Tempo di lettura: 10 min
Indice
Il Metodo Headvisor: i 7 Step
Il modello operativo di eccellenza del “miglioramento continuo”, contribuisce a garantire nell’organizzazione la crescita virtuosa verso l’eccellenza e il rispettivo mantenimento di ottimi livelli di controllo.
I vantaggi si propagano sui clienti, fornitori, operatori, investitori, e tutte le entità in contatto con l’azienda. Nel difficile mondo della competitività, l’azienda che persegue il “miglioramento continuo” otterrà maggiori vantaggi in termini di efficienza, controllo e gestione del cambiamento.
Dobbiamo abbracciare l'eccellenza attraverso il perseguimento dell’efficientamento continuo. Ciò significa migliorare ogni parte della produzione aziendale e delle capacità post-vendita. In particolare, i nostri processi aziendali interni devono diventare precisi e puntuali come un orologio. Si tratta di fare tutto ciò che facciamo nel miglior modo possibile, riducendo gli sprechi e gli errori.
Rendere i processi produttivi eccellenti significa meno frustrazione per gli operatori oltre a rendere le nostre imprese un ottimo posto in cui aver voglia di potervi lavorare.
Tutti noi abbiamo la possibilità di rendere migliore il nostro lavoro, quando ci vengono dati gli strumenti giusti per farlo!
I vantaggi del Metodo Headvisor
Il metodo Headvisor è composto da 7 macro fasi sviluppate per migliorare l’efficienza aziendale e impostare un ciclo virtuoso di miglioramento continuo che potrà essere mantenuto e sostenuto anche nel lungo periodo, con enormi benefici per l’intera organizzazione.
Questo metodo si basa su diversi strumenti provenienti da diversi ambiti, i quali ci permettono di reingegnerizzare i processi, rendendoli efficienti e in linea con le reali esigenze dell’impresa.
Tra questi vi sono la Lean production, Six Sigma, il metodo DMAIC, l’Operational Excellence e la Digital Transformation.
La logica del miglioramento continuo (nota nella Lean Production come Kaizen) contribuisce a garantire la crescita virtuosa dell’organizzazione nel medio-lungo periodo, rispettando i capisaldi legati al core business aziendale e mantenendo ottimi livelli di controllo.
I benefici derivanti dal metodo Headvisor e da una visione che mira all’Operational Excellence si propagano non solamente all’interno dell’impresa, ma anche sugli stakeholder come clienti, fornitori, operatori e investitori, migliorando notevolmente anche la Brand Reputation.
In un contesto economico in continua evoluzione il perseguimento del miglioramento continuo permette migliorare la competitività dell’azienda, mantenere elevato il livello di innovazione e creare una realtà all’avanguardia sotto ogni punto di vista.
Raggiungere l’efficienza produttiva significa inoltre migliorare ogni parte dell’apparato produttivo aziendale, partendo dalla produzione, alla fornitura, ala gestione del magazzino fino alle attività post vendita.
I processi interni devono agire in modo preciso ed efficiente, svolgendo ogni attività nel miglior modo possibile e riducendo sprechi e costi di produzione.
Ecco I 7 strumenti per aumentare l’efficacia aziendale!
STEP 1: Analisi di valore, Value Stream Mapping
Il primo passo per raggiungere l’efficienza operativa è di comprendere il contesto aziendale in cui andremo ad operare i le azioni di efficientamento, avendo così una panoramica dello stato dell’azienda.
Le domande da porsi sono le seguenti:
- Quando vendo un prodotto o un servizio, cosa il cliente sta pagando?
- Com’è organizzato il flusso di lavoro per generare il valore?
- Quali membri del team stanno svolgendo determinate attività?
- Come vengono gestiti i processi e la documentazione?
- A chi spetta la responsabilità relativa alle diverse fasi del processo produttivo?
Il successo di un’azienda dipende dall’avere un personale vario, che si occupa e ha competenze in diverse aree del business. Per questo a volte comprendersi e lavorare insieme può essere difficile. Dato che non sappiamo esattamente come si svolge il lavoro dei colleghi, potremmo avanzare richieste difficili o avere aspettative che differiscono molto dalla realtà.
