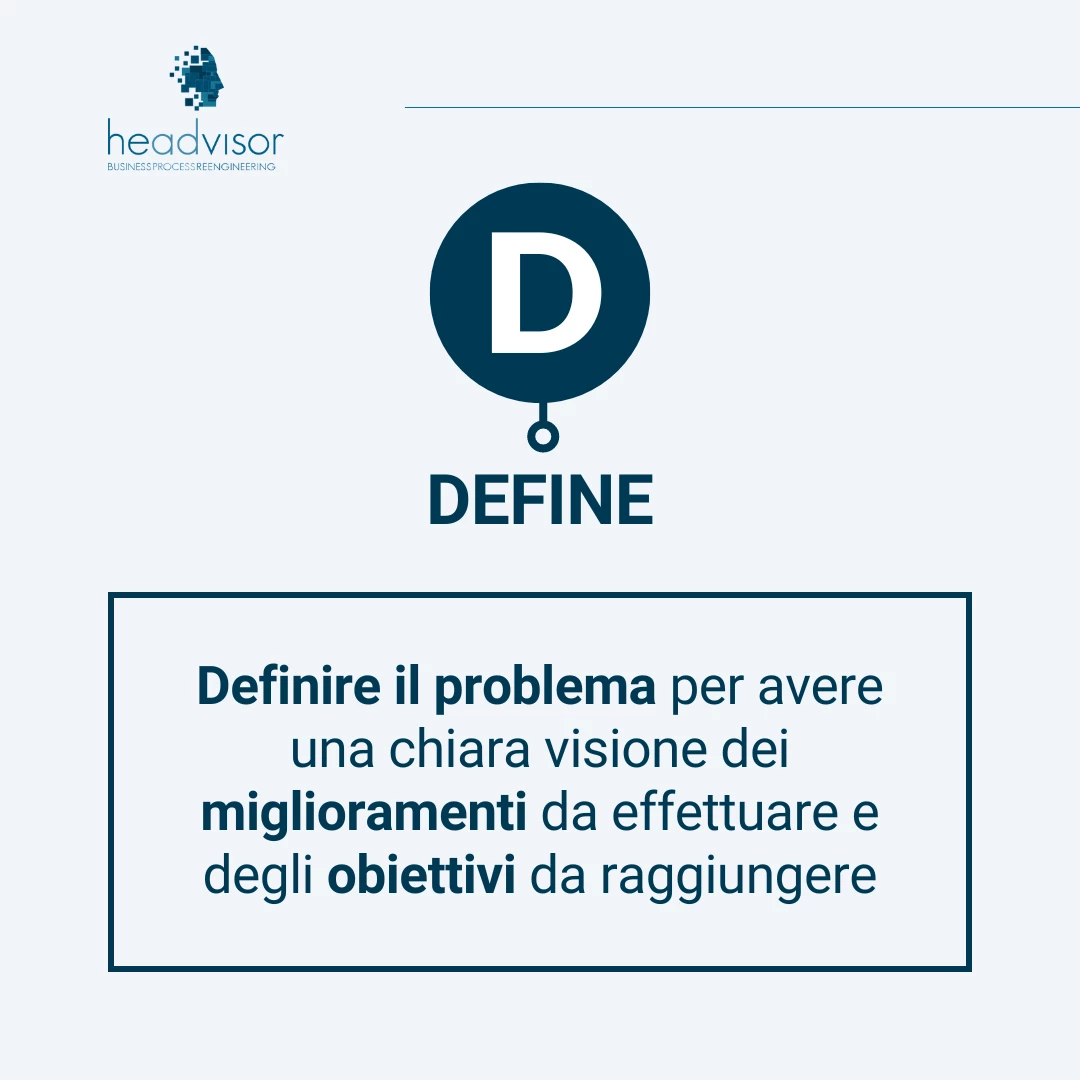
La prima fase è ovviamente definire il problema: questo consente di avere una chiara visione dei miglioramenti da effettuare e degli obiettivi da raggiungere.
Nella fase Define si andrà a definire lo “scenario di riferimento” di un progetto in cui sarà opportuno andare a specificare:
- il problema da analizzare;
- i potenziali destinatari di processo e le loro esigenze;
- indicatori di processo da misurare (CTQ Critical To Quality);
- gli obiettivi che si intendono perseguire con il progetto;
- le risorse necessarie e il tempo di conclusione.
Sempre nella fase Define si ascolteranno le richieste del cliente (Voice Of Customer - VOC) fondamentali per il processo DMAIC: sarà necessario individuare le reali esigenze dei clienti e valutare come essi percepiscono i beni/servizi offerti (anche in confronto rispetto a quelli offerti dai competitors).
Definire la VOC (Voice Of Customer)
La VOC o Voice of Customer, la cui traduzione letterale è “la voce del cliente”, è l'insieme di tutto ciò che il cliente desidera in un prodotto, tutto ciò che ritiene utile e tutto ciò che invece è negativo.
La Voice of Customer può essere misurata con vari strumenti:
Diagramma di Kano
Il diagramma di Kano è uno strumento utilissimo per misurare la VOC, permette di identificare quali sono le caratteristiche necessarie, desiderabili ed indifferenti del tuo prodotto.
È stato inventato da Noriaki Kano, che nel 1984 pubblicò un documento contenente una serie di idee e tecniche per aiutare le aziende a soddisfare le aspettative dei clienti modificando le caratteristiche del prodotto.