Ecco che entra in gioco la mappatura dei processi (tramite analisi As-Is, Current State Map e Value Stream Map) in cui evidenziare la produzione del valore: un documento che permette di tenere traccia dei processi operativi, aiuta a capire come è organizzato il lavoro dei team, permette di capire esattamente chi deve fare cosa e quando deve farla.
La Value stream Map oltre che a evidenziare come e quando l’azienda produca valore, mette soprattutto in risalto eventuali inefficienze di processo, attese o sprechi.
Le mappe di processo sono utili a tutte le aziende e a tutti i reparti, dalla produzione agli uffici amministrativi.
Come si crea una mappa di flusso?
Il primo passo è sempre il brainstorming: tutte le persone in un team/reparto devono sedersi insieme e ragionare sulle attività giornaliere: quali sono i compiti assegnati ad ognuno? Quali sono le attività che si ripetono sempre? E quelle rare? Chi è l’autorità che controlla l’andamento dei lavori? Come fa a capire se il tempo impiegato per un’attività è adeguato/eccessivo/insufficiente?
Il secondo passo è fotografare in modo chiaro il processo tramite il quale un determinato lavoro deve essere svolto, le tempistiche e come queste variano in base al variare della quantità di lavoro o delle persone coinvolte.
Gli Strumenti per la mappatura del flusso: analisi As-IS e Value Stream Map
Lo strumento che utilizzeremo per l’analisi di contesto è l’analisi As-Is, che permette di analizzare e comprendere i processi esistenti, i fattori che li influenzano e la gerarchia delle responsabilità interne all’azienda, avendo così una visione chiara dell’azienda in cui andremo a operare e delle persone con cui collaboreremo.
Attraverso la Value Stream Map (VSM) e la Current State Map (CSM) si esegue invece la mappatura dei processi, evidenziando come viene prodotto valore in azienda.
Questo strumento permette perciò di rappresentare visivamente tutte le fasi e i processi necessari per realizzare un prodotto o un servizio. In questa fase può essere fondamentale eseguire un brainstorming con i membri del team aziendale, in modo da descrivere le attività svolte ed individuare eventuali problematiche all’interno dei processi.
STEP 2: i 7 Muda (Sprechi)
Il passo successivo è quello di identificare quanti più sprechi possibile che intralciano il buon flusso nella produzione del valore. Tutte le inefficienze o sprechi si definiscono come MUDA (i 7 MUDA), perdita di valore, e dalla filosofia della Lean production sono suddivisi in 7 storiche macrocategorie (più una ulteriore macrocategoria più moderna).
Poche cose nella vita sono perfette, soprattutto sul posto di lavoro.
Sappiamo tutti che nell’azienda in cui lavoriamo ci sono processi/lavorazioni che non funzionano al meglio e che potrebbero essere ottimizzate, ma prima di cominciare a migliorare queste inefficienze bisogna capire esattamente dove sono i veri problemi.
Uno dei sistemi per individuare le inefficienze e gli sprechi è il sistema dei 7 MUDA o 7 Sprechi (più uno).
Già nella fase di mappatura del processo produttivo sorgeranno diverse inefficienze, le quali andranno suddivise nelle 8 tipologie di muda.
In questo modo saremo in grado di capire quali sono i problemi che impattano maggiormente sulle performance dell’azienda, agendo in modo organizzato e secondo la logica del miglioramento continuo.
I Muda sono identificabili come le attività che non aggiungono valore al prodotto offerto al cliente (NVA – Not Value Added) aumentando i costi del processo produttivo. Il valore viene infatti deciso dal cliente, il quale può essere disposto a pagare cifre maggiori per prodotti di qualità, ma certamente non per sprechi e inefficienze lungo la catena di produzione.
I 7+1 Muda identificati dalla Lean Production sono i seguenti:
MUDA Trasporto
La prima tipologia di spreco è quella relativa ai trasporti. Il Muda trasporti si verifica nel momento in cui si muovono merci, materiali, attrezzature e informazioni inutilmente. L’ideale è muovere le cose il meno possibile: posizionare tutto dove serve è molto più efficace, riduce le perdite di tempo e aumenta l’efficienza, oltre ad evitare usure e danneggiamenti.