Il Diagramma di Kano raggruppa le caratteristiche di un prodotto/servizio in quattro categorie:
- Performance: caratteristiche funzionali che determinano una performance del prodotto che il cliente trova attraente, ma che non sono per forza il fattore decisivo per l'acquisto (un esempio: i consumi di benzina in un’automobile);
- Must-Be: caratteristiche fondamentali che un prodotto deve avere (riprendendo l'esempio dell'automobile la caratteristica Must-Be sono i freni);
- Attraente: caratteristiche che rendono il prodotto più attraente, anche se non incidono sulla sua funzionalità. Sono caratteristiche che stupiscono il cliente e che invitano all'acquisto (un esempio molto calzante sono le automobili che si parcheggiano da sole: molti comprano la macchina anche per questa caratteristica);
- Indifferente: caratteristiche che ai clienti sono indifferenti, su cui non investire tempo perché da esse non dipende l’acquisto (sempre in termini di automobili: l'utilizzo di viti, dadi, bulloni e colle di marche particolari)
L’Analisi di Kano permette di individuare quali sono le caratteristiche che spingono il cliente all'acquisto, quali sono fondamentali e quali sono quelle inutili su cui non si deve investire tempo e lavoro.
Analisi dei Feedback
L’azienda riceverà sicuramente feedback dai propri clienti. Analizzarli attentamente per scoprire quali sono le necessità non soddisfatte permetterà all’azienda di avere una miniera di informazioni utili, perché derivanti da utilizzatori in target.
Definire i Processi aziendali
I processi aziendali sono centrali in un progetto DMAIC: devono essere modellati per rispondere alle necessità del cliente, per questo è necessario analizzarli nel dettaglio, tramite svariati strumenti:
Brainstorming
Il brainstorming è una tecnica che permette di trovare nuove idee e analizzare lo stato dell’azienda. Si svolge con il supporto dell’intero team, pronto ad esprimere le proprie idee, che verranno poi raccolte in un unico documento. Leggi di più sul Brainstorming nel nostro tutorial "Brainstorming: la forza nel team"
Diagramma di affinità
Il Diagramma di Affinità è una tecnica avanzata di Brainstorming utilizzata per organizzare idee, problemi e soluzioni in gruppi connessi tra loro, permettendo una visione schematica dei processi aziendali.
- Definire i processi: diamo per scontato che sia già stato effettuato un Brainstorming per definire i processi e i problemi su di essi riscontrati. In questa fase si presentano le informazioni trovate da questo Brainstorming;
- Generare idee: chiedere a tutti i partecipanti di scrivere nuove idee, nuovi problemi e nuove informazioni correlate ai processi su post-it;
- Presentare le informazioni: appendere i post-it su una parete (o una lavagna) visibile a tutti i membri del gruppo e permettere loro di leggerli e interiorizzare le informazioni;
- Organizzare le informazioni: il gruppo adesso deve organizzare tutte le informazioni in categorie e sotto-categorie, nel modo che appare più appropriato;
- Eliminare le idee duplicate: per rendere più facile l’organizzazione delle idee sarà necessario eliminare tutte le idee duplicate o molto simili;
- Denominare le categorie: una volta raccolte e ordinate tutte le idee sarà possibile nominare tutte le categorie e sotto-categorie trovate;
- Creare collegamenti: cercare collegamenti tra le varie categorie individuate ed esprimerli graficamente in modo da renderli chiari a tutti i partecipanti;
- Preparare una documentazione organizzata: il responsabile del diagramma di affinità lo riprodurrà ora su un supporto cartaceo o digitale e lo renderà disponibile a tutti;
Si svolge in gruppo, composto da tutti gli interessati dal progetto DMAIC e si articola in 8 fasi:
Current State Map
La current state map è una fotografia volta ad immortalare il funzionamento dei processi aziendali prima di cominciare un progetto DMAIC.
È molto utile per chiarire l’esatto funzionamento dei processi per tutti i partecipanti al progetto, ed è indispensabile per fare il confronto dopo la prima implementazione delle misure decise per efficientare. Vuoi sapere di più sulla Current State Map? Leggi il nostro tutorial "Current State Map: le analisi della Lean Production".
Per creare una current state map sono necessari 6 passaggi:
- Definizione dell’ambito: si definisce lo scenario e il contesto della Current State Map, utilizzando strumenti come l’Analisi SWOT e l’Analisi PESTEL;
- Pianificazione della ricerca dei processi umani: si osservano quali problemi esistono nei processi umani, documentandoli e intervistando il personale aziendale;
- Analisi: è necessario analizzare il funzionamento dell’intera azienda, per acquisire tutte le informazioni necessarie a stendere la prima bozza;
- Creazione della Bozza: viene creata la prima bozza della Current State Map, che illustra il funzionamento dei processi aziendali e che deve essere analizzata e migliorata;
- Consolidamento: la bozza della Current State Map deve essere rivisitata e corretta non solo dal personale aziendale ma da professionisti esterni, come Innovation Manager o Consulenti Aziendali esperti;
- Condivisione: la Current State Map deve essere condivisa con tutti in azienda, mettendo in chiaro che è un punto di partenza nel processo di miglioramento continuo;
Metodo SIPOC
Il metodo SIPOC è una strategia per visualizzare quanto e come un’azienda sta soddisfacendo i requisiti del cliente finale. L’utilizzo delle informazioni raccolte da questo metodo permette di creare una mappa di processo.
Il metodo SIPOC permette di mappare i processi aziendali in modo semplice ed efficace, permettendo a tutti i partecipanti del processo DMAIC di comprendere efficacemente dove si trovano i problemi nell’azienda. Si basa si cinque fasi:
- Supplier: elenco dei fornitori del processo, cioè coloro che forniscono gli input per il processo. Possono essere persone, altri processi, aziende, sistemi o applicazioni, sia interni che esterni all’organizzazione;
- Input: individuare gli input richiesti (materie prime, macchinari, strumenti, nozioni, dati, persone);
- Process: descrizione del processo insieme alle attività che lo compongono;
- Output: insieme dei prodotti generati dal processo;
- Customer: i destinatari (o clienti) del processo che riceveranno l’output. Come per i fornitori, possono essere persone, processi, altre aziende, sistemi o applicazioni, sempre interne o esterne all’azienda.
Definire la Qualità (Total Quality Management - 6C)
“Qualità” in ambito aziendale è un concetto relativo: non dipende da fattori fissati o immutabili ma dalle aspettative e dalle necessità dell’utilizzatore finale.
Il concetto di TQM - Total Quality Management è un concetto esteso in ambito aziendale
È fondamentale analizzare il processo di controllo qualità dell’azienda, per comprendere se è attinente alle necessità dei clienti, scoperte tramite l’analisi della VOC.
Definizione delle CTQ
Le CTQ (Critical to Quality) sono letteralmente “Valori Critici per la Qualità”, ovvero tutte le caratteristiche che un prodotto/servizio deve avere per essere considerato dai clienti “di qualità”.
La CTQ è quindi l’elemento cardine su cui operare correttivi al fine di migliorare la qualità del servizio o prodotto. È necessario definire la CTQ per procedere con la Fase Measure. Tutorial per approfondimenti: TQM - Total Quality Management
Che documenti devono essere prodotti alla fine della fase DEFINE?
Project Charter
Il Project Charter è un documento che contiene tutte le informazioni necessarie per lo svolgimento di un progetto DMAIC e che viene distribuito a tutti i partecipanti. Nel Project Charter sono inseriti: i partecipanti al progetto e i loro ruoli, gli obiettivi da raggiungere tramite il progetto, tutte le informazioni raccolte (aggiornate!) e tutte le caratteristiche del progetto;
Risultati delle analisi fatte
Una volta deciso che strumenti utilizzare per analizzare le tre fasi chiave dell’azienda è necessario produrre tutta la documentazione necessaria e custodirla per le prossime fasi.
DMAIC: Fase 2 - Measure o Misurazione
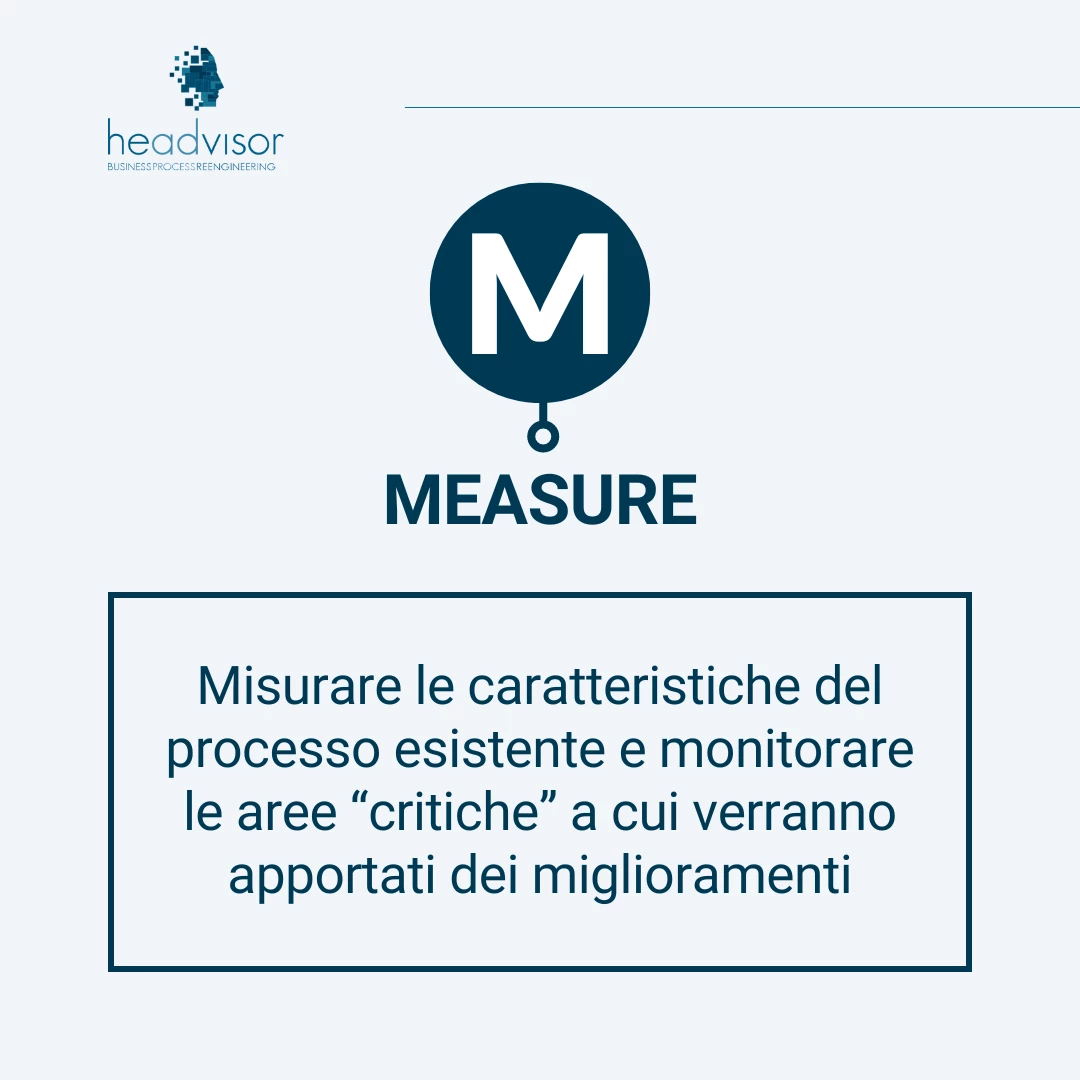
In che cosa consiste la Fase Measure? Analizzare le prestazioni del processo As-Is ossia misurare le caratteristiche del processo esistente e monitorare le aree “critiche” a cui verranno apportati dei miglioramenti. Le attività svolte sono tipicamente le seguenti:
- Pianificazione della raccolta dei dati, necessari alla comprensione del problema
- Validazione del sistema di misura
- Analisi dei rendimenti e della capacità di processo
In questa fase sarà creato un piano di raccolta dati strutturato, per:
- distinguere ciò che sta realmente accadendo da ciò che pensiamo stia accadendo (comprensione del problema)
- confermare o confutare idee, preconcetti e teorie
- stabilire un livello base delle prestazioni
- identificare e comprendere le relazioni che potrebbero aiutare a spiegare la variabilità
Quale è l’obiettivo della Fase Measure?