MUDA Inventario
Il secondo spreco è il MUDA inventario, il quale si verifica quando l’azienda ha una quantità eccessiva di materiale in giacenza, troppi materiali o prodotti finiti a bassa rotazione di magazzino.
Lo stock può diventare una forma di spreco notevole se non viene movimentato spesso. Questo vale sia per il reparto produttivo che per gli uffici. Una quantità eccessiva di lavori in corso crea infatti ritardi ed inefficienze.
Gli sprechi di magazzino possono dunque portare ad un notevole aumento dei costi e creare inefficienze lungo tutto il processo.
MUDA Movimentazione
Il Muda movimentazione, a differenza di quello relativo al trasporto, si riferisce alle persone che devono effettuare spostamenti eccessivi o inutili per svolgere le attività sul luogo di lavoro, come cercare strumenti, raccogliere materiale o richiedere chiarimenti su determinate informazioni.
MUDA Attesa
Il Muda attesa si verifica quando un processo produttivo si interrompe a causa della mancanza di materiali, informazioni oppure forza lavoro e quindi ogni volta che un ritardo crea attesa e perdite di tempo, mettendo in deficit il flusso produttivo.
MUDA Sovrapproduzione
Uno dei capisaldi della Lean production prevede di produrre solamente le quantità di prodotto necessarie per rispondere alle esigenze dei clienti e del mercato, senza produrre nulla più del dovuto.
La presenza di prodotti in eccesso che ristagnano in magazzino crea molti sprechi, dal tempo e dalle risorse per produrre l’eccesso oltre ai costi di spazio, di tempo per lo stoccaggio e il reperire il materiale.
La soluzione al MUDA sovrapproduzione è quella di migliorare la pianificazione delle attività, mettendo in atto alcuni strumenti della Lean Production.
MUDA Sovra-lavorazione
Il MUDA sovra-lavorazione riguarda tutte quelle attività in eccesso e che non creano valore aggiunti al prodotto offerto al cliente (o che offrono qualità eccessiva e che il cliente non percepisce).
In questo modo vengono aggiunte lavorazioni non necessarie e viene sprecato del tempo in attività che non creano il valore che il cliente è disposto a pagare. Questo può anche tradursi nella creazione di documentazione eccessiva o nella misurazione di metriche inutili all’azienda.
MUDA Difetti
Difetti ed errori si verificano spesso lungo il flusso produttivo e creano uno spreco notevole di tempo e denaro. Capire le cause che hanno portato a questi difetti e ridurli al minimo permette di aumentare la produttività e migliorare la qualità del prodotto finale.
MUDA Abilità (ottavo muda)
Esiste un ulteriore spreco introdotto più di recente rispetto ai classici 7 MUDA, Skills, l’ottavo MUDA. Questo tipo di spreco non fa parte dei sette sprechi originali, perché è stato aggiunto solamente negli ultimi tempi, ma è molto importante per l’azienda.
Lo spreco di abilità si verifica quando l’azienda non utilizza e valorizza le capacità dei propri dipendenti, cosa che porta ad un altro tasso di frustrazione e addirittura a dimissioni e turnover generando quindi perdite importanti all’azienda.
Supportare i propri dipendenti significa anche comprendere che ognuno di essi ha capacità particolari che non sempre sono coerenti con il lavoro che stanno svolgendo.
Il sotto utilizzo di queste capacità non è solo un grandissimo spreco per l’azienda ma è anche uno spreco per la persona, che non si sentirà apprezzata e non sentirà di star facendo un lavoro in cui può utilizzare tutte le proprie capacità.
Come individuare i MUDA?
Una tipologia di analisi che possiamo effettuare in questa fase per avere una visione ancora più profonda delle logiche aziendali è la Root Cause Analysis.
Questa tipologia di analisi permette di individuare le cause che stanno alla base delle diverse inefficienze aziendali. Spesso infatti attraverso l’analisi dei Muda vengono individuate solamente le cause superficiali e non quelle profonde che possono creare a cascata altri sprechi aziendali.