L’obiettivo della Fase Measure è quello di comprendere al meglio il problema, per concentrare al meglio gli interventi. La Fase Measure è necessaria per permettere il corretto funzionamento della successiva Fase Analyze, perché fornisce i dati reali che verranno poi analizzati.
Quali strumenti sono utilizzati nella Fase Measure?
Diagramma di Pareto
Il Diagramma di Pareto è un grafico che rappresenta l'importanza delle differenze causate da un certo fenomeno e utile a visualizzare gli elementi rilevanti di un sistema. Il Diagramma di Pareto, composto da una serie di barre la cui altezza contiene la frequenza o l’impatto dei problemi dove sulla linea delle ascisse troviamo le cause e sulla linea delle ordinate la loro incidenza in percentuale. Il grafico è utile per analizzare le dinamiche di una tipologia di attività e per accorparle secondo gli effetti osservati;
Graphical Summary
È un modello di rappresentazione dei dati raccolti ed elaborati, che risulta chiara e facilmente comprensibile a tutti coloro che lavorano al progetto. Si compone di: istogramma, box plot, calcolo dell’intervallo di confidenza, test di normalità e calcolo degli indicatori statistici.
DMAIC: Fase 3 - Analyze o Analisi
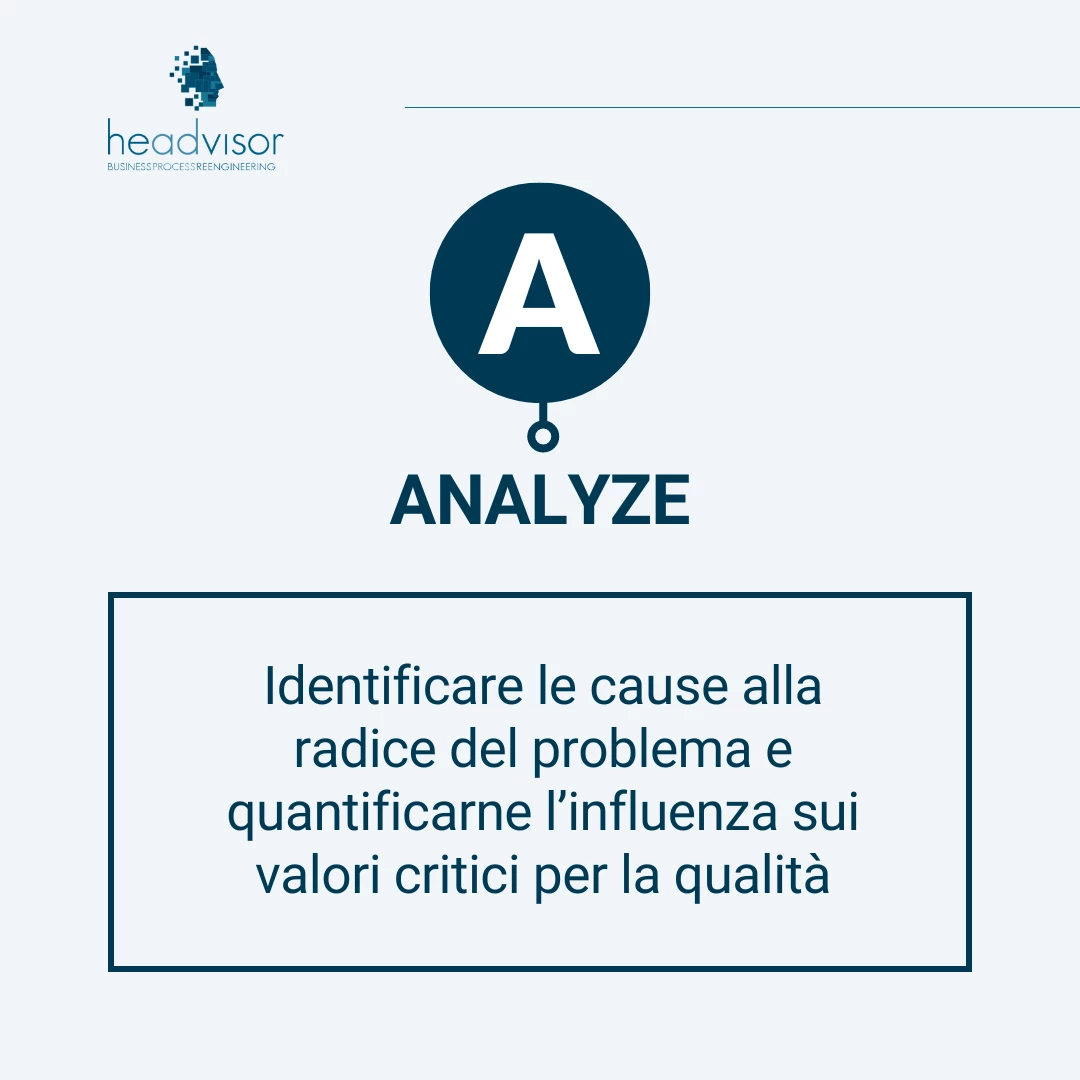
Nella Fase Analyze vengono individuate le poche cause significative che comportano il generarsi di difetti o non conformità. Questa analisi verrà effettuata utilizzando strumenti gestionali e statistici.
Quale è l’obiettivo della Fase Analyze?
L’obiettivo della Fase Analyze è identificare le cause alla radice del problema e quantificarne l’influenza sui valori critici per la qualità (CTQ Critical To Quality: ovvero gli elementi cardine su cui operare per migliorare la qualità di un servizio/prodotto).
Quali sono gli strumenti utilizzati nella Fase Analyze?
Diagramma di Ishikawa
Il Diagramma di Ishikawa, conosciuto anche come diagramma causa effetto o diagramma a lisca di pesce, è stato inventato nel 1969 da Kaoru Ishikawa.
Questo diagramma permette di identificare cause e sintomi dei problemi riscontrati nelle fasi Define e Measure. Il Diagramma di Ishikawa si attua semplicemente disegnando uno schema a lisca di pesce, in cui verranno scritte le eventuali cause del problema rilevato.
Metodo 5 Whys
Il metodo 5 Whys è utilizzato nel campo del problem solving. Si basa su una serie di domande che permettono di analizzare un problema e scoprirne le cause principali (Root Cause).
Come funziona?
Semplicemente si parte dal problema riscontrato, per esempio “ci sono ritardi nella consegna del prodotto finito ai clienti” e si pone la domanda “Perché” 5 o più volte. È ovvio che cinque è un numero arbitrario, l’ideale è porsi la domanda “Perché” il numero di volte necessario per arrivare alla Root Cause del problema.
Utilizzando il nostro problema di esempio “ci sono ritardi nella consegna del prodotto finito ai clienti”, il processo delle 5 Whys si svolgerà così:
PROBLEMA: “Ci sono ritardi nella consegna del prodotto finito ai clienti”
- Perché ci sono ritardi? “La produzione non riesce a rispettare i tempi”
- Perché la produzione non riesce a rispettare i tempi? “I macchinari producono solo per il 50% del tempo di attività”
- Perché i macchinari producono così poco? “I tempi di attrezzaggio sono troppo lunghi”
- Perché gli attrezzaggi sono troppo lunghi? “Il recupero di mescole è lento”
- Perché il recupero di mescole è lento? “Il magazzino è disorganizzato ed è complesso cercare il necessario per la produzione”
Ecco trovata la Root Cause: “Il magazzino è disorganizzato ed è complesso cercare il necessario per la produzione”. Partendo da questa causa sarà possibile risolvere i ritardi.
Tecnica di Regressione
La Tecnica di regressione è uno strumento analitico che permette di sviluppare un modello matematico in grado di descrivere una relazione esistente fra una variabile di Input e una di Output. Viene utilizzato per valutare e analizzare i dati raccolti nella fase Measure in modo da presentare un'analisi futura basata su dati storici.
DMAIC: Fase 4 - Improve o Implementazione
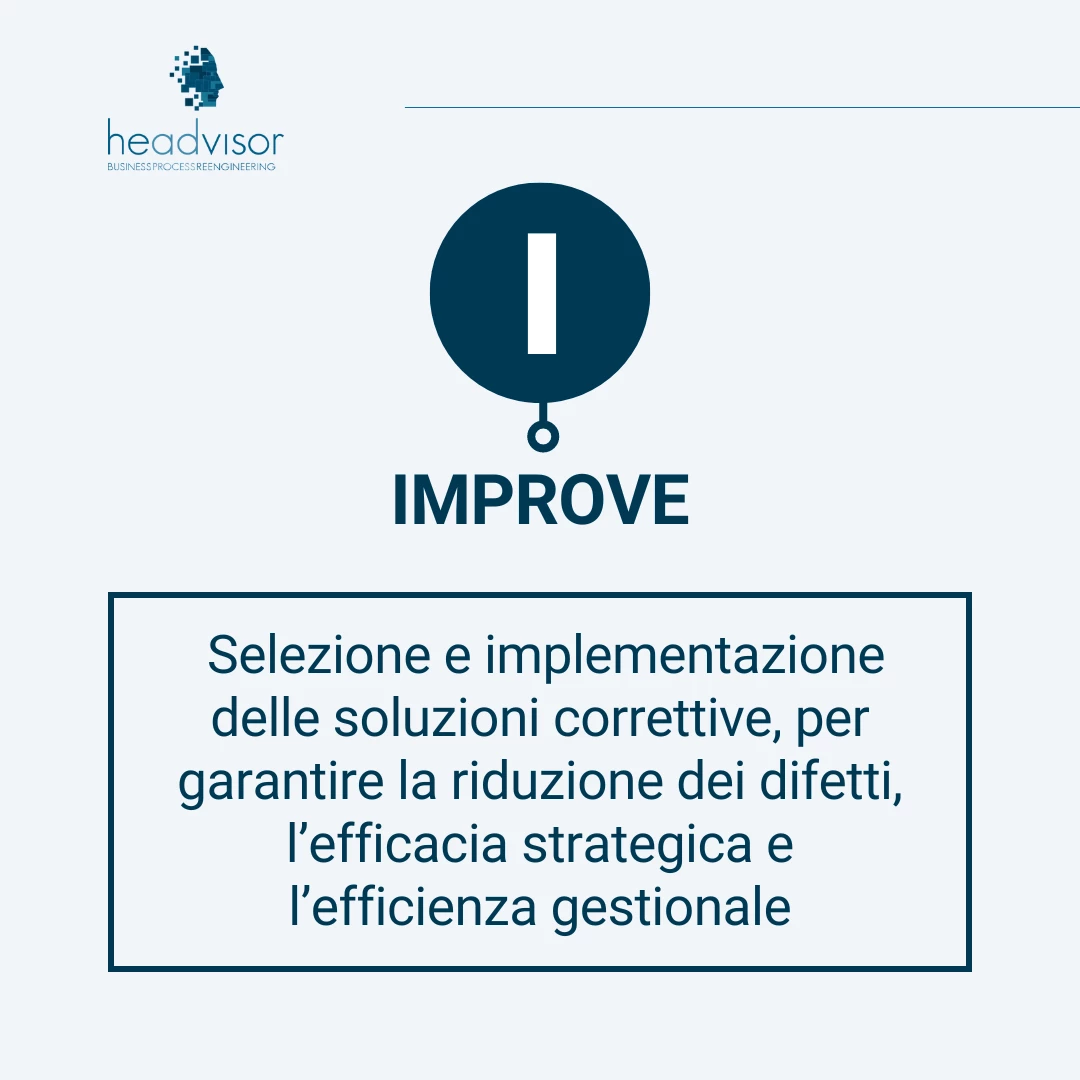
Nella Fase Improve vengono selezionate e implementate le soluzioni correttive, per garantire la riduzione dei difetti, l’efficacia strategica e l’efficienza gestionale.