Comprendere la causa scatenante risolverà diverse problematiche ed è una soluzione migliore rispetta ad azioni tampone non in grado di risolvere definitivamente la questione.
Altri strumenti che i nostri consulenti utilizzano in questa fase sono il Diagramma di Ishikawa, l’analisi SWOT, l’analisi FMEA e i sistemi di Risk Management.
STEP 3: Proposta attuativa
Dopo le analisi preliminari effettuate nelle fasi precedenti è il momento di proporre una serie di progetti operativi con delle ipotesi riguardo ai costi e tempi necessari alla realizzazione.
La proposta attuativa è basata sui risultati delle analisi effettuate e conterrà il ROI di ogni misura proposta, l’orizzonte temporale di attuazione e le modalità di misurazione dei risultati.
Noi di Headvisor ci proponiamo di sviluppare solo progetti con un payback a 6 mesi o massimo un anno.
Al fine di poter garantire questi risultati sarà necessario valutare per ogni micro progetto il reale COPQ Cost of poor quality.
Solo alla condivisione del costo di inefficienza sarà tangibile il ROI dei progetti sviluppati e poter comprendere la bontà del nostro intervento.
GARANZIA DI SUCCESSO!
STEP 4: Misurazione e monitoraggio dei KPI
All’avvio di ogni singolo microprogetto inizieremo da subito con la messa in opera di fattori di controllo misurabili e tangibili, i KPI.
I KPI Key Performance Indicator sono degli indici di misura numerica in grado di misurare l’efficacia con cui un’azienda, un team o un reparto sta raggiungendo gli obiettivi prefissati.
In questa fase è importante identificare i KPI più significativi, ovvero quelli in grado di fornirci informazioni utili per svolgere con efficacia i processi di miglioramento delle performance aziendali.
I KPI possono essere di “alto livello”, concentrandosi sulle prestazioni complessive dell’impresa, oppure di “dettaglio”, focalizzati sui processi di specifici dipartimenti, come la produzione, il marketing, gli impianti, le risorse umane etc.
I KPI sono utili sia in fase di analisi, per evidenziare le aree in cui l’azienda mostra delle lacune, che in quella operativa, poiché ci permette di comprendere lo stato di avanzamento delle attività e valutare i miglioramenti in corso d’opera.
Inoltre dopo la chiusura del progetto saranno degli strumenti utili per valutare l’effettivo raggiungimento degli obiettivi prefissati e il successo o meno del progetto.
STEP 5: Prototipo
Qualora il sistema di progettazione preveda l’introduzione di impianti o modellazione di molteplici contesti omogenei possiamo sviluppare un prototipo funzionale per effettuare una simulazione della soluzione auspicata e valutare l’impatto che queste avranno sull’impresa.
Per fare ciò è necessario sfruttare un prototipo POC (Proof Of Concept) il quale ci permette di determinare la fattibilità tecnica ed economica dell’idea che vogliamo implementare.
In questo modo possiamo anticipare eventuali problematiche che potrebbero sorgere durante lo svolgimento del progetto di efficientamento, visualizzando il flusso delle attività e organizzandole in modo da ridurre al minimo le possibilità di insuccesso.
STEP 6: Implementazione
Dopo aver approvato il POC Proof of Concept, è il momento di introdurre in azienda le soluzioni pianificate assieme agli eventuali nuovi strumenti e software per la gestione delle attività, come MES, APS, ERP WMS ecc.
In questa fase è fondamentale tenere monitorati i KPI, in modo da valutare il reale impatto delle attività e il rispetto degli obiettivi di progetti determinati in fase di pianificazione. È inoltre importante comunicare con il team di progetti e con i vari membri dell’azienda, tenendoli aggiornati sul progetto e ascoltando i loro dubbi e le loro opinioni.
Eseguire dei Un altro strumento utile è quello di implementare una “procedura del miglioramento continuo”, da sfruttare sia durante il progetto di efficientamento che per le attività future. Si tratta di un documento che tiene traccia dei miglioramenti apportati in azienda e delle nuove idee prodotte dai brainstorming.