A questo punto è necessario generare opportunità di miglioramento, sviluppare e implementare soluzioni correttive e pianificare una “prova pilota”, ovvero un prototipo per monitorare l’efficacia delle soluzioni nel breve-medio periodo.
Quali strumenti sono utilizzati nella fase Improve?
Ciclo PDCA
Il ciclo PDCA è uno strumento utilissimo per migliorare i processi e applicare le soluzioni scelte. Si compone di quattro fasi:
- P (Plan – Pianificare): In questa fase il problema viene valutato attentamente e vengono pianificate le possibili azioni correttive;
- D (Do – Fare): Le correzioni vengono applicate e i processi corretti vengono monitorati con un sistema di raccolta dati;
- C (Check – Controllare): Si controllano i dati raccolti, si applicano miglioramenti ai processi e si cercano nuove soluzioni per ciò che non funziona;
- A (Act – Agire): Si applicano tutte le nuove soluzioni e si riparte dal punto 1, per innescare un processo di miglioramento continuo.
Queste quattro fasi del PDCA creano un ciclo di miglioramento, che permette di verificare e correggere tutte le modifiche applicate ai processi.
Design of Experiments
È la progettazione di qualsiasi compito che abbia lo scopo di descrivere e spiegare la variazione delle informazioni in condizioni che sono ipotizzate riflettere la variazione. Questo tipo di analisi permette di verificare che le soluzioni applicate siano efficaci nell’apportare miglioramenti ai processi.
Pensiero Lean
Il pensiero Lean è una strategia operativa che permette di applicare i miglioramenti scelti ai processi, verificarne il funzionamento e applicare le correzioni. Non è però un semplice strumento del DMAIC, ma può essere applicato a qualunque strategia per il miglioramento dei processi (come il Business Process Reengineering).
È un processo di trasformazione che mira a fornire un nuovo modo di pensare, organizzare e agire. Si applica a tutte le attività aziendali perché risultino più efficienti.
Per approfondimenti sul pensiero Lean: “Lean Thinking in azienda”.
Kaizen e Kaikaku
Il Kaizen è la strategia per il miglioramento continuo sviluppata da Taiichi Ohno (TPS Toyota Product System), sulle linee produttive Toyota. Il Kaizen è una metodologia per migliorare i processi aziendali e supporta l’azienda nella fase Improve caratterizzata dal cambiamento continuo per piccoli passi.
Il Kaikaku è una strategia di cambiamento radicale, da applicare in sostituzione del Kaizen, nel caso l’azienda necessiti di una strategia dirompente mirata al cambiamento radicale.
Sono spesso utilizzati alternativamente, in base alle esigenze dell’azienda che deve effettuare il cambiamento.
5S
La metodologia delle 5S si basa sull’idea che un ambiente di lavoro ordinato e pulito sia assolutamente necessario per promuovere il miglioramento continuo e la produttività.
L’espressione metodo 5S trae origine dalle iniziali delle cinque parole giapponesi (ovviamente nella loro pronuncia occidentalizzata) che sintetizzano appunto i cinque passaggi della metodologia:
- SEIRI: Semplificare, scegliere e separare = Classificare attrezzature/strumenti presenti in una postazione lavorativa eliminando ciò che non è strettamente necessario;
- SEITON: Sistemare, ordinare ed organizzare = Posizionare al posto giusto ciò che serve in modo da consentirne facile identificazione, accesso e riposizione;
- SEISO: Splendere, pulire = Mantenere il luogo di lavoro pulito e nello stato di ordine precedentemente costituito;
- SEIKETSU: Stabilizzare e standardizzare = Creare i principi standardizzati per mantenere l’area in ordine ripetendo le tre fasi precedenti e rendere tali principi visibili e applicabili per tutti;
- SHITSUKE: Sostenere nel tempo = Rendere lo standard del metodo 5S un’abitudine e parte del lavoro quotidiano sostenendo l’adeguata disciplina e rigore per il proseguo.