STEP 7: Leadership improntata sul miglioramento continuo
Dopo aver completato i processi di efficientamento sarà necessario sviluppare tutte le procedure atte al mantenimento dei risultati ottenuti, implementando delle regole di controllo e sviluppando la filosofia del miglioramento continuo.
La leadership in particolare svolge un ruolo fondamentale in questa fase, poiché se l’intera azienda non è improntata sul miglioramento continuo le operazioni eseguite in precedenza saranno presto disperse e vanificate.
I manager dell’azienda sono coloro che prendono le decisioni, quindi se le decisioni prese non sono nell’ottica del miglioramento continuo tutti i tentativi di rendere l’azienda più efficiente saranno inutili.
Serve introdurre compiti di mantenimento e controllo costante delle procedure e dei processi definiti.
Il sistema di leadership deve integrarsi con i dipendenti aziendali, per raccogliere feedback e scoprire assieme i problemi o i miglioramenti ma soprattutto deve mantenere solido il controllo attraverso la costante raccolta dati delle procedure consolidate.
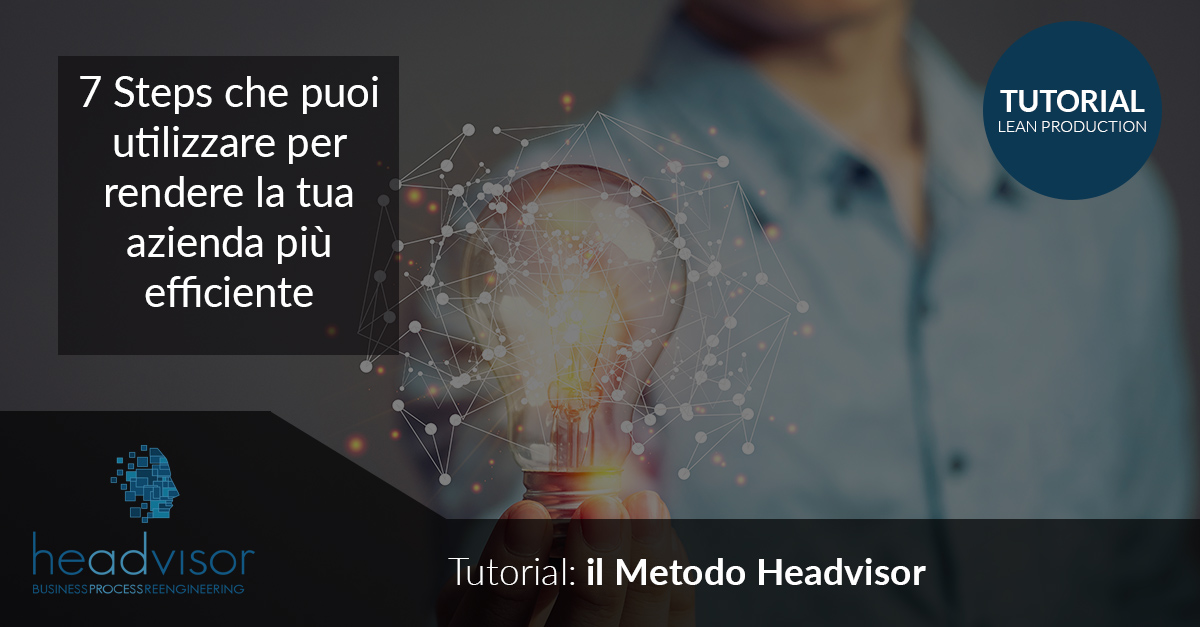
Conclusione
Abbiamo sviluppato questo piano in centinaia di casi, attraverso 7 passaggi chiave possiamo garantire il metodo di migliorare l’efficienza della tua azienda.
Pensiamo assieme come tutti questi strumenti possano essere utilizzati per avviare questo processo.
I nostri advisor possono supportarti in tutte le fasi di efficientamento operativo, dalla mappatura dei processi al mantenimento dei risultati ottenuti, aiutando la vostra azienda a comprendere il funzionamento interno, i punti di forza e I punti di debolezza da correggere.
Sei pronto a partire?
Chiedici una consulenza gratuita
I nostri esperti sono a tua disposizione!
Gli operatori circolano nei reparti della tua azienda con fogli di carta? La pianificazione della produzione è manuale o effettuata con Excel?