Selezione e Applicazione delle Soluzioni
Questa quarta fase viene conclusa con la selezione delle soluzioni:
- Valutazione delle soluzioni dove si identificano quelle da perseguire portando avanti la soluzione determinata;
- Matrice delle priorità che consente di valutare la migliore fra tutte le soluzioni formulate utilizzando una procedura specifica
- Alcuni possibili criteri di scelta per un progetto di miglioramento possono essere: costo di implementazione, vantaggi potenziali, facilità di realizzazione…
Una volta che le soluzioni sono state scelte vengono applicate ai processi: a questo punto si passa all’ultima fase del ciclo DMAIC, quella di Controllo
Fase 5: Control o Controllo
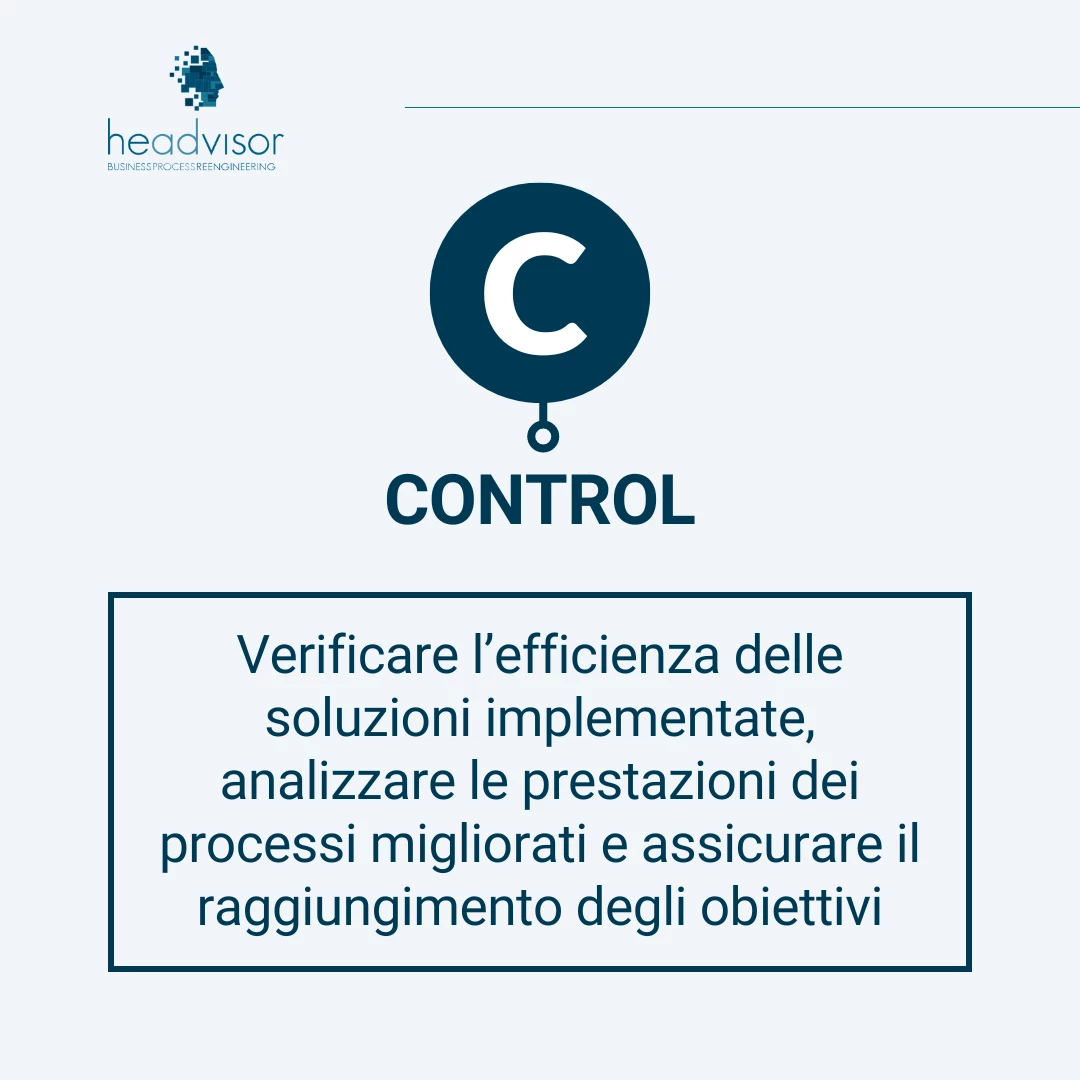
L’obiettivo della fase Control è verificare l’efficienza delle soluzioni implementate, analizzare le prestazioni dei processi migliorati e assicurare il raggiungimento degli obiettivi del progetto.
In questa fase inoltre si standardizzeranno i processi, ovvero verrà definito e finalizzato su carta il metodo di lavoro. Tutte le variabili, le specifiche e le azioni saranno documentate e condivise, per rendere più efficaci i processi e per semplificare il lavoro al personale, che in questo modo diventerà più produttivo.
Quali strumenti sono utilizzati nella fase Control?
Poka-Yoke
Nell’ottica di consolidare i nuovi processi e di prevenire gli errori nella fase Control del processo DMAIC viene spesso utilizzato il Poka-Yoke.
Letteralmente Poka-Yoke significa “ridurre l’errore involontario”, da Poka che significa “errore involontario” e Yoke che significa “evitare” o “ridurre”. È una metodologia della Lean Production, che permette di raggiungere lo stato produttivo “zero difetti”.
Il punto di partenza di questa metodologia è la consapevolezza che nessuna persona, per quanto si impegni, è in grado di evitare completamente gli errori involontari. Per questo la metodologia Poka-Yoke agisce applicando varie misure per prevenire questi errori, in modo da supportare il personale nel lavoro quotidiano evitando gli errori.
Standard Operating Procedure (SOP)
Questo documento fornisce le istruzioni, step by step, per eseguire correttamente tutte le attività di cui è composto un determinato processo.
La Standard Operating Procedure permette di mappare i processi dettagliatamente e di conseguenza permette di conformare il lavoro del personale, minimizzandone la variabilità e rendendo più semplice lo svolgimento delle attività di tutti i giorni.
Avere dei documenti SOP in azienda permette anche di identificare velocemente sprechi ed inefficienze, diminuendo i costi dovuti ad essi.
Statistical Process Control
Un sistema di controllo statistico del processo (SPC Statistical Process Control), che consente di intraprendere il percorso di eccellenza analizzando i processi in modo statistico e rilevando inefficienze, sprechi e colli di bottiglia.