Sai esattamente quanto è il tuo livello di produzione? Quanto scarto produci? Quante rilavorazioni per inefficienze? Quante materie prime impieghi?
Tramite un processo di efficientamento è possibile implementare soluzioni tengibili, per ottimizzare al meglio ogni processo e migliorare il livello di efficienza.
Tutto il nostro team è a tua disposizione, per qualunque esigenza.
Leggi i Tutorials più recenti
Strumenti per efficientare le imprese
Core Tools Automotive: l’importanza degli strumenti “Core”
Core tools automotive: gli strumenti chiave da conoscere per lavorare come controller, project manager e dirigenti nel settore automotive.... [Continua a Leggere]
Metodo Hoshin Kanri per la pianificazione strategica
Hoshin Kanri è un metodo di gestione strategica della lean production che permette di allineare gli obiettivi strategici di un'azienda con le sue operazioni quotidiane... [Continua a Leggere]
ESRS: gli standard europei per il reporting sulla sostenibilità
ESRS: gli standard che definiscono le linee guida per la rendicontazione sostenibile delle aziende in Europa. Scopri cosa sono in questo articolo... [Continua a Leggere]
CSDDD o CS3D: cosa è e cosa prevede la nuova direttiva europea
CSDDD o CS3D perché è nata questa normativa europea? a chi è rivolta? entro quando entrerà in vigore?... [Continua a Leggere]
Sostenibilità aziendale: come migliorare le performance sostenibili
La sostenibilità aziendale è un concetto fondamentale per le aziende moderne. Come implementare soluzioni sostenibili per il prossimo futuro?... [Continua a Leggere]
Balanced scorecard: la guida completa
Balanced Scorecard BSC è la scheda di valutazione bilanciata per la gestione strategica e la misurazione dei risultati aziendali nelle diverse aree.... [Continua a Leggere]
Analisi PEST e analisi PESTEL
Analisi PESTEL (anche conosciuta come PEST o PESTLE) permette di evidenziare tutti i fattori esterni che possano condizionare lo sviluppo di una azienda o business... [Continua a Leggere]
La Carbon Footprint aziendale: 9 tecniche e metodi per la stima degli impatti di emissioni in atmosfera
Carbon Footprint aziendale: tecniche e metodi per la stima degli impatti di emissioni in atmosfera e rendicontazione nel bilancio di sostenibilità... [Continua a Leggere]
Margine di Contribuzione: Cos’è, Calcolo ed Esempi
Il margine di contribuzione è un indice fondamentale per valutare la redditività dei prodotti creati dall'azienda. Leggi questo articolo per saperne di più... [Continua a Leggere]
Just in Time: efficienza in produzione e logistica
Il just in time è una strategia di gestione che permette di ridurre gli sprechi e rendere più efficiente e coordinato il reparto produzione.... [Continua a Leggere]
WBS (Work Breakdown Structure): cos'è e come utilizzarla
La WBS è lo strumento di ripartizione del lavoro per suddividerlo in compiti più piccoli e renderlo più gestibile, controllabile e accessibile.... [Continua a Leggere]
Break Even Point (BEP) - come calcolare il punto di pareggio
Il Break Even Point è una formula per calcolare il punto di pareggio. Il valore in cui i profitti e i costi di un’attività aziendale sono in equilibrio.... [Continua a Leggere]
Sistemi di Efficientamento organizzativo
Gli strumenti per efficientare la tua impresa
L'analisi e la mappatura dei processi di un'organizzazione, consentono di riorganizzare le attività, razionalizzare l'uso delle risorse, incrementare l’efficacia, l’efficienza ela produttività della struttura stessa.
I nostri servizi a supporto di imprese:
- Mappatura dei processi interni, gestionali e organizzativi
- Analisi e ottimizzazione delle prestazioni dei processi individuati
- Analisi e riduzione dei costi di gestione
- Ridefinizione dei processi con l'obiettivo di migliorare l'efficienza dell'organizzazione e delle sue prestazioni
- Progettazione di Innovazione tecnologica e digitalizzazione dei processi
- Progettazione di economia circolare