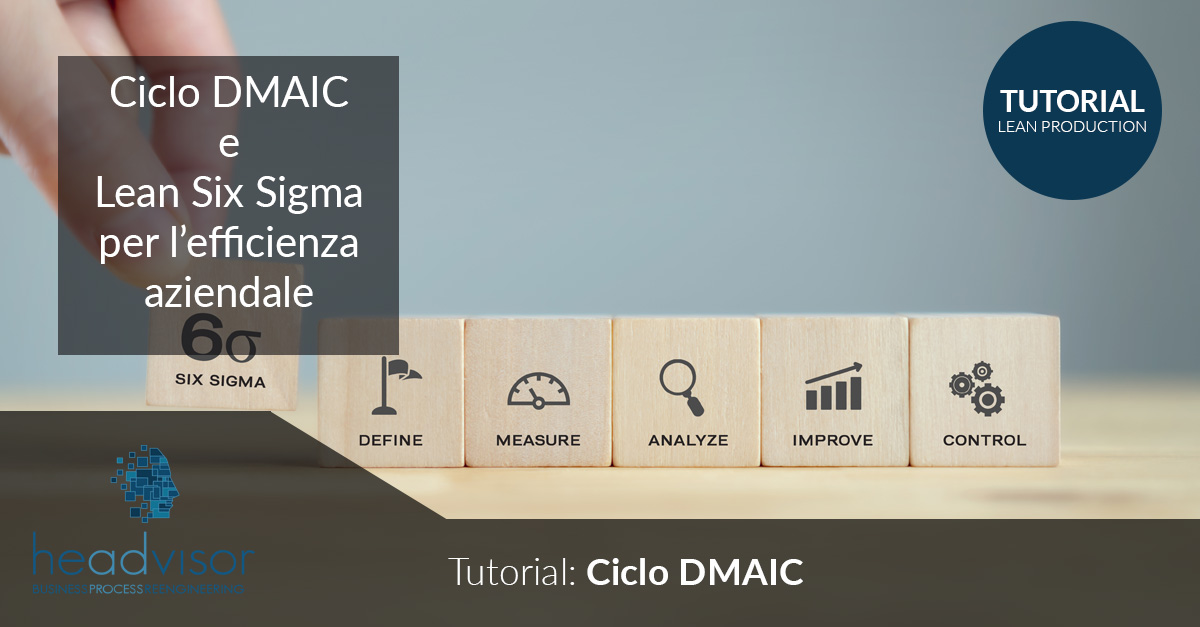
Chiedici una consulenza gratuita
I nostri esperti sono a tua disposizione!
Gli operatori circolano nei reparti della tua azienda con fogli di carta? La pianificazione della produzione è manuale o effettuata con Excel?
Sai esattamente quanto è il tuo livello di produzione? Quanto scarto produci? Quante rilavorazioni per inefficienze? Quante materie prime impieghi?
Tramite un processo di efficientamento è possibile implementare soluzioni tengibili, per ottimizzare al meglio ogni processo e migliorare il livello di efficienza.
Tutto il nostro team è a tua disposizione, per qualunque esigenza.
Leggi i Tutorials più recenti
Strumenti per efficientare le imprese
Core Tools Automotive: l’importanza degli strumenti “Core”
Core tools automotive: gli strumenti chiave da conoscere per lavorare come controller, project manager e dirigenti nel settore automotive.... [Continua a Leggere]
Metodo Hoshin Kanri per la pianificazione strategica
Hoshin Kanri è un metodo di gestione strategica della lean production che permette di allineare gli obiettivi strategici di un'azienda con le sue operazioni quotidiane... [Continua a Leggere]
ESRS: gli standard europei per il reporting sulla sostenibilità
ESRS: gli standard che definiscono le linee guida per la rendicontazione sostenibile delle aziende in Europa. Scopri cosa sono in questo articolo... [Continua a Leggere]
CSDDD o CS3D: cosa è e cosa prevede la nuova direttiva europea
CSDDD o CS3D perché è nata questa normativa europea? a chi è rivolta? entro quando entrerà in vigore?... [Continua a Leggere]
Sostenibilità aziendale: come migliorare le performance sostenibili
La sostenibilità aziendale è un concetto fondamentale per le aziende moderne. Come implementare soluzioni sostenibili per il prossimo futuro?... [Continua a Leggere]
Balanced scorecard: la guida completa
Balanced Scorecard BSC è la scheda di valutazione bilanciata per la gestione strategica e la misurazione dei risultati aziendali nelle diverse aree.... [Continua a Leggere]
Analisi PEST e analisi PESTEL
Analisi PESTEL (anche conosciuta come PEST o PESTLE) permette di evidenziare tutti i fattori esterni che possano condizionare lo sviluppo di una azienda o business... [Continua a Leggere]
La Carbon Footprint aziendale: 9 tecniche e metodi per la stima degli impatti di emissioni in atmosfera
Carbon Footprint aziendale: tecniche e metodi per la stima degli impatti di emissioni in atmosfera e rendicontazione nel bilancio di sostenibilità... [Continua a Leggere]
Margine di Contribuzione: Cos’è, Calcolo ed Esempi
Il margine di contribuzione è un indice fondamentale per valutare la redditività dei prodotti creati dall'azienda. Leggi questo articolo per saperne di più... [Continua a Leggere]
Just in Time: efficienza in produzione e logistica
Il just in time è una strategia di gestione che permette di ridurre gli sprechi e rendere più efficiente e coordinato il reparto produzione.... [Continua a Leggere]
WBS (Work Breakdown Structure): cos'è e come utilizzarla
La WBS è lo strumento di ripartizione del lavoro per suddividerlo in compiti più piccoli e renderlo più gestibile, controllabile e accessibile.... [Continua a Leggere]
Break Even Point (BEP) - come calcolare il punto di pareggio
Il Break Even Point è una formula per calcolare il punto di pareggio. Il valore in cui i profitti e i costi di un’attività aziendale sono in equilibrio.... [Continua a Leggere]
Sistemi di Efficientamento organizzativo
Gli strumenti per efficientare la tua impresa
L'analisi e la mappatura dei processi di un'organizzazione, consentono di riorganizzare le attività, razionalizzare l'uso delle risorse, incrementare l’efficacia, l’efficienza ela produttività della struttura stessa.
I nostri servizi a supporto di imprese:
- Mappatura dei processi interni, gestionali e organizzativi
- Analisi e ottimizzazione delle prestazioni dei processi individuati
- Analisi e riduzione dei costi di gestione
- Ridefinizione dei processi con l'obiettivo di migliorare l'efficienza dell'organizzazione e delle sue prestazioni
- Progettazione di Innovazione tecnologica e digitalizzazione dei processi
- Progettazione di economia circolare